Fibroline is an engineering company specialized in technology transfer based in France near Lyon. It also has an entity in the United States, in North Carolina. The company has developed and patented several dry powder impregnation solutions, intended to provide efficient and environmentally friendly techniques to functionalize porous structures, and filter media in particular for gas capture such as CO2 or war gases and water treatment, including arsenic removal.
Indeed, these technologies have shown several innovative features that lead to numerous key competitive advantages in different sectors. The principles behind this technology give it capacities unmatched by common liquid impregnation solutions. Using dry impregnation leads to drastic reductions of all clogging effect and significantly increasing performances of impregnated products. An environmentally friendly process, it also leads to significant reductions in energy consumption and waste reduction with the complete removal of effluents.
The Leading Principles Behind Dry Impregnation Solutions
Dry impregnation consists in the distribution of powders in any form into porous structures by the use of high intensity alternating electric fields.
These technologies are available in several configurations, depending on customers’ needs in terms of
targeted materials and production characteristics. Using repulsion of particles grants the capacity to
impregnate in an extremely homogenous way, occupying all of the available space within the given material. It also allows to deposit active porous particles in various ratios, in very large quantities, but also in very small amounts with results that cannot be obtained with conventional liquid impregnation solutions.
Within Fibroline’s technology portfolio, D-Preg is the one that is most used for the technical textile applications and therefore the filtration and separation sector. It is greatly appreciated for its flexibility and adaptability, working with material’s width ranging from 0,15 to 5m wide.
Dry impregnation solutions also allow for pattern deposition. Within the filtration sector, the manufacturer can pick preferred impregnation areas and decide where and how much to spread the powder on desired media. This grants capacity to concentrate functional actives exactly where needed, depending on the air or liquid flow. “Pattern deposition is especially a strong feature of Fibroline’s S-Preg solution, widely used in the medical and biomedical sectors, and can pave the way to new products in the filtration industry,” Léa Monin said, as a R&D project manager in charge of Filtration development at Fibroline.
How These Principles Lead to Improved Performances
Because these technologies are based out of dry impregnation, they do not require any liquid binders, leading to the reduction of clogging effect. Therefore, active in powder form is fully available and this results in much higher efficiency of impregnated products overall. For instance, tests have shown that in the case of liquid impregnation of zeolite, 40% of active surface area got clogged with only 12% rate of latex binder impregnated. Fibroline’s dry impregnation solutions can reduce clogging to less than 7%.
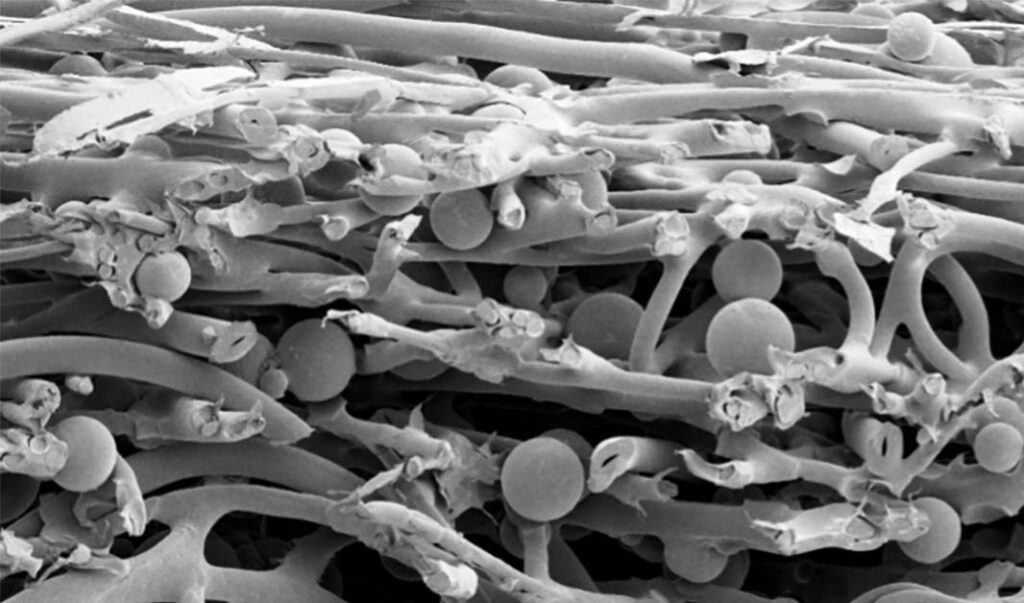
Moreover, the use of actives in powder form also grants capacity to increase the specific surface area of the materials used by the manufacturers. Indeed, by using very thin powder instead of beads or pellets, the product benefits from a much wider active surface, and can therefore provide higher adsorption capacity and faster adsorption and desorption kinetics. A recent study on the capture of organosulfur compounds demonstrated a 105% raise of the adsorption kinetic using 30 microns zeolites instead of 2mm diameters beads at the same loading level.
With powder consisting in porous particles of controlled geometries, it also enables the trapping of targeted molecules selectively, and also increases the active filtration area. This makes Fibroline’s dry impregnation solutions perfectly suited for the use of MOFs, which are continuously growing in use with more and more applications being developed from them.
All in all, thanks to bigger specific surface area compared to beads or pellets and the removal of liquid binders that drastically reduces clogging effect, dry impregnation solution results in higher filter efficiency than conventional methods.
The Notable Features of Dry Impregnation Solutions as Cleantech
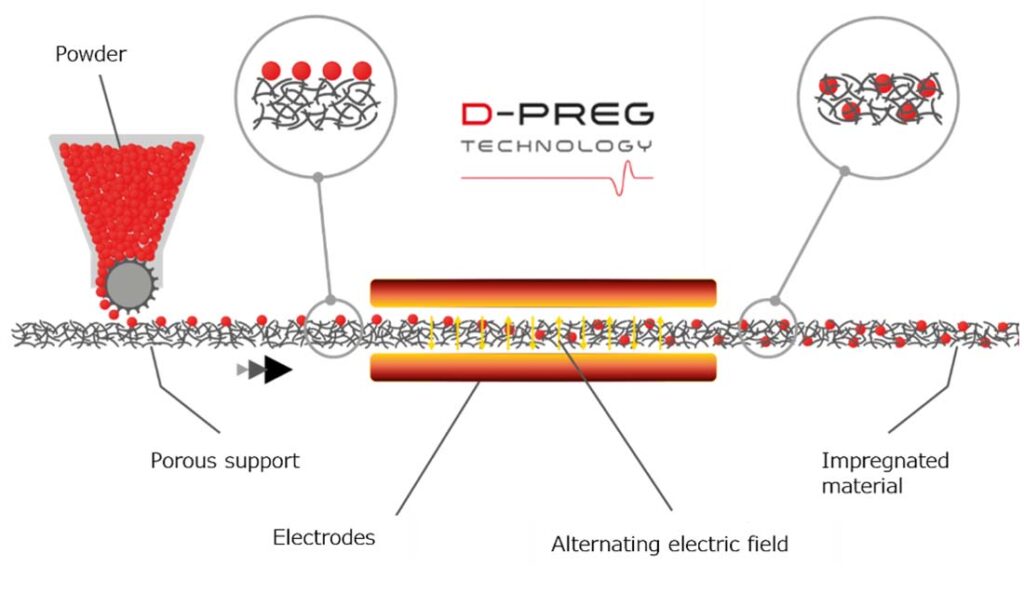
Other pros of dry impregnation technologies reside in their characteristics as distinguished cleantech with several environmentally friendly features. This generates both greater sustainability and major savings for its users.
Replacing technologies that require solvents, these solutions have also eliminated VOCs emissions. For instance, for a recently transferred automotive interior applications, there were 100 time less VOCs emissions using dry impregnation solutions as compared to those of wet impregnation. As these emissions are immensely reduced, the quality of products is greatly improved with the removal of unsafe gases which can be a key benefit for specific applications in dealing with ever more constraining regulations.
Another key strategic aspect of the removal of solvents results in the simplification of industrial production processes. Not only does it make for simplified production lines, but it diminishes risks on industrial sites as it eliminates hazardous situations. They are therefore in accordance with safety regulations worldwide, such as SEVESO norms in Europe.
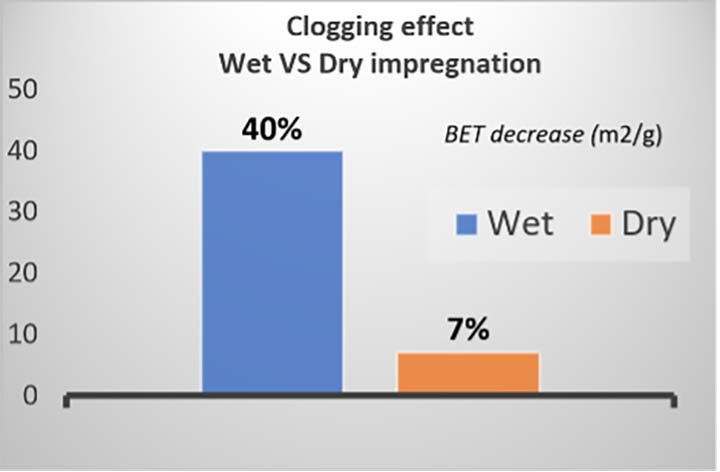
Using dry impregnation instead of liquid solutions also results in better energy efficiency and cost savings for its users. Since the technology does not need energy intensive drying, it can greatly reduce energy consumption. As an example, a 4m long and 1,50m wide unit running at 20m/min, impregnating up to 2T/h material requires less than 15kW. Instead of having to use large ovens to evaporate solvents, dry impregnation solutions can be combined with short thermal treatments resulting in space savings and increased productivity. These savings can be added to those from the complete elimination of effluents in dry impregnation solutions, making the latter all the more attractive.
Not only does it make for simplified production lines, but it diminishes risks on industrial sites as it eliminates hazardous situations.
Conclusion
Dry impregnation solutions bring several key innovations and competitive advantages to manufacturers. The use of alternating electric fields at its core is an innovation that results in improved performance of impregnated products. It is also a cleantech, as it greatly significantly liquid waste and VOCs emissions.
Fibroline does not build and prepare machines, but rather transfers its technologies by application sector. It accompanies its customers to secure a project from the initial idea to the industrial implementation of the solution. Said technologies are protected by numerous patents worldwide, and are continuously extended to new industries.