The market for air, water and energy products for blood plasma fractionation and drugs derived from the plasma is approaching $5 billion per year. The market for filtration and separation devices and media is several hundred million dollars. The consumable media segment is substantial, and in part determined by technology advances.
Plasma is a large-volume application compared to many pharmaceutical processes. Nearly 100 million liters of plasma are produced each year. The sources of this plasma are the people of the world.
Fractionation technology is complex. As a result, plasma in developing countries is often discarded and only the red blood is utilized.
Manmade recombinant products have been making inroads into the market. But the human-derived plasma product market is growing at approximately 6% per year and will likely continue to do so over the next five years.
The technology is undergoing significant change. Even the cold ethanol process itself is being challenged by newer technologies. The need to analyze all the technology options is therefore heightened.
Notably, centrifuges compete with depth filter media in the plasma process. GEA has a new separator for plasma separation. Will this change the comparative cost of ownership enough to impact the separation choices? On the other hand, filter press automation could tilt the market in the other direction. These are questions for which the operators will want answers, as will the suppliers.
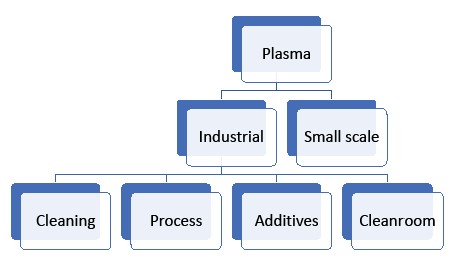
IFN is publishing a series of “True Cost” articles in collaboration with Mcilvaine. Linkage will also be provided to background documents.
Processes
Blood must first be separated into the platelets and plasma. The processes for industrial plasma fractionation processes differ from those used in small-scale operations.
Filtration and separation products are extensively used in the processing but are also used in creating the ultrapure water (water for injection) needed for the clean-in-place or other cleaning systems. There are dilution fluids and various additives used in the fractionation process. Filtration is necessary in their preparation.
Depth filtration media can be used in cartridges, filter presses and disc filters. Some designs combine depth filters and ultrafilters in diafiltration.
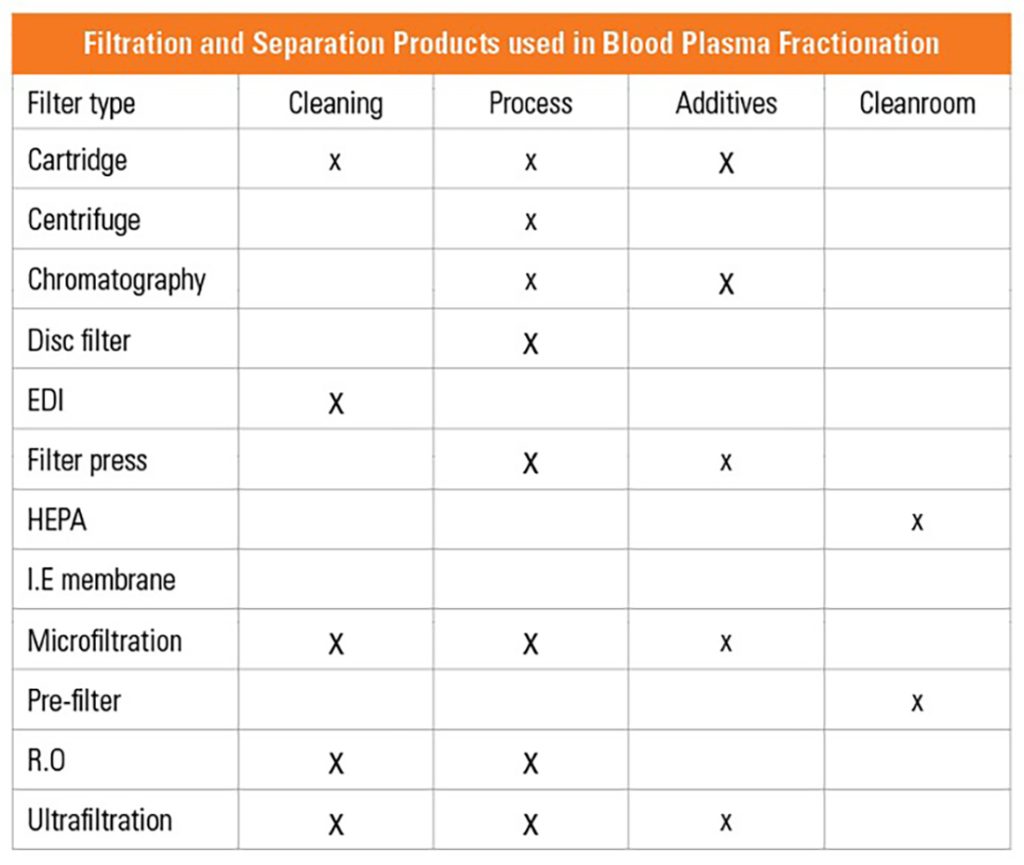
Suppliers
HENKEL states that its vertical centrifuge is specially designed for separating the different plasma fractionations. The following advantages are listed:
- Constant product temperature thanks to double-walled centrifuge housing with bottom
- Sterile machine design including feed pipe and suction pipe
- CIP cleaning meets the highest requirements according to GMP
- Clean room solution thanks to sophisticated design and special operating equipment
- Permanent direct drive for higher dynamics and performance
- Low space requirement due to compact design
EMD Millipore is collaborating with Takeda for the development of a Single Pass Tangential Flow system as an alternative to traditional TFF for concentrating a plasma-derived Immunoglobulin G (IgG) solution from 10% to 20%.
Eaton says depth filters are the first choice for the separation of precipitates and clarification processes in dedicated fractionation steps. Because proteins and process parameters, such as ethanol concentration and pH vary throughout the process, it is essential to choose the right filter media for the appropriate process.
Eaton has filter media for plate and frame filters with the following stated advantages:
- High particulate holding capacity
- High efficiency
- High throughput
- Low leachables
- Minimal pre-rinsing
Novasep states that to recover clotting factors, fibrinogen, poly-IgG, specific IgG or α1-antitrypsin, etc., several chromatography steps can be used to reach high purity and quality.
Sartorius reports that attempts to improve the performance of Albumin and IVIG manufacturing processes are focusing on ultrafiltration and diafiltration (UF/DF) steps within downstream processes. Ultrafilters constitute a significant proportion of the consumable costs associated with albumin production. Membrane improvements can reduce these costs.
In a recent IFN article, Adrian Wilson reported on plasma projects at UK’s National Institute for Health Research.1 One effort would produce a filter that removes anti-A and anti-B antibodies from donated plasma so that anyone could receive a transfusion regardless of their blood group. Central to the development is a nonwoven technology by the Nonwovens Innovation Research Institute called Hydrospace, containing an active ingredient for the selective removal of harmful antibodies.
In developing countries, there is research underway to use nonwoven and membrane media filters as a less technology-challenging route to plasma than centrifugation.
Single-use filters have operating advantages, but this generally comes at a higher price point. In another IFN article, authors from Dr. M addressed costs.2 In the case of large-scale production of recombinant protein, production costs using stainless steel equipment can be as low as ≤ $100/gram. Single-use filtration can cost up to $500/gram. The selling price can be $150,000 per gram. Single use can be justified if more product is obtainable. Single-use can be justified if downtime is avoided or efficiency improved. In developing countries where plasma may otherwise be discarded, single-use can certainly be justified.
IFN also recently reported on a new GEA separator, which is self-cleaning and fully automatic. In this completely enclosed three-room concept, the suspended bowl with hood and solids’ trap is located in a clean room mounted below the separator frame, while the drive units are located in a lower-classified room above. The operating elements are also located outside. The valuable solids are discharged automatically from the suspended separator bowl at reduced or full operating speed under sterile conditions.3
Ultrapure water is required for clean-in-place systems. Distillation and membrane filtration are two routes for achieving acceptable water purity. MECO’s packaged RO + EDI solution, the MASTERpak, incorporates pretreatment, reverse osmosis and electrodeionization for efficient, easy-to-implement purified water production, all on a single skid.
Product comparisons
Eduardo Munoz of CRB writes, “If anything stands a chance to replace the classic ethanol precipitation and mechanical separation approach in the future, it will likely be through technological advancements in large-scale chromatography techniques. One of the more promising solutions is the use of expanded bed adsorption chromatography. This is still not a cost-effective solution for most large-scale plasma fractionators. Until then, ethanol fractionation and mechanical separation is here to stay.”
Munoz also says, “From an initial cost point-of-view, filter presses and centrifuges have similar price tags on a per unit basis. However, in a typical large-scale operation, only one filter press is typically needed while two to three centrifuges are required to process the same plasma volume.”
Some manufacturers who use a filter press method are buying spare plates and frames to cut out the times involved with cleaning. Others are installing two filter presses side-by-side that are tied into the same process system. They operate one and then switch to the other one while the first is harvested and cleaned, which drastically improves overall cycle time.
Plan
Background data for plasma fraction filtration and separation is available and will be periodically updated by McIlvaine. In the next two editions of IFN, McIlvaine will provide a deeper-dive analysis of centrifuges and filter-press technology concepts for plasma fractionation.
For more information on the programs highlighted above, please contact Bob McIlvaine at rmcilvaine@mcilvainecompany.com or +1 847 226-2391.
References
- “New filters promise improved outcomes in transfusions and other clinical procedures,” International Filtration News, https://www.filtnews.com/new-filters-promise-improved-outcomes-in-transfusions-and-other-clinical-procedures/.
- “Multi-cycle single-use filter optimizes biopharma processes,” International Filtration News, https://www.filtnews.com/multi-cycle-single-use-filter-optimizes-biopharma-processes/.
- “GEA launches separator for blood plasma fractionation,” International Filtration News, https://www.filtnews.com/gea-launches-separator-for-blood-plasma-fractionation/.