In this new feature, IFN highlights significant research from universities and institutions around the world. If you are a part of a project you would like to highlight, email csmith@inda.org. Please write “IFN Emerging Research Submission” in your subject line in order to apply. Please send a completed press release and/or summary of the research as you would want it to be printed, a link to the university online story (if applicable), and all high-resolution photographs/charts/graphs, short researcher bio(s). All selections could be edited for length.
By Moni Mahesh Ghosh and Sadhan C. Jana, University of Akron
The global plastic waste generated annually is already in the million metric tons and the problem is ever-growing with land filling as the most popular disposal method. It is widely recognized that plastics in landfills will take hundreds of years to degrade1. Among the plastic wastes, polyolefins are most abundant due to their versatile applications and considerable chemical resistance. It is imperative to develop methods to upcycle them (i.e., to recycle this class of materials while adding commercial value to them).
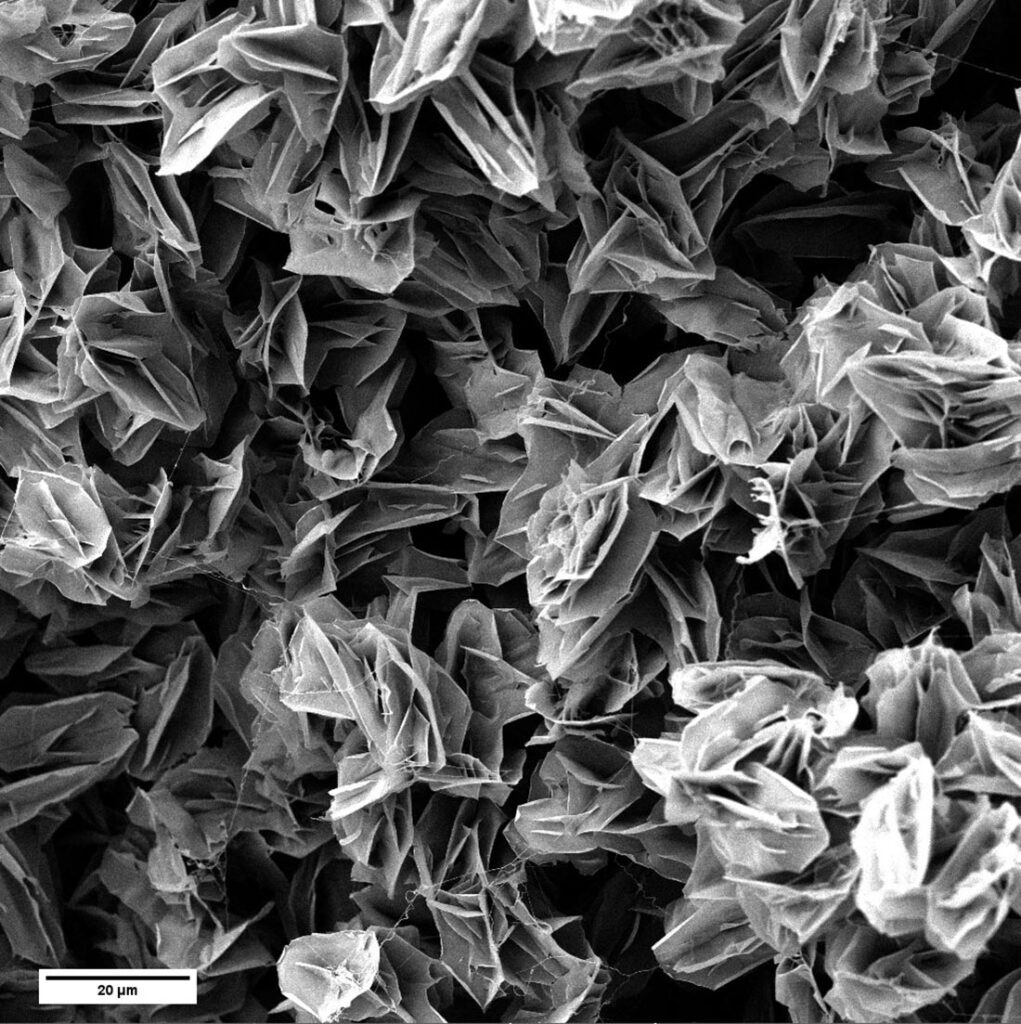
The researchers in Prof. Sadhan C. Jana’s group in the School of Polymer Science and Polymer Engineering at The University of Akron have found a unique method of upcycling polyolefins from waste streams using plant-based solvents known as terpenes. The group investigated the viability of manufacturing highly porous solid structures called aerogels with polyolefins, mainly high-density polyethylene (HDPE) and isotactic polypropylene (iPP) and using them as filter media for oil-water separation and air filtration.
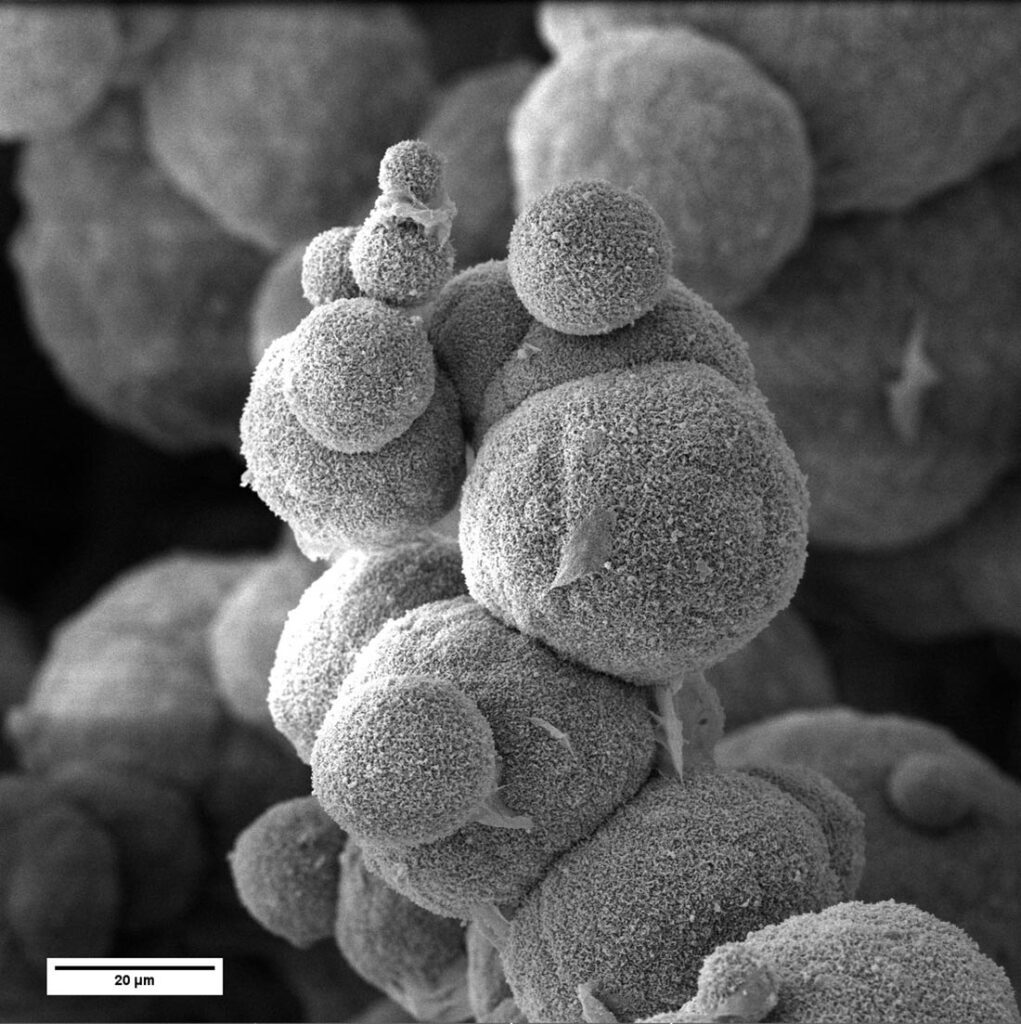
These aerogels are being produced by the method of thermally induced phase separation (TIPS) after dissolving the polymers in two of the more commonly available terpenes – orange terpene derived from oranges and beta pinene derived from pine trees. The properties of these aerogels depend on the solvent used, specific type of polyolefin used (HDPE/iPP), and the weight percent of the polymer in the solution.
The ongoing research focuses on fundamental understanding of the structure-property relationships of the aerogels and their viability as filter media, either as self-standing structures, e.g., as cylindrical monoliths, or in a hybrid structural form, such as supported by 3D-printed scaffolds. The results of the study will be communicated to a peer-reviewed journal. The aerogel specimens were manufactured from both virgin polymer pellets and from segregated polyolefinic waste with either HDPE or PP as the base polymer and with unknown additives. These aerogels were then used in oil-water separation and air filtration and their efficiencies were benchmarked against known commercial filters or materials that are used for similar separation operations, namely, surgical face masks and cellulose-polypropylene based oil absorbents. For some of the aerogel samples that were tested, the air filtration performance was at least 5% more and the oil absorptivity from an oil-in-water emulsion was at least 33% more than the corresponding commercial benchmark materials. The HDPE aerogels had considerably higher compressive strength while the iPP aerogels had considerably higher specific surface area and a higher fraction of mesopores.
It is known in melt-processing that mixed polyolefin wastes do not produce homogeneous materials due to immiscibility of polyolefins. However, the method adopted in this work leads to synergy, in that, co-existing, high-surface area polyolefin phases work in unison to fetter out airborne particles or oil phases. These aerogels can be manufactured in net-shape, thereby opening the avenues for potential applications like oil spill cleanup, modular air filtration, carbon capture etc.
About the researchers:

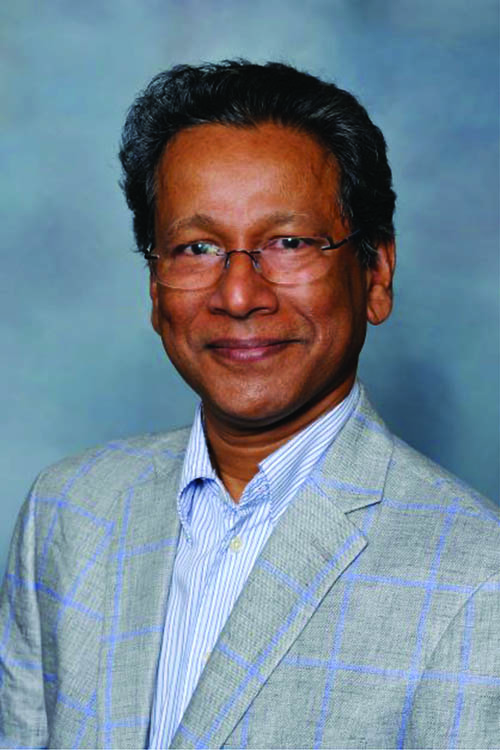
other things. His email is janas@uakron.edu.
Reference:
1. Roland Geyer et al. Production, use, and fate of all plastics ever made. Sci. Adv.3, e1700782(2017).