Beverlin Specialty Tube takes an in-depth look at the manufacturing process, benefits, and limitations of spiral weld tubes.
In the world of specialty tubing, spiral weld tubes have gained significant attention due to their unique manufacturing process and intrinsic advantages. Beverlin Specialty Tube has witnessed a surge in demand for spiral weld tubes across a range of industries, including oil and gas, nuclear, and large-scale industrial applications. In this article, Beverlin explores how the manufacturing process of spiral weld tubes creates several application-specific benefits – and a few noteworthy limitations – compared to traditional straight seam welds.
Manufacturing Process
Spiral weld tubes are produced using a continuous welding process, which is similar to high volume straight seam tubes. This process involves coiling a strip of metal around a mandrel at an angle, forming a helical shape. As the strip is coiled, the edges are welded together, creating a spiral seamed tube.
Key Benefits
- Enhanced Roundness and Straightness
- One of the primary advantages of spiral weld tubes is their inherent roundness and straightness. The continuous welding process ensures a more uniform and consistent shape than straight seam tubes, reducing the likelihood of deformities or irregularities in the tube’s structure.
- 360-Degree Filtration Flow
- Spiral weld tubes offer excellent filtration capabilities. The spiral seam allows for a 360-degree filtration flow, ensuring even distribution and efficient filtering of fluids and gasses. This makes spiral weld tubes ideal for applications that require high levels of filtration performance.
- Larger Outer Diameters Without Specialized Equipment
- Spiral welding allows for the production of tubes with larger outer diameters and of varying lengths without the need for large-scale coil and coil-handling equipment. Instead of relying on large metal coils, manufacturers can use smaller strips of metal and create a die set to achieve the desired diameter. This flexibility in production allows for more cost-effective manufacturing.
- Additional Benefits:
- Increased crush-resistance
- Increased corrosion-resistance
- Strength and flexibility in high temperatures
- Stronger, more consistent welds
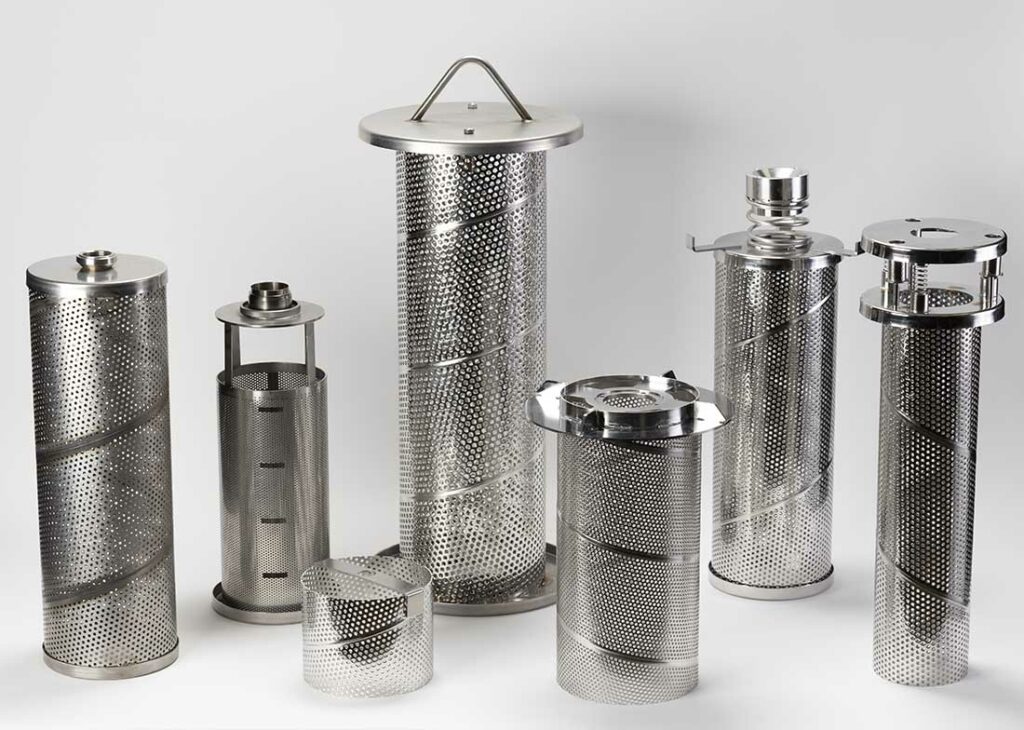
Limitations
- Reduced Open Percentage
- The spiral weld seam occupies a larger surface area, resulting in a marginally smaller open area for filtration or flow. This reduction is often negligible, however, and can be mitigated through proper design and engineering.
- Potential for Slower Production Speeds
- Depending on the specific application requirements, spiral weld tubes may, at times, run slower through the continuous welding process than straight seam tubes. This potential reduction in production speed should be considered when evaluating the suitability of spiral weld tubes for a particular project or manufacturing environment.
Experience Matters
At Beverlin Specialty Tube, we have extensive experience in the manufacturing of spiral weld tubes for a wide range of applications. Our expertise allows us to optimize the production process, ensuring the highest quality and performance of our products.
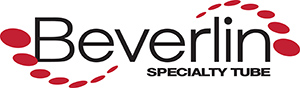
Visit with Beverlin at FILTECH, Nov. 12-14, 2024, in Hall 7, Booth No. G1.
If you have any questions or would like to discuss your specific needs, call us at (616) 949-5990, or visit www.beverlin.com.