A2Z Filtration Specialties is a designer and manufacturer of complete customer centric machines and automation solutions for filter production and assembly. A2Z’s customer base includes industry leaders in over 75 countries. The company excels in providing superior value, durable and globally serviceable production lines. The components are sourced from leading global suppliers to ensure ease of availability and trouble-free maintenance. A2Z equipment is easy to use, efficient and offers excellent value for money, with features such as pictorial manuals and remote access for service and upgradation.
With a dynamic team comprising of over 50 engineering professionals in design, manufacturing and installation, A2Z is providing complete turnkey solutions around the globe. The A2Z Design Team uses state-of-the-art Solid Works® 3D design software for the designing and simulation of filter production lines. A2Z’s deep knowledge of filter manufacturing processes and their ability to develop customer specific, innovative and efficient automation has resulted in development of fit-to-purpose solutions.
A2Z’S HVAC Assembly Cell
A2Z is pleased to offer yet another automation solution for the assembly of die cut frame HVAC filters. The HVAC filter assembly cell is designed for the assembly of die cut filters from 10 to 30 inches in length and width and 1 and 2 inches in pleat height. The filters are available in single and dual die cut models of filters.


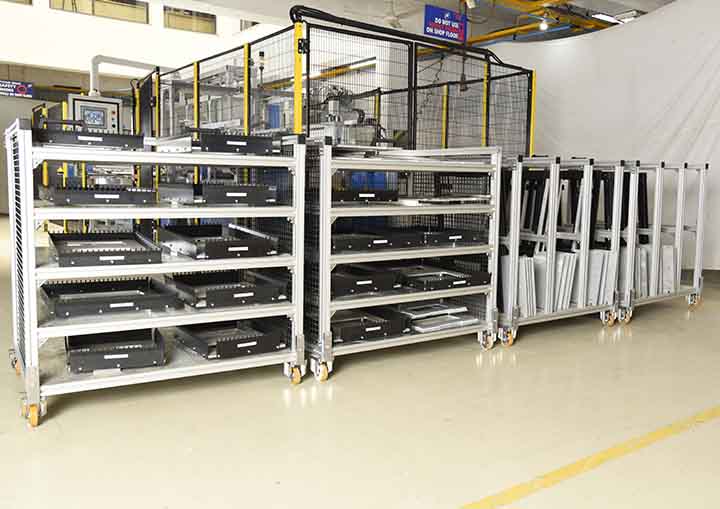
Process for Dual Die Cut Frame Filter
The bottom die cut stack is placed on a stacker and the automatic feeder feeds the die cuts to the glue applicator. Here, the glue applicator applies an even layer of glue along the surface of the die cut board. The forming station forms the bottom frame and indexes to the pleat pack placement station. An operator places the pleated pack into the formed bottom die cut frame. The pleat pack with the bottom die cut frame indexes to the top framing station. The top laminated die cut is flipped and placed over bottom frame. The process for the top die cut mirrors the process for the bottom die cut when the pleated pack is rotated. The complete assembled filter with top and bottom die cut is pushed to the curing tunnel where the curing of the glued die cut takes place.
A pick and place system picks the filter from the top of the curing tunnel and ejects the finished filter onto a chute for packing.
Features:
- Operator friendly
- Allows for quick change over of fixtures
- A production rate of upto 12 filters a minute
- Safety as per CE norms. Machine is guarded all around by steel mesh
- A laser safety scanner provided to stop the machine in case of interruption in operation, thus safe for the operator.
- User – Friendly 10” Allen Bradley HMI with a complete Instruction Manual
- Remote Support Facility
- Allen Bradley ® Controls
A2Z Filtration Provides:
- Fit To Purpose manufacturing, assembly & automation Solutions
- Value prices for quick return on investment.
- Ability to Integrate various automation solutions and processes including online quality validation systems
- Globally serviceable lines
- Latest state-of-the-art manufacturing & automation Solutions
- IoT & Industry 4.O compliant systems
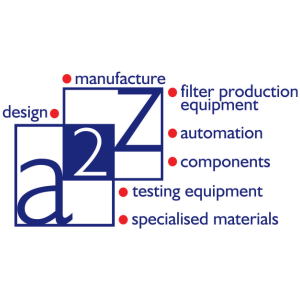
For further information, please visit our website – www.a2zfiltration.com or contact us at marketing@a2zfiltration.com
WhatsApp number: +91 9871690592