Pleating is one of the most critical processes for the filtration industry. The advent of a wide range of media with specific applications and properties requires pleating equipment that can perform without affecting the properties and performance of the media.
Filters are pleated to provide enhanced performance characteristics for certain applications. Through pleating, filters can offer increased surface area and density without impacting airflow. Thus, pleats enable filters to collect more particles without increasing pressure drop or energy consumption.
Once the filter manufacturer identifies the type of pleats and properties to be maintained in the target media, the correct process can be determined. Common pleating processes include: blade pleating; rotary pleating; servo pleating; star pleating; and mini pleating
Blade-type pleating systems are generally a good fit for producing filter pleats of varying sizes and depths. This technology is capable of supporting multi-layer filter media and can create “M”-style pleats. Blade pleaters are frequently used for higher-efficiency pleated filters and are versatile enough to handle materials from delicate membranes to multi-layer woven and sintered materials.
Rotary-type pleating machines are suited for applications where the filter media and pleat height remain fairly consistent. These machines are known for production speed and precision. They are commonly used by automotive filter manufacturers, as well as industrial filter manufacturers working with cellulose media.
Servo-type pleaters offer the ability to pleat at varying heights and support materials of various thicknesses at high speeds. Common pleat types with this technology include marker pleat, the taper pleat, step pleat, and “W” pleat, with the ability to support various media combinations such as heavy-duty mesh, expanded metal, epoxy-coated mesh, stainless steel material, etc.
Star pleaters are commonly used in HVAC pleat production. These machines are a good fit for high-volume pleat production with expanded metal laminated HVAC media, as well as the self-supporting polyester HVAC media. These machines are capable of pleating multiple layers of media at once and typically have independent frames to enable easy removal when swapping out star wheel and frame assemblies for different production requirements.
Mini-pleat machines are commonly used to provide spacing between media pleats via a hot-melt adhesive to achieve the desired airflow in a filter. These units have grown in popularity as media and adhesive technologies have advanced and are now the go-to method for pleat separation in many filtration applications, such as HEPA and ULPA filters.
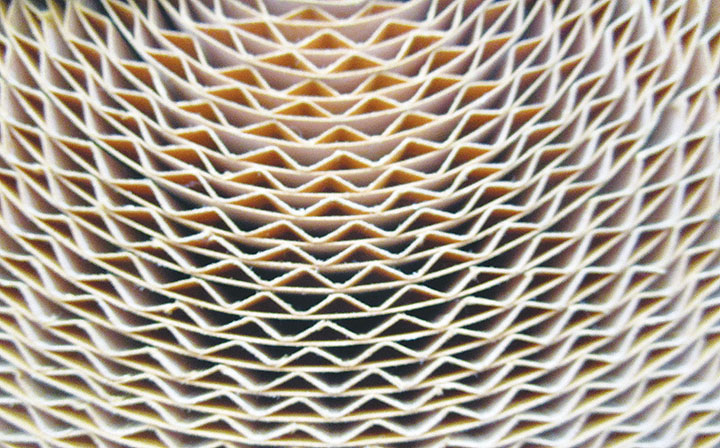
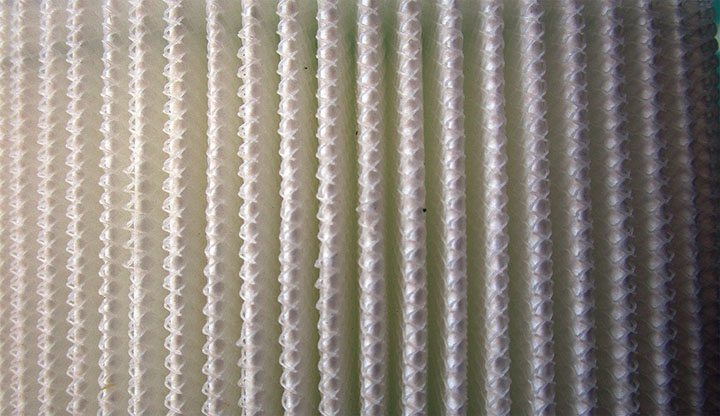
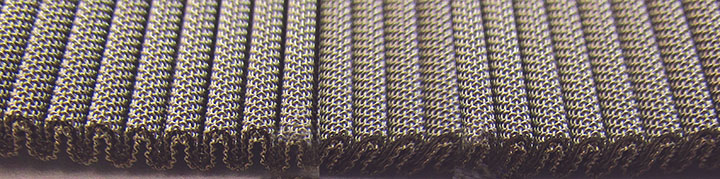
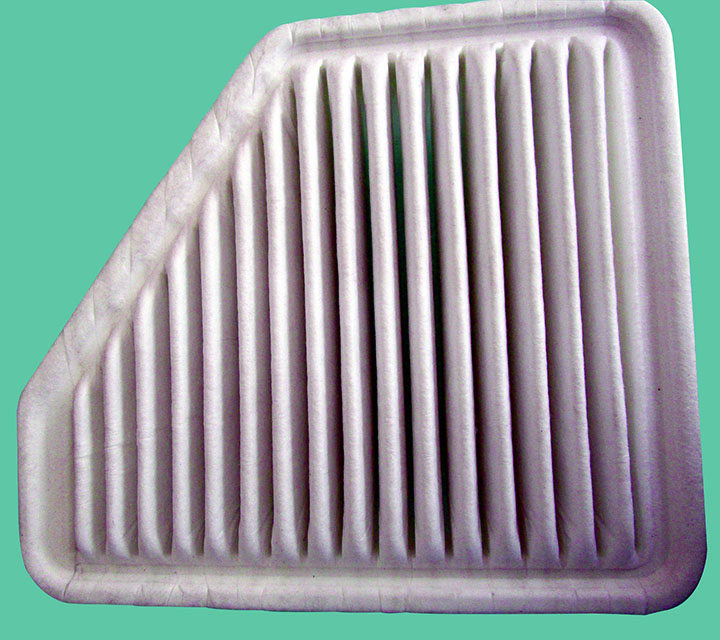
While the pleating systems mentioned here provide a general overview of the technology options, manufacturers and suppliers also offer custom and hybrid options to support the needs of different manufacturing scenarios.
For example, A2Z Filtration, a global provider of equipment for filter manufacturing, offers a wide range of technologies for filter pleating, including blade, rotary, servo, star and mini pleating systems, as well as custom and hybrid solutions. A2Z specializes in working closely with its customers to identify the correct process to meet pleating needs, leveraging its deep knowledge and experience in various forms of pleating to develop unique solutions to meet challenging application requirements.
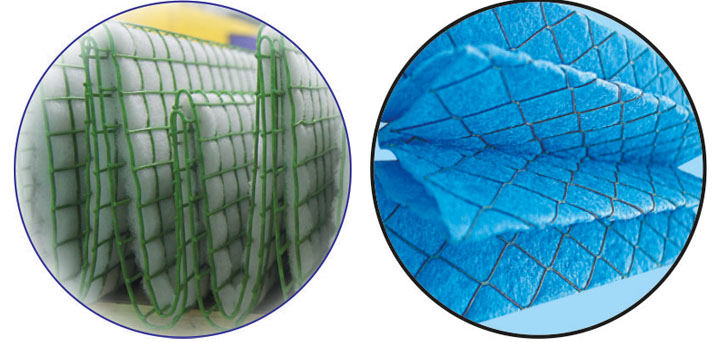
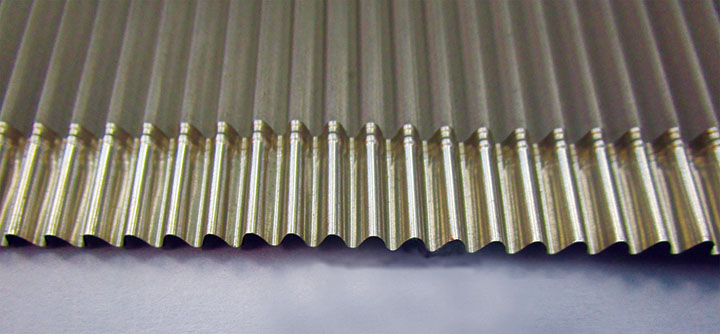
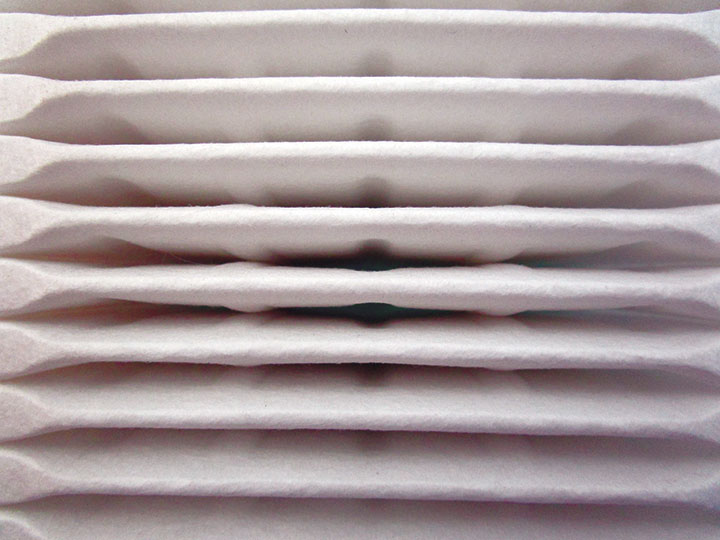
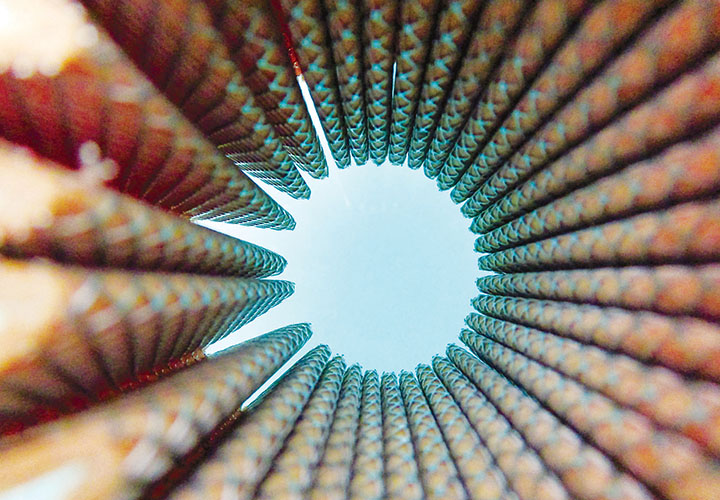
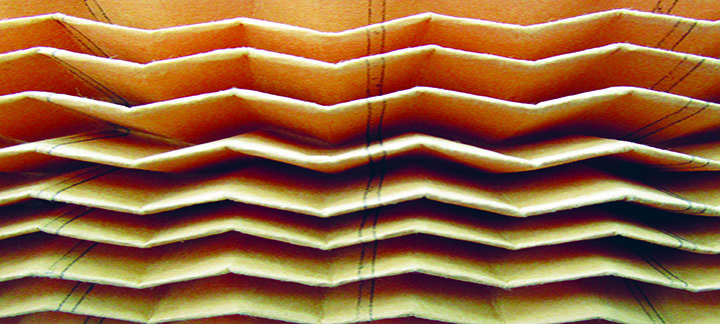
JCEM Group, which includes JCEM GmbH (Switzerland), TAG GmbH (Germany) and JCEM Inc. (USA), offers innovative, efficient, and robust pleating systems for a range of filtration applications. The company’s lineup includes its latest generation P7 model, offering what the company describes as “world-record” pleating speeds, as well as turnkey blade and mini pleat systems, cabin air lines, custom requirements, etc.
Pleating Systems & Equipment (PSE), of Simpsonville, Kentucky, is a supplier of high-quality equipment and contract pleating services. CroyBilt is PSE’s flagship brand of mini-pleating machines, rotary-pleating machines, and used pleating machinery. Roth Industries has also recently partnered with PSE to offer its high-speed CNC Roth blade pleaters, supporting 4-300mm pleat heights and glue bead application.
Solent Technology Inc. of Columbia, South Carolina, offers a range of pleaters capable of producing pleated filter packs from a variety of media types. The company’s SOLTECH pleating system can economically produce easy-to-handle panel or cartridge mini pleat filter elements. Also, through its Contract Pleating Services business unit, Solent is focused on helping small companies get started in the market from producing samples to shipping orders, providing production support or assisting with the setup of on-site production.
This edition of “Technofile” provides a general overview of filter pleating technology, as well as some resources for more information about technology options. However, it is not all-inclusive, and there are many pleating system suppliers and technologies available to help meet your application needs. Doing as much homework in advance of making a technology decision is always recommended.
For more information, visit:
a2zfiltration.com`
jcem.group
pseusa.com
solentech.com