Optimizing the efficiency of nonwoven filter media is basically about achieving the perfect balance between the material’s capacity to capture and hold dust or other particles and its pressure drop – its resistance to the air, liquid or gas that is being passed through it.
There are of course, many parameters that can influence this and a huge amount of research and trials continue to be undertaken with the aim of optimizing this balance between particle capture and pressure drop.
At the Fraunhofer Institute for Industrial Mathematics (ITWM) based in Kaiserslautern, Germany, a range of digital twins has now been developed to move beyond what is already possible, as part of the development of a ready-to-use simulation software program called FiltEST (Filter Element Simulation Tool).
This work was outlined by Dr Ralf Kirsch, team leader of the ITWM’s Flow and Material Simulation Department, in a fascinating keynote speech at the Filtech conference and exhibition which took place in Cologne, Germany from November 12-14.
Flow simulation
“A digital twin is a computerized, virtual counterpart to a device or process in the real world, allowing us to study and predict its performance under varying operating conditions,” he explained. “In filtration, a classical application is the computer-aided optimization of the design of a filter media or element to reduce the time and costs associated with manufacturing and testing prototypes.”
The relevance of such a digital twin for the prediction of the filter’s lifetime, he added, is underlined by the abundance of research and trial work devoted to the simulation of flow and filtration from the microscopic length scale of the nonwoven to the macroscopic scale of the filter element.
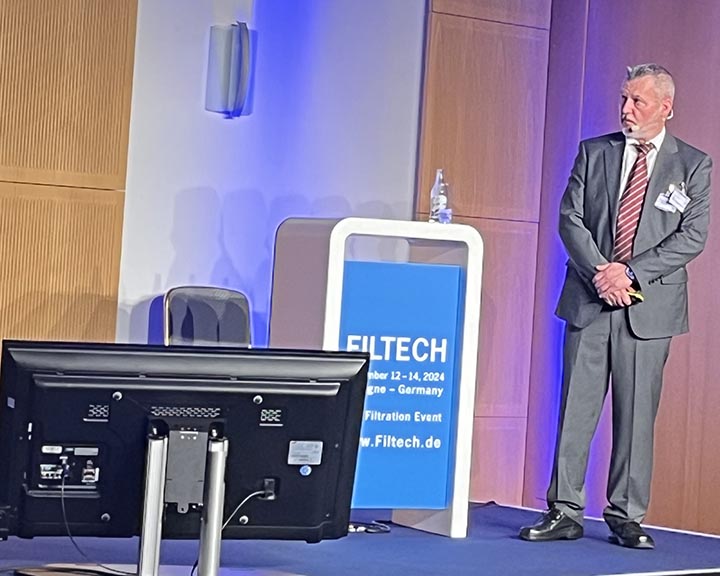
“Digital twins interacting with the real filter device through data exchange will play an important role going forward, because they offer very interesting possibilities such as predictive maintenance, the automation of optimized operation and much more,” Kirsch said. “Obviously, a digital twin must reflect the relevant properties of the real device and therefore, one of the challenges is to identify what is relevant so that computational resources do not prevent its beneficial use. In our work we have looked at improving digital twins of filter elements by taking a more integrated approach with a focus on the filter media. More precisely, we have considered a chain of digital twins, representing the different stages the filter media goes through – from the laydown process to the formation, including pleating, to the media’s operation within a filter element.”
Pleating
A material property of major interest is the uniformity of the distribution of the fiber volume fraction.
The fiber laydown process determines how ‘cloudy’ a nonwoven filter media will be, which influences its efficiency as a flat sheet material. Pleating, however, creates regions of compacted fibers, where the flow resistance and filtration properties can differ significantly from the flat sheet.
“In contrast to a quite common assumption of computer models, filter media are not rigid bodies, but they deform under the pressure of the fluid flow,” Kirsch stressed. “Depending on the operating conditions, these deformations cannot be neglected in the digital twin of the filter element.”
The deformation of a pleated filter media during operation leads to acknowledged and unwanted effects such as pleat collapse, or pleat crowding. Flat filter media, however, can also be affected by related impacts.
Trade-off
One of the major goals is to identify an optimal trade-off between low flow resistance, a large filtration area and sufficient mechanical robustness of the design.
In order to assist filter element designers with this, the interaction of the deformable nonwoven with the air or liquid flow – called Fluid-Porous Structure Interaction or FPSI – is being simulated using specialized mathematical models and numerical algorithms.
“The achievements of previous joint research projects have formed the basis of this approach, and a lot of ongoing and future developments will lead to further improvements of the simulation methods,” Kirsch said. “With FiltEST, users can create digital twins of multilayered filter media, filter pleats and entire filter elements to study their performance in terms of efficiency, lifetime and particle holding capacity. In addition, we offer services for the computer-aided optimization of pleated filters with regard to both pressure drop and service life.
“In more and more fields of application, the deformation of filter media during operation is significant. In addition, our simulations can take into account the impact of the compression of the nonwoven material during manufacturing, such as the pleating process, on filter performance and lifetime.”
Moving its digital twinning and FiltEST software development forward, ITWM already offers services for the integrated computer-aided optimization of filter elements and their components by analyzing variations in the geometry of filter pleats, panels, cartridges and housings, FPSI for advanced studies of the flow-induced deformation of the filtering media and a stress-strain analysis of the filter element’s housing, based on flow and pressure distribution.