Putting an ESG strategy in place is relatively straight forward. The hard work comes during the process of accurately tracking performance metrics and building the corporate structures necessary to empower and encourage change. Parker Hannifin’s John Davies, EHS & Quality Manager for the Filtration & Energy Solutions (FES) division – Altair Business Unit, outlines their approach to delivering on ESG.
ESG That Meets Goals
It’s a fairly safe bet that every single one of the world’s biggest companies – and many small and medium enterprises too – have an Environmental, Social, and Governance (ESG) strategy in place. However, for an ESG strategy to become more than an exercise in advanced green washing and bring about real corporate change requires much more than simply establishing the policy. A key process on the road to becoming responsible corporate citizens is setting challenging performance targets against rigorous benchmarking and demanding consistent improvement.
As part of an enhanced ESG strategy, air filtration experts at Parker Hannifin, for example, set out an ambitious target of achieving carbon-neutral operations by 2040 and cutting emissions from operations by half by 2030. The ESG program thus compares favorably to industry standards. In the UK, for
instance, the UK government has set a net zero target a full decade later, in 2050.
Crucially, as part of this overarching strategy, Parker Hannifin created performance metrics around each individual division. The Parker Hannifin FES division has already succeeded in slashing emissions by 28% in just the first five years under its enhanced ESG plan. Furthermore, while the company’s FES division has already realized significant reductions in emissions it also continues to meet or exceed a challenging target of a 3% year-on-year reduction in CO2e production set against a 2019 benchmark. This emissions reduction target of 3% was established in 2022. However, in only the first year of implementing its latest emissions reduction plan, the division achieved a 13% cut in net direct emissions.
Policy in Action
These reductions have been achieved through the implementation of dozens of individual carbon reduction projects at various locations globally. For example, installing an updated efficient roof at the Parker Hannifin manufacturing facility in Alton, UK, the division significantly reduced gas and energy consumption, improving the building’s energy efficiency by adding this secondary layer to the existing roof design.
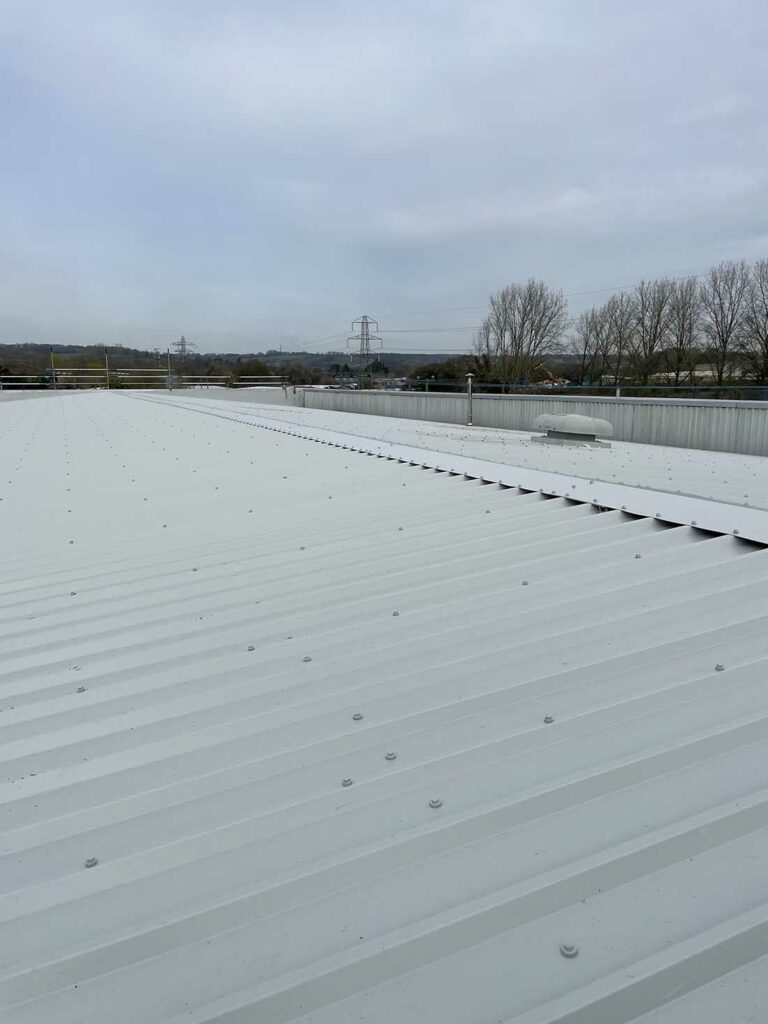
In addition, the ongoing 3% target has prompted continuous improvement initiatives. One example of this policy in action is the inclusion of regular ‘energy treasure hunts’ in which three-day events are undertaken at each location to identify energy efficiency opportunities across the company. For the FES division, energy efficiency improvements implemented so far include switching to LED lighting and using PIR detectors, finding and addressing compressed air system leaks, and lowering the set point on air compressors so that they work optimally. More fundamentally, improvements in the actual filter manufacturing process have also made a substantial contribution. Often these improvements are relatively simple to achieve. For example, by tightly controlling temperatures for glue points and using automatic timers rather than working 24 hours a day, as was the case previously, energy is saved.
Delivering Actionable Data
A commitment to gathering information that can be used to enact future measures is another critical part of achieving results from an ESG strategy. At Parker Hannifin energy monitoring and data loggers are deployed across the distribution system that allow the company to identify where further savings may be achieved and the FES division has initiated supply chain reporting too. The ESG program has been concentrating on Scope 1 and Scope 2 emissions so far, but the company is currently engaged in evaluating and reducing Scope 3 emissions as well.
Data is captured across all sections in Benchmark Gensuite, a comprehensive environmental health and safety (EHS), sustainability, and ESG reporting software solution that helps companies and investors analyze and report on investment-grade ESG data. Parker Hannifin uses this tool to track all waste streams which include general, recycled, hazardous waste and metal waste. In the UK, for example, nothing goes to landfill. General waste goes to energy recovery while other wastes and metals are recycled. The company also continues to not only prioritize minimizing waste sent to landfills but also conserving water across manufacturing sites.
Tracking waste and utility usage and converting that data into a CO2e figure gives actionable data that can inform goals and key performance indicators year-on-year. Having completed many on-site carbon reduction projects, including lighting retrofits, and HVAC system upgrades among others, the data reveals that while the emissions baseline in 2019 was around 946,000 kg’s of CO2e across the FES division, since the policy was introduced in mid-2022 and for the first full year that figure was already down to 823,000 kg’s CO2e.
Beyond the “E” of ESG
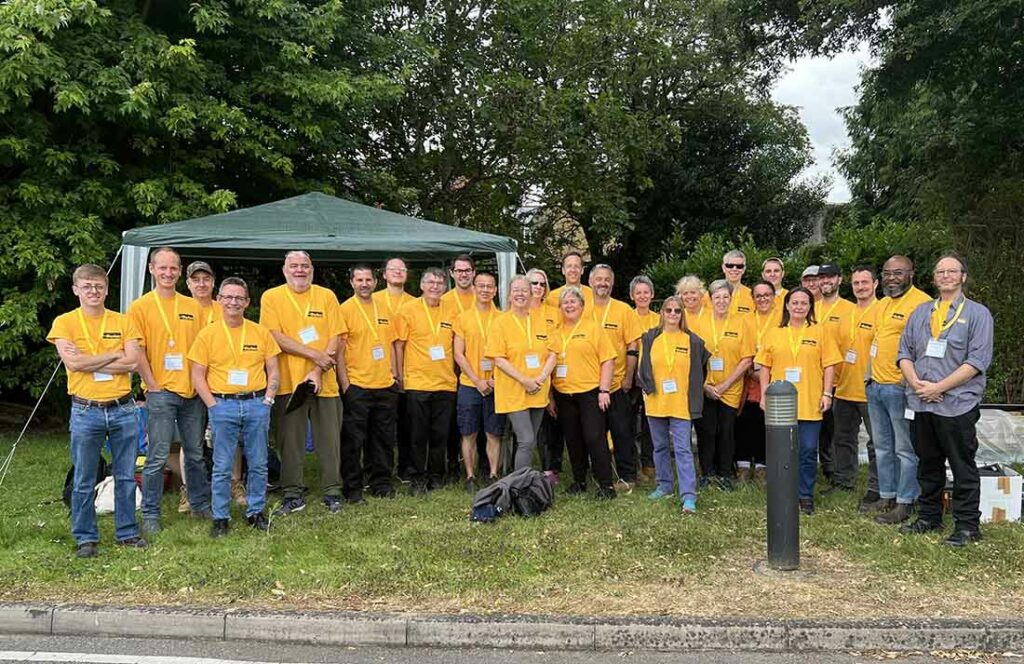
Parker Hannifin with more than 60,000 employees across the company, also prioritizes the health and safety and social aspects of its ESG commitments, which have resulted in a 45% reduction in the Recordable Incident Rate and a 33% reduction in the Lost Time Incident Rate over the last five years. This level of performance ranks Parker Hannifin in the top quarter of its peers. Employee well-being is also supported by having outside providers for mental health, and health surveillance programs. For example, mental health first aiders are on-site at the UK Alton site to support employees as needed.
In addition, in the 2023 financial year, the company focused on increasing diversity across the business, particularly in leadership positions and there is also compulsory code of conduct training for all Parker Hannifin employees annually. This reminds employees of the importance of diversity and inclusiveness, while training progress is tracked through the year. Beyond the immediate workforce, numerous outreach program are supported by employees. This ties in with wider Parker Hannifin Foundation initiatives which contributed more than $9 million to charities that helped strengthen communities around the world last financial year. The majority of these contributions supported causes that align with the Foundation’s three areas of focus – STEM education, community needs, and sustainability.
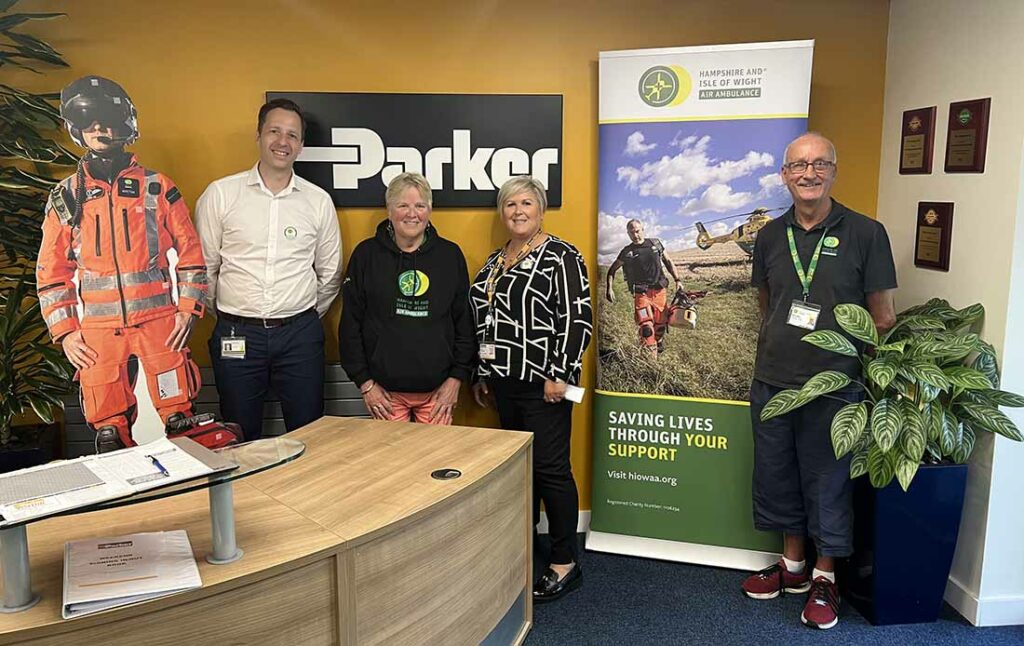
However, other, more local initiatives are also encouraged. An employee engagement team in each part of the business works to identify opportunities for employee well-being and community
service. In the UK-based FES division, this year’s local designated charity is the Hampshire and Isle of Wight Air Ambulance Service, for example, but other local projects are supported too. Currently, the FES division is engaged in providing refurbishment services for a specialized special needs children’s college and the Phyllis Tuckwell Hospice, which receives donated clothing and other items that are high on their needs list. UK employees also recently donated chocolate Easter Eggs to the local food bank. A key part of a successful strategy is to empower staff members to drive positive change and enabling local initiatives is an important element to gain traction and buy-in from employees.
Empowerment also comes from knowledge and training, and all Parker Hannifin FES division employees are given environmental awareness training delivered through an online platform. An internal group has also been formed with participants from all areas of the business. This group meets every other month to review ideas, explore current results and discuss future goals. While governance is specifically handled by corporate headquarters and individual division controllers, several audits and questionnaires are required on an annual basis.
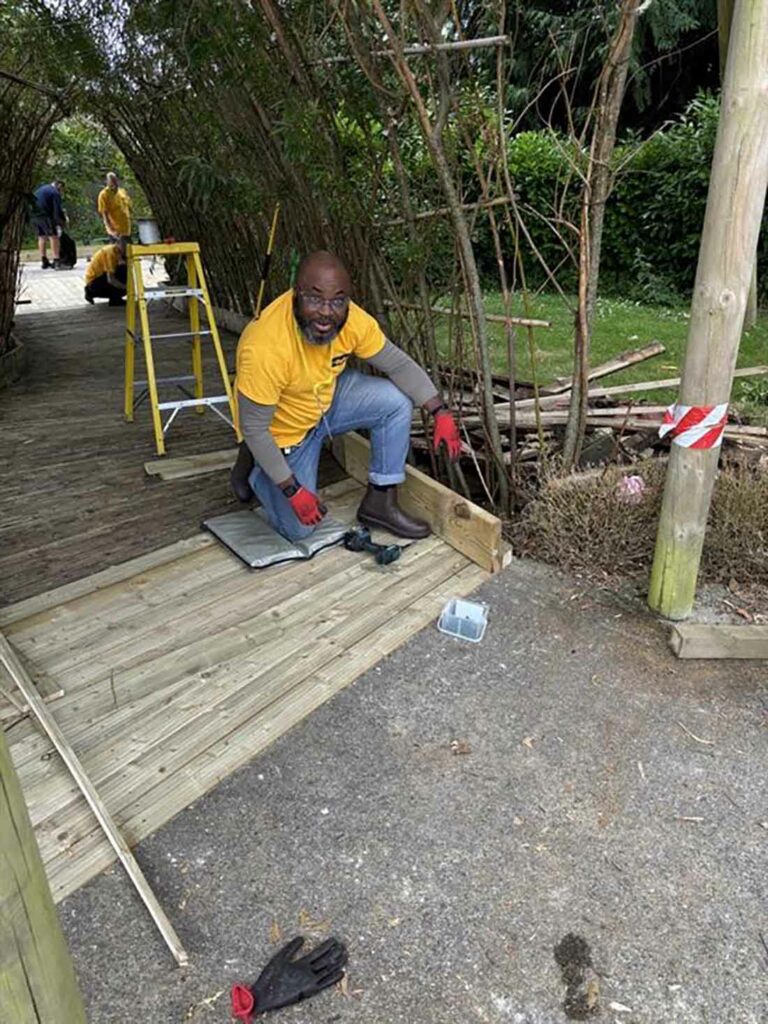
Beyond that, the Atlon site is ISO14001 certified. ISO 14001 is an internationally agreed standard that sets out the requirements for an environmental management system that can support organizations to improve their environmental performance through more efficient use of resources and waste reduction While this means an environmental management and stewardship scheme is in place, ISO 14001 includes the need for continual improvement of an organization’s systems and approach to environmental concerns. The standard was recently revised to ISO 14001: 2015 with key improvements such as the increased prominence of the environment in the strategic planning processes. Certification also ensures that the Alton site is externally audited to confirm improvements in the environmental aspects and impacts on the local environment. Indeed, many of Parker Hannifin’s FES division customers require that certification.
Beyond Parker Hannifin
The FES division’s commitment to sustainability and environmental stewardship is yielding results, but Parker Hannifin also has an obligation to the wider world. This goes beyond the conventional supply chain concerns though. By supporting improved energy efficiency in gas turbines, Parker Hannifin’s technology plays a very large role in protecting the environment far beyond the factory gate. A core element of this is a strong commitment to R&D to support continued performance improvements and in the last financial year, more than 40% of Parker Hannifin’s research and development was dedicated to expanding a clean technology portfolio, with a focus on electrification and the emergence of alternative fuels such as hydrogen and sustainable aviation fuels.
For the FES division, this R&D focus supports the development of filtration systems tailored for specific environmental conditions, such as damp coastal regions or dry and dusty deserts. These systems improve turbine performance and efficiency but also reduce differential pressure across the filtration system, increasing output and reducing operating heat rates. These are not one-time events but rather a continuous improvement in business processes both internal and external. It’s not without challenges including return on investment (ROI) calculations that are required to justify capital expenditure. Within Parker Hannifin’s FES division, all of the energy efficiency or CO2 reduction improvements identified through energy treasure hunts have been implemented.
Looking to the future, the strategic goals for any ESG programme must continually evolve to meet emerging environmental, social, and governance challenges but the obligation to support a more sustainable tomorrow must remain constant. The key to success though is to empower the company to make positive change through actionable data, leveraging best practices, demanding targets, and dedication to that goal.