ITMA, the textile technology exhibition that takes place once every four years in Europe, was held from June 20-26 this year, attracting more than 105,000 visitors to Barcelona, Spain.
With 1,700-plus exhibitors from 45 countries, featured technologies supported a wide range of fiber-based products ranging from clothing and home furnishings to more technical products such as construction materials and reinforcements for composites. And, of course, both nonwoven and woven filter media.
A key theme at ITMA 2019, was Industry 4.0 – the name given to the concept of smart factories in which machines are augmented with web connectivity and connected to systems that can visualize the entire production chain and make decisions on their own.
This technology is being vigorously pursued by Germany’s VDMA textile technology branch. The organization hosted a press conference in Barcelona, with 12 companies outlining their developments in this field, and many of them touched on Industry 4.0.
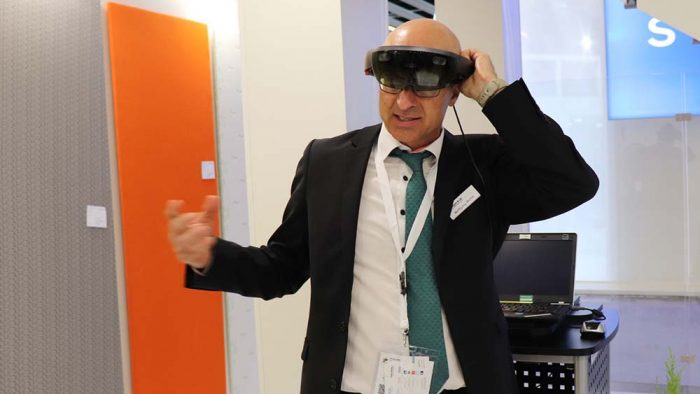
Needlepunching
In textile technology, as elsewhere, the trend is definitely towards automation and data exchange in manufacturing technologies, and AGV (automated guided vehicle) robots and virtual reality demonstrations were much more prevalent this year compared to the last show held in Milan in 2015.
One of the largest exhibits at the show, for example, was a complete diloline 4.0 range for nonwovens exhibited by DiloGroup.
This consisted of fiber opening and blending equipment, a carding unit, a crosslapper for compressing layers of nonwoven webs and the Hyperpunch Hα needlepunching unit.
“The diloline 4.0 has been equipped with a range of smart manufacturing functions developed in collaboration with Siemens, which further simplify operation and increase transparency in web forming and consolidation via the storage and rapid analysis of all machine data,” said the group’s CEO, Johann-Philipp Dilo.
Several development I4.0 modules were demonstrated to illustrate the potential of today’s automation for improved operation control and maintenance and ultimately, better quality products. The additional Siemens-based applications can be selected by app from Mindsphere in the cloud.
Just opposite DiloGroup at ITMA 2019, Andritz Nonwovens, like a number of other companies, employed augmented reality glasses to provide visitors with a full understanding of the technologies incorporated into one of its needlelooms.
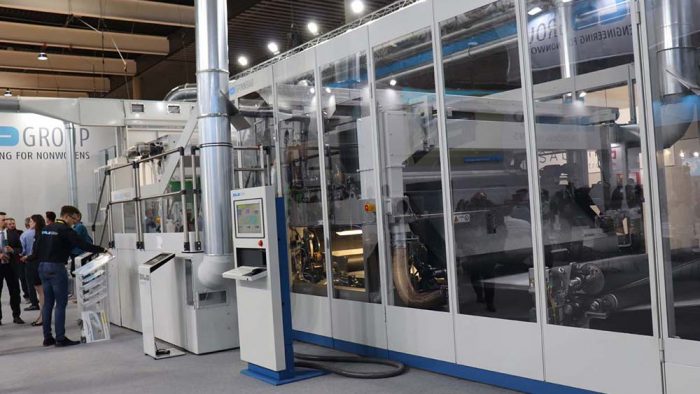
Fine tolerances
A significant development in carding technology for staple fibers was reported by Trützschler.
The setting of the carding gap on card openers has a critical influence on quality and performance, and Trützschler’s new TC 19i intelligent card can now automatically and continuously optimize it to within a tolerance of 3/1,000ths of an inch – something that has not before been possible through human operation of a machine.
“This allows us to measurably improve our customers’ raw material utilization and productivity while achieving consistently high quality,” said Dr, Dirk Burger, CEO of the Trützschler Group. “In addition, new cloud-based digital monitoring and management systems provide manufacturers with transparency over all processes in the manufacturing plant.”
The My Wires app, for example, provides information on the status of clothing and service intervals and helps with the planning of reorders.
Spunbonding
Another significant nonwovens technology for making filter media is extrusion-based spunbonding, often combined with a second technology, meltblowing, for finer materials, and a key player in this field is Oerlikon Neumag.
Oerlikon really pushed the Industry 4.0 boat out at ITMA 2019 by inviting visitors to be strapped into its combined flight simulator-cum-rollercoaster – again with the aim of demonstrating the inner workings of its technologies.

Coating and finishing
Filter media are frequently coated or finished in order to provide them with the specific functionality they require, most notably with PTFE, and a leader in finishing technology for such products is Monforts.
The company’s new “digital twin” capability is being made available for all of the company’s machine systems, particularly the industry-leading Montex stenter dryers.
By exploiting the latest advanced sensor technology, comprehensive technical machine data can now be virtually mapped in the cloud in real time easily accessed using the new Monforts Smart Support and Smart Check apps for an instantaneous status overview.
All specifications relating to machine performance and the production process can be mapped, to enable vastly simplified and targeted analysis for controlled planning and production. Insights harnessed from such analysis can be used to optimize the actual production process.
At the same time, potential sources of error can be anticipated and eliminated, enabling improved machine availability while considerably minimizing downtime.
In addition, the digital twin system provides information on the individual wear parts of a system, such as, for example, converters or gears.
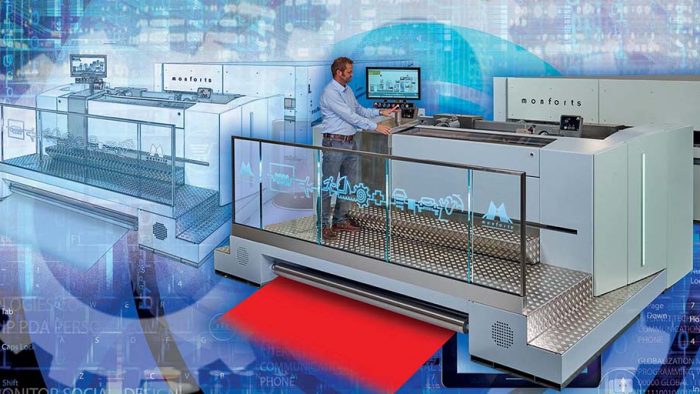
PTFE fabrics
The ability to thermally-set PTFE fabrics without oil greasing in the stenter chain and in the width, adjustment is particularly appreciated by manufacturers of filter media using Montex stenters.
“This protects both workers and the environment from harmful oil vapors and keeps the filter material clean,” said Jürgen Hanel, Monforts Head of Technical Textiles. “The guarantee of reaching 320 C with a very low temperature tolerance and with an excellent housing insulation is a major advantage, so that an outside temperature over 60 C is never reached at any point.”
Montex stenters in special executions are ideal for the preparation of filter materials for the drying and finishing of both wovens and nonwovens and characterized by high stretching devices in both length and width of up to 10,000 N, with the ability to accommodate the higher operating temperatures required.
Robotics
Finally, a conglomerate of companies consisting of Swedish automation specialist ACG Kinna, Italian filling systems expert Borsoi, and US carding supplier CCS (Card Clothing and Services) drew considerable crowds to their stand with demonstrations of a new robotic pillow filling system. This has the ability to fill and finish some 3,840 pillows per eight-hour shift – a considerable improvement on what is currently possible with either manual or semi-automatic systems, resulting in significant savings in both labor and energy for busy home textile businesses.
The technology is based on two robotic arms from Japan’s Fanuc – the world’s biggest robotics brand – which have been specially modified by ACG Kinna with advanced gripping tools and seaming and labelling devices. The pillows are automatically sealed with either single or double lockstitch seams and labels can be attached without interrupting the flow of the system.
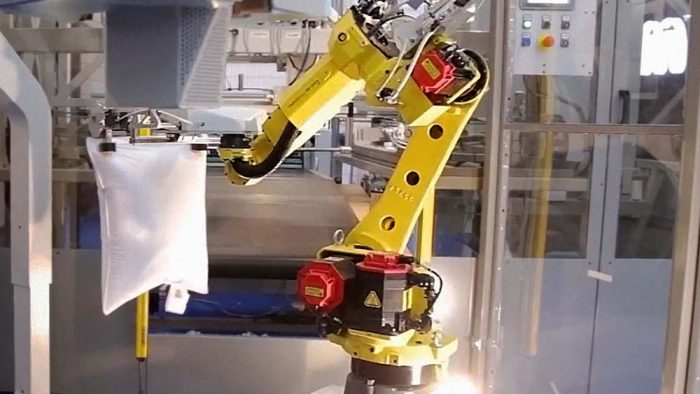
Smart Filter Line SFL-2000
But what, you may ask, is the significance of this to the filtration industry?
Well, at the forthcoming Filtech exhibition in Cologne, Germany from October 22-24t, ACG Kinna will be demonstrating its automation technology adapted – in a cooperation with Juki, the world’s leading manufacturer of sewing technology, and filtration specialist Job Group – for the entirely automated production of fully completed filter bags.
The new Smart Filter Line SFL-2000 Series consists of five sections for fully automatic filter bag production. The first section houses the media rolls and a unique solution for joining two rolls of media together without slowing down the production. This then leads into a compensator which feeds enough material to ensure the machine does not slow down further down the line. A steel brush is used to prepare certain special materials for welding during the feeding process.
The next section joins together the tube, either by sewing, welding or a combination of both. The joining process can be based on individual requirements and the media being used. The final section allows printing directly on the filter bag and cutting to the required length. One of the key advantages of the SFL-2000 is the flexibility it provides in the production process. Not only can the type of media be changed easily but also the method of joining the seams.
Automation and Industry 4.0, it appears, is now everywhere.