As advanced gas turbine efficiencies peak beyond 60%, the demands on the air filtration system have never been greater. Backed with a comprehensive R&D programme and decades of operating experience, Parker Hannifin’s innovative clearcurrent® ASSURE filters are a match made in heaven.
With efficiencies beyond 60% in the combined cycle, today’s advanced gas turbines represent a new age of sophistication in understanding heat transfer, blade aerodynamics, and materials science. This evolution has resulted in higher firing temperatures, enhanced air-cooling flow, improved hot gas path components and upgraded thermal coatings that characterise machines like the H and J class turbine. These machines are far superior to earlier generations of machines but, like a thoroughbred racehorse, that performance demands rigorous care and attention.
Given the precision needed to optimize air, fuel, and combustion gases through an advanced gas turbine, one of the most important requirements is a consistent and reliable flow of inlet air. However, just as important as consistent flow is the quality and condition of that air and thus the performance of the inlet air filtration system is critical.
Any contaminants within the air stream that pass through the filterhouse and into the turbine itself can have a huge impact on turbine efficiency. This effect is particularly acute with advanced gas turbines, where even the smallest change in aerodynamic performance can be disastrous for the thermal efficiency of the machine. Larger contaminants, such as dust or particulates, can erode elements of the compressor section or other internals. Damage to the special super alloys, finishes and coatings inside the turbine may lead to severe machine damage and could easily cost millions to repair. Even non-abrasive contaminants such as water or oils can have a substantial impact on performance if they are deposited on the blade surfaces, stators, or other aerodynamic components. For this reason, operators conduct periodic off-line compressor section washes to restore aerodynamic performance but inevitably, this results in costly downtime and lost production.
Nonetheless, the reduction of turbine efficiency associated with contamination passing into the turbine not only increases operational costs, it can also be directly equated to higher greenhouse gas emissions. This is a key metric in assessing business and economic performance in today’s carbon-constrained world. Avoiding these negative outcomes is the primary role of the air inlet filtration system.
Advanced Filters for Advanced Machine Media
While gas turbines have seen continuous improvement over the years, the air filtration systems offered by the leading companies have matched the pace. The extensive R&D programmes undertaken by Parker Hannifin, for instance, have led to numerous breakthroughs in design and technology that have allowed the latest filtration technologies to sustain the impressive performance of the most advanced gas turbines.
Parker’s new range of innovative filters, clearcurrent® ASSURE, have been designed to reflect the needs of today’s advanced gas turbines and bring cutting-edge filtration engineering and Parker’s “performance first” expertise to bear.
Delivering a substantial improvement in filtration efficiency, clearcurrent® ASSURE filters keep turbine internals cleaner for much longer, reducing the frequency of offline washes and sustaining aerodynamic performance for far longer. At the same time, they deliver the predictable differential pressure characteristics that are essential to avoid any sudden pressure spikes that can lead to damage or unplanned turbine outages.
One of the breakthroughs that support the higher efficiencies of the overall system is the use of durable hydrophobic and oleophobic filtration media. By resisting the ingress of particularly troublesome ‘sticky’ contaminants like salt water and oils, the filter materials remove problematic liquid contaminants. Such liquids can also exacerbate problems associated with other contaminants. For example, small droplets of water can combine with dust to form a mud that may block the filter. Moisture can also prompt changes to salt particles, turning them from a solid to a liquid and making them far more challenging for the filtration system.
Using Precision to Prevent Bypass
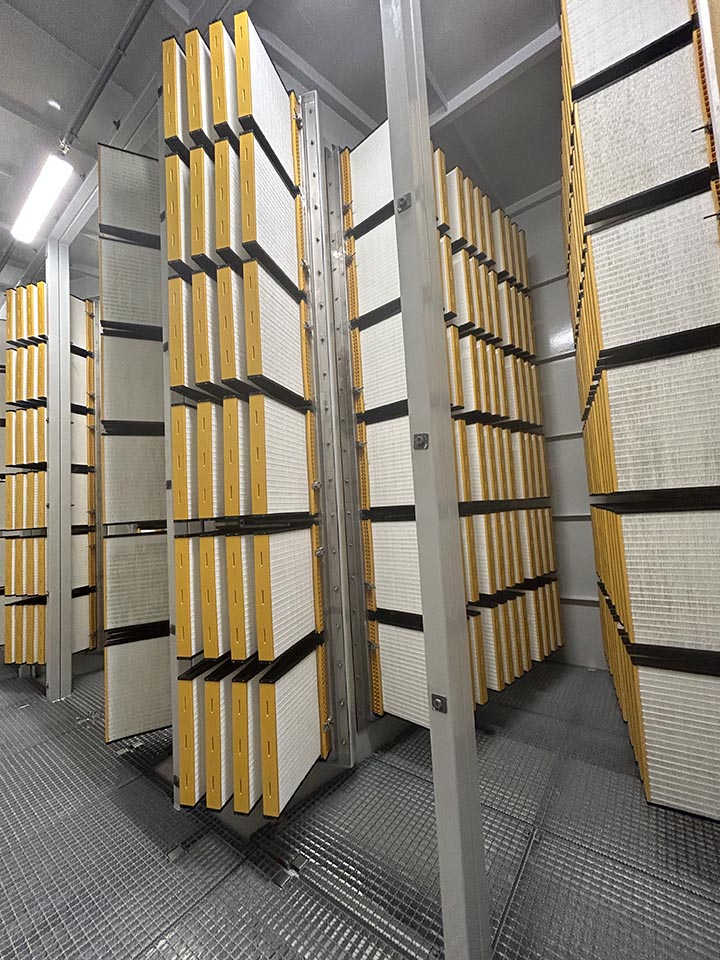
While advances in filtration media represent the potential for a substantial gain in turbine performance there are other factors at play. Even the most sophisticated media can only deliver on its promise if the air actually travels through it and, like any fluid, air will always take the easiest route. Any gaps or leaks will be readily exploited by an air stream that could bypass the filtration system altogether. Parker’s filters are designed for precision engineering and manufacture to prevent bypass and deliver a new benchmark in turbine protection.
An example of this approach comes from the pleating arrangements. In all filtration systems, the filter media is pleated to maximize the surface area, but the folds introduce a natural weakness. Any damage to the pleats that occurs because of that weakness can create a bypass route for air and moisture. A proprietary polyurethane (PU) flow technology ensures an even distribution of sealant through the pleat channels and complete encapsulation of the pleat tips. Edge seal technology may then subsequently be used to apply hot-melt beads at the border of the pleat pack to act as a secondary reinforcement seal. This kind of attention to detail goes a long way to reducing bypass opportunities.
Furthermore, framing and fitment can also have a big impact on performance. Parker’s filters are made to ensure an exact fit in the inlet house to eliminate the possibility of bypass. Wherever possible, secondary fail-safe sealing is also incorporated into the filter design as an additional layer of back-up. Indeed, poor sealing within the filterhouse or in the filter itself is a common issue found in air intake filtration systems, along with inadequate drainage, and sub-optimal weather protection. All of these can contribute to filter bypass and subsequent contamination of the turbine.
Curbing Corrosion
Any turbine operating close to the sea is potentially vulnerable to salt ingress. The corrosive properties of salts are well known, but in the high temperatures found within a gas turbine those corrosive characteristics can be amplified many-fold. Salt can combine with fuel in the hotter areas of the turbine to form corrosive sodium sulphate, for example. As well as adhering to turbine blades, salts and sulphur compounds cannot only corrode the metals within the turbine but also the galvanized steel of the filter house and filter framing. Indeed, gas turbines and their ancillaries face a wealth of environmentally challenging conditions that can promote corrosion. Sulphur dioxide pollution from exhaust fumes, alkalis and cements, chlorides and sulphates from industry, acidic rainwater and cooling tower drift are just some of the corrosive elements at play. Even electrolytic corrosion between dissimilar metals can be a significant factor.
However, while rust is a perennial problem it is rarely dealt with in a comprehensive way in the filtration system. Zinc galvanizing steel does give a degree of protection, but the galvanized metal components in clearcurrent® ASSURE filters are also powder coated. Resistant to cracking, peeling, chipping and abrasion, powder coating provides a robust water-proof sealant that adds years to the life of the components. Over 1,000 hours of accelerated salt spray testing reveals the metal remains virtually unchanged under the engineered powder coating, a dramatically different result when compared with steel that is only galvanized. Such coatings thus ensure the continued high performance of the filtration system and with it the best possible protection of the turbine.
Continuous Performance Improvements with R&D
Given the continuous progress in gas turbine performance, it is clear that further advances are on the way as technologies such as 3D printing, advanced analytics and materials breakthroughs push the efficiency window higher. Further improvements mean 65% efficiency machines are on the horizon and, naturally, air filtration systems must continue to keep pace. With more than 50 years of ground-breaking innovation under its belt, whilst working in partnership with gas turbine manufacturers, Parker’s comprehensive R&D program is designed to meet the most stringent requirements of the gas turbines of the future. A significant investment of millions of dollars is made to create testing methods, rigs, and apparatus that accurately mimic the constantly evolving challenges face by modern Advanced Gad Turbines.
Deploying tools such as CFD modelling to reveal the impact of pleat spacing, height and depth on differential pressures, dust handling capacity and other qualities of the filter media are just one part of Parker’s R&D effort. A world-class collection of laboratory testing capabilities and procedures allow simulation of the most punishing operating environments which go way beyond any current International Standards. Subjecting filters to extremes of temperature, vibration, moisture, and contaminants like salt allows any possible leak paths to be identified using advanced diagnostic tools like CT scans, transparent frame materials to enable visualization and dye testing. Any possible leak paths that are identified can then be eliminated at the design stage. Using the most advanced diagnostic techniques and backed with more than half a century of experience allows Parker to identify areas of improvement and engineer solutions.
In considering the filtration system, Parker Hannifin recommends that operators look for units that include robust frames, the use of construction materials that do not crack or become brittle over time, and resilient filter media that is not prone to sudden blockages and pressure spikes. Where moisture, salt, or other liquid contaminants are likely to impinge, selecting filters with durable hydrophobic and oleophobic properties is also advised. Construction practices and materials that are designed to maintain peak performance for longer.
With consistent performance through all filtration stages, clearcurrent® ASSURE delivers on all these requirements and the industry is evidently recognizing that. Despite being recently launched there are already over 35 reference projects in place, safeguarding around 15GW of power or 12 million households. Ultimately, high-performance advanced gas turbines demand high-performance advanced filtration in order to minimize life cycle costs, the carbon footprint, and operational risks.