Advancing next-level filtration, 3M is working with Svante Technologies to commercialize a filter media that can trap carbon dioxide (CO2) found in the atmosphere and permanently remove it.
Svante, headquartered in Vancouver, has developed a process for coating solid sorbents onto laminate sheets and stacking them into high-performance filters, which are available for both industrial point-source capture – from hydrogen, cement, steel, aluminum, pulp and paper plants and refineries – as well as for direct air capture.
Solid sorbents, particularly metal-organic frameworks (MOFs), are a step change for the carbon capture industry, Svante says. Their energy efficiency, resistance to degradation in the face of post-combustion flue gas impurities and low cost of ownership make them ideal for carbon capture.
Svante’s MOF captures CO2 from diluted flue gas streams with high capacity and selectivity over water. It captures 95% of the total CO2 emitted from industrial sources, adsorbing CO2 using direct low-pressure steam injection for regeneration. The company has partnered with BASF, the world’s largest chemical producer, to mitigate supply chain risk and scale-up the production of its MOF sorbent materials from lab to industrial scale, using a simple water-based process and green chemistry principles to minimize environmental impact.
The tailor-made solid sorbents have a high storage capacity for carbon dioxide – a sugar-cube sized quantity of the sorbent materials has the surface area of a football field.
Storage Capacity
The tailor-made solid sorbents have a high storage capacity for carbon dioxide – a sugar-cube sized quantity of the sorbent materials has the surface area of a football field. The engineered and structured adsorbent filters can capture and release CO2 in less than 60 seconds, compared to hours for other solid sorbent technologies.
The Svante MOF sorbent material is said to be proven and effective at separating CO2 from nitrogen contained in diluted flue gas from cement, lime, steel, aluminum, fertilizer, pulp and paper, oil and gas and hydrogen plants, and also has a unique resistance to SOx, NOx, oxygen impurities and moisture swing. It’s resistant to chemical degradation, which means less of a headache for operators and longer product lifetime.
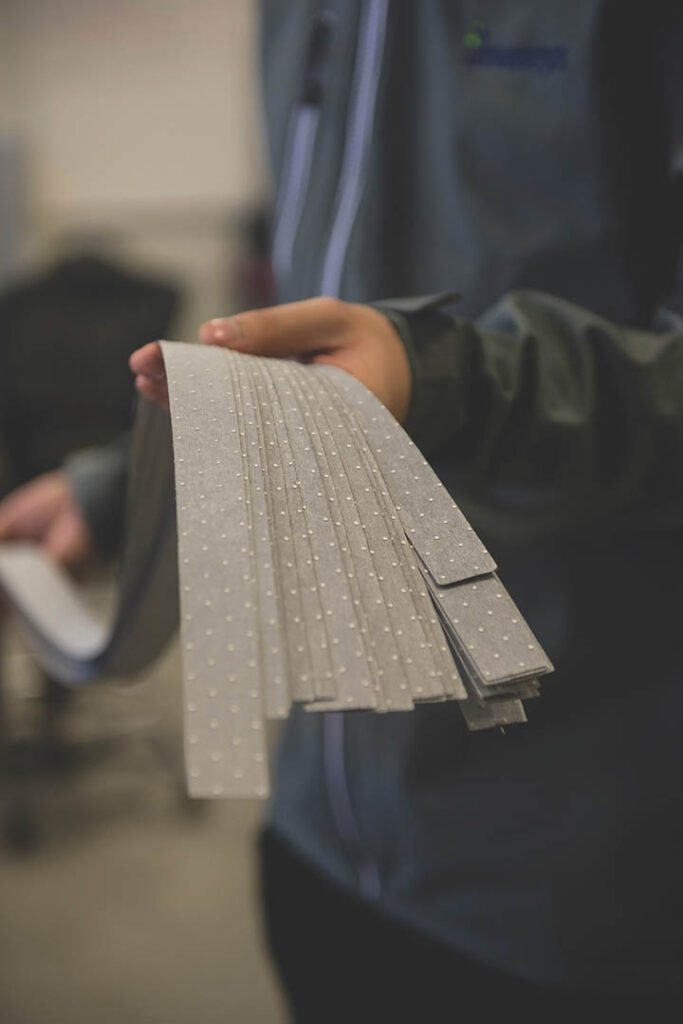
CO2MENT
In May this year, Svante announced Phase 3 of the ongoing CO₂MENT Project with Lafarge, Canada’s largest provider of building materials, and Denver, Colorado-based Dimensional Energy, a specialist in technologies for abating CO2 emissions across multiple industries.
Back in 2019, working with energy giant Total, Svante installed a demonstration unit at the Lafarge cement plant in Richmond, British Columbia, to capture approximately a ton of CO2 emissions each day.
The project has enabled Svante to de-risk its carbon capture technology in an industrial setting and for the past two years it has focused on increasing the efficiency of CO2 capture using its MOF filters.
Lafarge has meanwhile worked on finding a suitable end use for the captured CO2. Given the lack of CO2 transportation and sequestration infrastructure in southern British Columbia today, utilization of captured CO2 is fundamental to the decarbonization of large industries in the region.
Syngas
In Phase 3 of CO₂MENT, Dimensional Energy’s technology will convert the captured CO2 and green hydrogen to syngas, using its patented reactor and catalyst technology. The renewable syngas will then be further processed into liquid hydrocarbons which can be used in the production of industrial wax and other high value products that place the previously emitted carbon in an industrial use cycle.
Premium grade pure waxes produced from the process will be of interest to other offtake partners such as manufacturers of plastics, lubricants and cosmetics.
The project will include an ISO verified life cycle analysis (LCA) performed by a third party.
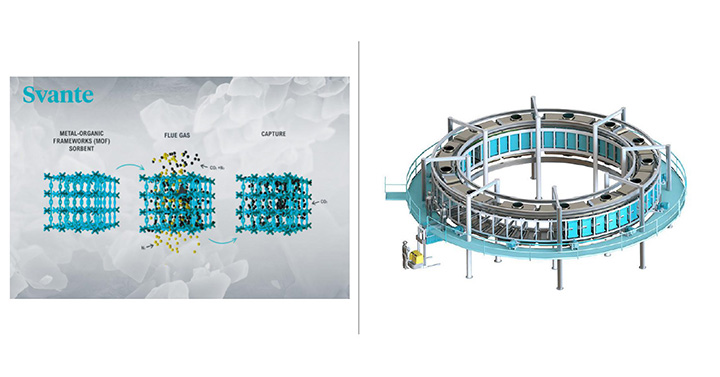
“Carbon capture is an important lever in our net-zero roadmap,” said Stephanie Voysey, head of sustainability and environment at Lafarge Western Canada. “However, for a carbon capture project to succeed, it must be paired with permanent geologic sequestration or utilization technology that will permanently isolate the CO2 in a specific media or product. If this pilot can be scaled to capture and use all facility emissions, it would be a first of its kind project for Lafarge and advance export and global adoption of this technology.”
“Finding pathways to the viable use of the CO2 we capture from industrial sites is key in developing a circular carbon economy,” said Svante president and CEO Claude Letourneau. “We must do everything we can to capture and remove CO2 before it reaches the atmosphere. This type of partnership and project could make a significant impact if deployed at scale.”
Jason Salfi, Dimensional Energy’s CEO, added that turning one of the world’s most persistent problems into an asset would contribute to a circular economy in better harmony with nature.
“Leveraging existing infrastructure in difficult to decarbonize sectors of our economy is where we, as technology providers, can have an immediate impact on abating carbon dioxide,” he said.
N95 success
3M is a leader in nonwoven filter media and Ray Eby, president of 3M’s Personal Safety Division, said that the company is eager to take on the challenge of scaling the production and supply of carbon removal materials over the next decade – in a similar way to how it managed to triple the production of nonwoven-based N95 respirators during the early days of the Covid-19 pandemic.
“Our deep expertise in filtration technology, extensive global R&D community and unwavering commitment to create world-changing solutions give us the confidence to scale these carbon-adsorbing solutions with the necessary speed to combat climate change,” he said. “3M is committed to helping build a low-carbon economy and driven by a need to solve the world’s most pressing challenges and our partnership with Svante to create innovative climate solutions is an exciting prospect for us.”
“3M is another great addition to our network of world-class strategic partners and investors,” said Svante’s Letourneau. “3M’s more than 120 years of expertise in producing materials science-based solutions at scale is unparalleled and will aid us in our efforts to capture millions of tons of CO2 from diverse sites around the world.”
Because of the wide array of markets the company serves, Letourneau added that Svante’s technology can be applied to 85% of the rapidly escalating carbon capture and removal industry.
Record Fundraising
3M Ventures, the venture capital arm of 3M, recently participated in Svante’s Series E fundraising round, which raised a record-breaking $318 million to accelerate the manufacturing of the carbon capture and removal technology.
“With 51 technology platforms across 3M, we’re innovating and creating new technology capabilities to meet the growing needs of the carbon capture and removal market,” said Fabrice Moguet, senior vice president of research and development for 3M’s Safety and Industrial business group. “To fulfil Svante’s needs and help combat climate change, we’ll need to scale to thousands of miles of technical material over the next few years, and we’re excited to manufacture our first products in the United States for Svante’s direct air capture applications.”
The joint development agreement between 3M and Svante will focus on solutions using parallel channel-structured adsorbent technology for sale into the carbon dioxide removal industry.