The filter medium is the core element of every filter unit. The main task of the filter medium is to retain the impurities, which have to be deposited. At the same time, the filter medium needs to be able to withstand the chemical, thermal and mechanical stresses which occur. For an energy-efficient filtration process, the filter medium should have a high permeability and a large dirt-holding capacity, which is associated with a long service life. For filtration processes with a large dirt load, the filter medium should be easily cleaned (e.g., by pulsejet or back flushing). Many of these filtration properties mentioned are contrary to each other and cannot be combined in one filter medium at the same time. For example, a high separation efficiency due to a small pore size is always associated with a high flow resistance.
For demanding process conditions, (e.g., in the form of high-process pressures and temperatures or if sharp-edged particles have to be deposited), metallic filter media and, in particular, metal woven wire meshes are often used. Dutch Twilled Weaves, as one of the weaving types of woven wire meshes, are established filter media for the deposition of finest particles down to the single-digit micrometer range. To achieve these small pore cross sections, the weft wires need to be woven as closely together as possible. This results in a fabric with a low porosity, low free passage area and low number of pores, and therefore, a high-pressure loss and power consumption of the filtration process. Furthermore, the narrowest pore cross section is located inside the fabric, which is why this weaving type is very difficult to clean.
An alternative weaving type to produce finest wire meshes are the so-called Betamesh-PLUS fabrics. In these plain weave fabrics, the diameters of the warp- and weft-wires as well as the pitches are combined in such a way that these fabrics are characterized by a high permeability, a high dirt holding capacity and ideal back flushing properties. Thus, the Betamesh-PLUS fabrics combine a large number of the advantageous properties in one filter medium. So far, these fabrics could only be woven for pore sizes of approximately 10 μm and coarser. By adapting the weaving technology and the wires used, it has yet been possible to produce this advantageous weaving type for energy efficient filtration processes down to geometric pore sizes of 5 μm.
Introduction
Filter cloths are the core element for the separation of particle laden fluid streams with filter apparatus and are frequently used in process engineering plants in all industrial sectors. In order to reduce the energy consumption of the filtration process, on the one hand the process sequence, such as the type and frequency of backwashing, can be subjected to optimization, and, on the other hand, the filter medium itself can be optimized. This work will focus on the second possibility.
Using metallic filter media, almost the complete range of filtration tasks can be handled. Especially in filtration processes with high-quality requirements, metal woven wire cloths are selected as filter media. In industrial applications, metal wire meshes are used – for example, in the separation filtration or solids recovery, for clarification filtration, for the purification of fuels and hydraulic fluids, for water treatment and for the separation of dirt particles from polymer melts and solutions.
Due to their advantageous filtration properties compared to filter media of other materials such as plastics, textiles or ceramics, metal woven wire cloths have this broad application profile. The main advantages of the metal woven wire cloths are:
- With their regular and well-defined structure, metal wire meshes have a narrow pore size distribution[1] and guarantee an excellent separation and classifying accuracy. The pore size only depends on the type of weave, on the diameters of the used wires as well as on the pitches and can be determined before the cloth is manufactured[2]. Time- and cost-intensive weaving tests to calibrate the pore size are therefore not necessary.
- Due to their high chemical, thermal and mechanical resistance, metallic filter media can be used in demanding operating conditions, for example, given as high-process pressures and temperatures or sharp-edged particles, which have to be deposited.
- Depending on the type of weave, metal woven wire cloths can be easily backwashed[3] and thus ensure a long service life of the filter elements. This leads to cost savings compared to textile fabrics or ceramic elements.
The basis of the metal wire cloths are cold-drawn wires made of different metals or metal alloys. The used wire diameter varies between a few micrometers and several millimeters. Usually, metal wires with a circular cross-section are applied, although stranded wires or ropes are also used for special applications. Parallel to the weaving direction pretensioned warp wires form the carrier material, into which the weft wires are successively drawn in. Depending on the combination of the warp wires and the weft wires during the weaving process, the production of different types of weave with different aperture sizes and different filtration behaviors is possible.
Types of Weave of Woven Wire Meshes
A over a wide range of pore sizes used weaving type is the Square Mesh. In a Square Mesh (see Figure 1, left), the warp and weft wires have an identical diameter and are interwoven at the same distance from each other, the so-called mesh width w. A low flow resistance and thus a low-pressure loss during filtration can be achieved. The backwash properties of these fabrics are excellent. In addition to the plain weave shown in Figure 1, Square Meshes are also produced in twill weave. Mesh sizes of down to approx. 20 μm can be realized. To produce Square Meshes with such small pore sizes, very thin wires have to be used. They are very expensive and mechanically less stable.
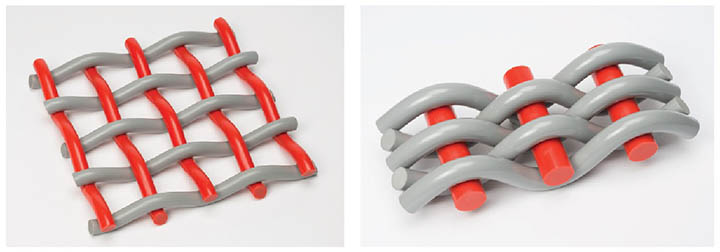
In so-called “opaque fabrics” either the warp or the weft wires are woven in such a way that they touch each other, and no mesh is visible in the projection. One of the most common opaque fabrics is the Single Plain Weave (see Figure 1, right), in which the weft wires are woven together as closely as possible during the weaving process. This results in a high degree of filtration accuracy. Both the diameter of the warp wires and the distance between two center lines of the warp wires, which is called the pitch t, are larger compared to the weft wires. As a result, the mesh count of the weft wires is higher than the mesh count of the warp wires. The mesh count indicates the number of wires per inch. The disadvantage of this type of plain weave is that the narrowest pore passage is within the mesh in the triangular shaped cross section between the warp wire and two weft wires, making it more difficult to back-clean the filter media. With this type of weave, pore sizes down to approx. 45 μm are realizable.
If smaller pore sizes are required in a filtration process, so-called Dutch Twilled Weaves (DTWs) need to be used. In this weaving type, the weft wires are positioned as close together as possible and one weft wire overstretches two warp wires (see Figure 2, left). By shifting the weft wire one diameter to the side, a typical diagonal pattern is created. Dutch Twilled Weaves are an established weaving type in filtration applications. Pore sizes down to 5 μm can be realized. However, due to the pore geometry, they tend to clog, which results in a sharp drop in flow rates. This leads to a low dirt holding capacity and poor backwashing properties (see also next section).
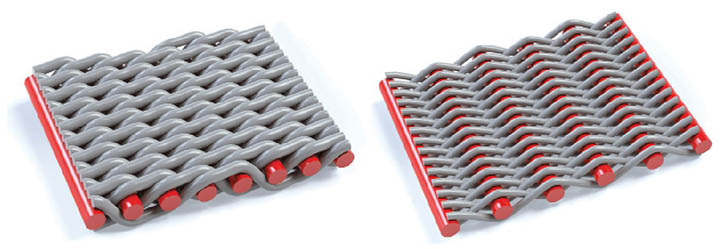
Betamesh-PLUS fabrics are a further development of Single Plain Weaves. The weft wires are extremely thin compared to the warp wires. During the weaving process they are shifted into each other to such an extent that partial deformations occur at their contact points. Due to the chosen wire diameters and pitches, the flow resistance and thus the pressure loss of this wire cloth is reduced compared to Single Plain Weaves and Dutch Twilled Weaves. So far, it was only possible to produce Betamesh-PLUS fabrics with a pore size of approx. 10 μm and coarser. By adapting the weaving technology, the fabric structure parameters and the mechanical properties of the wires, it has been possible to halve the pore size again. It is now possible to produce Betamesh-PLUS fabrics with geometric pore sizes down to 5 μm. These newly developed fabrics will be characterized in more detail below.
Filtration Performance of Betamesh-PLUS Fabrics
The Betamesh-PLUS fabrics are characterized with regard to their permeability, dirt holding capacity and cleaning behavior. The focus is on geometric pore sizes smaller than 15 μm. The Betamesh-PLUS fabrics are compared with Dutch Twilled Weaves. So far, this weaving type had to be used to achieve such small pore sizes. The production of the fabrics in a plain weave – as it is now possible in the Betamesh-PLUS fabrics – has not been possible yet.
The pore size of the wire cloth is characterized based on the geometric pore size. The geometric pore size is the diameter of the ideal spherical particle, which the brand new wire cloth can just pass through, filtering a liquid. The diameter is determined by a detailed geometrical description of the pore geometry. For details, please refer to the literature, e.g.[2].
Permeability
Figure 3 shows the flow curves for atmospheric air of Betamesh-PLUS fabrics and Dutch Twilled Weaves of identical geometric pore size. The curves of identical color have to be compared with each other. The significantly greater permeability of the Betamesh-PLUS fabrics becomes clear. The reason for this is the greater porosity, the larger open area and the larger number of pores of these newly developed fabrics in comparison with the Dutch Twilled Weaves.
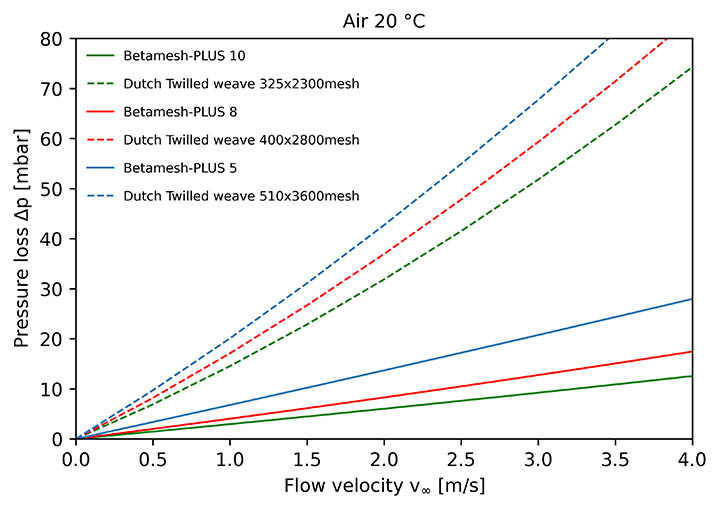
The increased permeability results in a reduced pressure loss. The possible higher flow rates lead to a higher amount of filtrate and therefore the productivity of the filtration process increases. The reduced use of resources and reduced operating costs are directly linked to the reduced power consumption of the process due to the reduced pressure loss. Is in the filtration process an identical pressure loss and power consumption compared to a filtration process with a Dutch Twilled Weave as filter medium allowed, using a Betamesh-PLUS fabric the required filter area is significantly smaller. This saves installation space as well as reduces the weight of the filter element.
The Betamesh-PLUS fabrics are characterized by a low flow resistance combined with small pore sizes, as shown in Figure 4. The filtration processes in which these fabrics are used are energetically more favorable. The Euler-number with 𝐸𝑢 with 𝐸𝑢=Δ𝑝𝜌𝑣2.
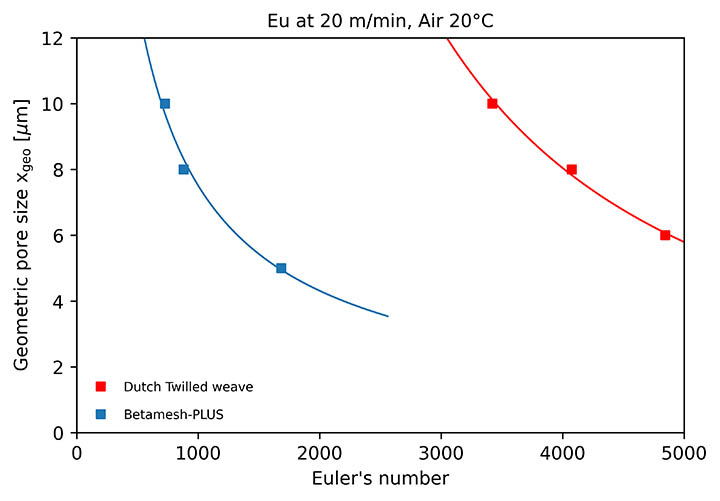
Dirt-Holding Capacity
The main task of a filter medium is to retain unwanted contaminations from the filtrate. The initial pressure loss is only present at the beginning of the filtration process. The contaminations retained by the filter medium continuously block the filter media pores, whereby the permeability continuously decreases with increasing filtration time or retained particles.
Figure 5 compares the change in pressure loss as function of the specific filter loading, i.e. the mass of separated particles, of Betamesh-PLUS fabrics and Dutch Twilled Weaves when separating the standardized test dust Arizona Test Dust Coarse according to ISO 12103-1 from atmospheric air. Again, curves of identical coloration have to be compared (fabrics with identical geometric pore size). When using a Betamesh-PLUS fabric, a significantly larger amount of dirt can be removed until the identical pressure loss is achieved compared to using a Dutch Twilled Weave. The Betamesh-PLUS fabrics are characterized by a greater dirt-holding capacity and thus service life.
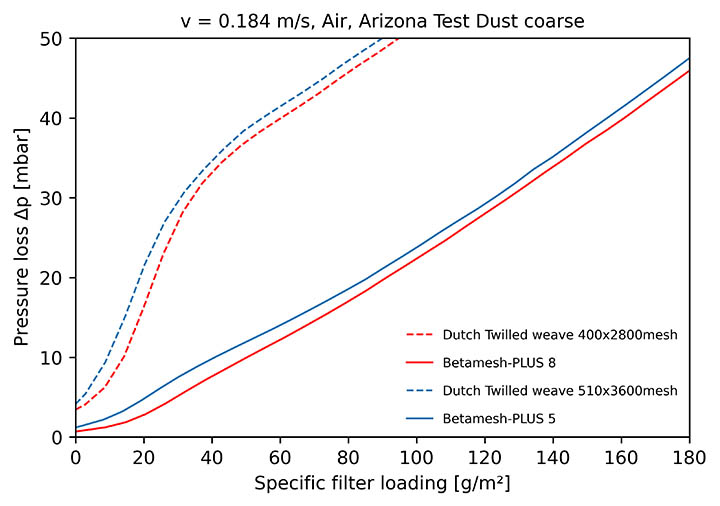
Dutch Twilled Weaves have a small number of pore openings and their narrowest pore cross section is located inside the fabric in the triangular pore passage between the warp wire and two adjacent weft wires. Therefore, a single particle can block this pore. As a result, the pressure loss and thus also the power consumption of the filtration process increase sharply immediately at the start of the loading. The pressure loss increases massively until the filtration process transitions to cake filtration. In this filtration state, there is a linear relationship between pressure loss or pressure loss increase and filter loading.
In Betamesh-PLUS fabrics, the wire diameters and pitches are combined to each other in such a way that the narrowest pore is located on the outside of the fabric between two weft wires. This slot-shaped pore geometry can’t be blocked by a single particle. If a particle is deposited, the flow still has sufficient free area to pass through. Supplemented by the large number of pore openings, this results in an only moderate increase of the pressure loss during loading. This larger dirt-holding capacity means, that the filtration process runs for a longer operation time, before the filter medium needs to be cleaned or exchanged. This lower number of filter elements which have to be exchanged saves costs. The higher dirt-holding capacity is linked directly to reduced downtimes and consequently increases the productivity of the filtration process.
When the filtration process finally turns into cake filtration, the filter cloth only has the task to mechanically support the filter cake. Using a Betamesh-PLUS fabric, the cake filtration process runs at a significantly lower pressure loss level and thus power consumption level compared to the use of Dutch Twilled Weaves.
The filtration process is more energy-efficient. All these benefits are present at the same geometric pore size and consequently separation performance compared to the Dutch Twilled Weaves.
Cleaning Behavior
The cleaning behavior by cleaning with a pulse-jet is investigated in accordance to DIN ISO 11057. Figure 6 shows the remaining pressure loss after a pulse-jet cleaning in the different states of the filter medium (cycle 1-30: new filter medium; cycle 31-60: artificially aged filter medium). The artificial and thus standardized aging over 2500 cleaning cycles is indicated by the vertical black dashed line. If fabrics of identical geometric pore size (identical coloration) are compared, the advantageous cleaning properties of the Betamesh-PLUS fabrics become clear. The remaining pressure loss due to blocked pores by separated particles is lower. These advantageous cleaning properties are caused by the position of the narrowest pores on the outside of the fabric. Particles can be easily removed from this cross section by a pulse-jet.
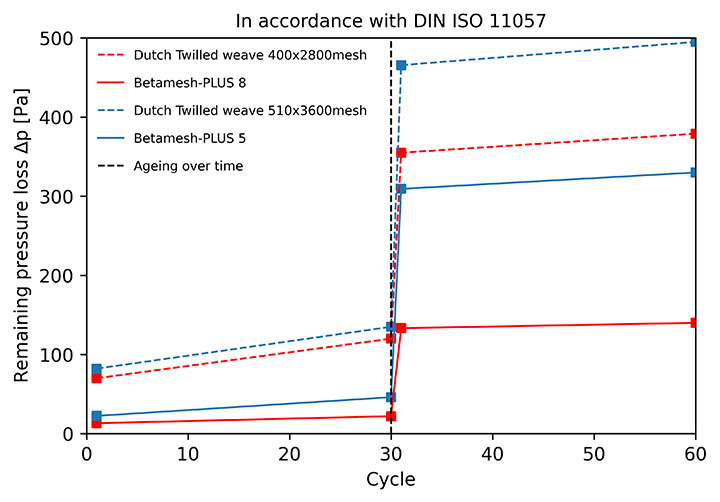
As already mentioned, in Dutch Twilled Weaves the smallest pore cross section is in the interior of the mesh. Particles separated in this cross section can’t be removed easily, the remaining pressure loss and thus the power-consumption after cleaning is higher compared to the Betamesh-PLUS fabrics. The slit-shaped pores on the outer side of the Betamesh-PLUS fabrics have also the benefit, that if the separated particles are the recyclable fraction of the filtration process, a higher amount of the fraction can be extracted using this newly developed type of weave.
Summary & Conclusions
If pore sizes smaller than approximately 10 μm were required in a filtration process, Dutch Twilled Weaves had to be used up to now. Due to their low permeability, either the filter area had to be very large or the filtration process was associated with a large pressure loss and thus power consumption. Due to the low dirt-holding capacity the filter media often had to be replaced or recleaned. However, recleaning was only possible to a limited extent.
Herein, Betamesh-PLUS fabrics were presented in detail and subjected to a filtration technology evaluation. Betamesh-PLUS fabrics are plain weave wire cloths with a high porosity and a large number of pores. Pore sizes down to 5 μm can be realized. For their automated production, the weaving technology had been further developed and the fabric structure parameters ideally adapted to the geometric conditions.
Due to the large porosity and number of pores, the fabrics are characterized by a high permeability and thus flow rate. Due to the advantageous slit-shaped narrowest pore opening on the outside of the fabric, there is no blocking of the fabric by deposited particles. This makes it possible to achieve a high dirt-holding capacity. The fact that the narrowest pore is on the outside of the fabric means that the fabrics can also be back-cleaned very easily by pulse-jet.
Overall, the newly developed Betamesh-PLUS fabrics make it possible to ensure maximum flow rates even with the smallest required pore sizes. As a result, the filtration processes are characterized by low power consumptions and thus energy consumptions. Energy-efficient filtration processes can be realized. Alternatively, the filter area and thus the installation space can be massively reduced with an unchanged flow rate compared to a Dutch Twilled Weave.
The advantages of Betamesh-PLUS fabrics explained here were only illustrated for the filtration of a gas flow. In case of the particle separation out of a liquid continuous phase, the described advantageous properties are also given.
References:
- Piesche, M.: Methoden zur Bewertung der Trenneigenschaften unterschiedlicher Filtermedien (Methods for the assessment of the separation properties of different filter media), final report of the AVIF-project A224, Institute of Mechanical Process Engineering, University of Stuttgart, 2006.
- Müller, M.: Untersuchungen zum Einsatz von metallischen Filtermedien bei der Filtration von Flüssigkeiten (Investigations on the use of metallic filter media in the filtration of liquids), Shaker, Aachen, 2017.
- Warth, T.: Experimentelle und numerische Untersuchung von Strömungswider-stand, Abscheide- und Abreinigungsverhalten metallischer Filtermedien (Experimental and numerical investigation of the flow resistance, separation and dedusting behaviour of metallic filter media), Shaker, Aachen, 2013.