The use of micron ratings as a primary parameter to select media for typical metalworking fluid filters could lead to misinterpretation and possibly selecting a fabric which has a high operating cost. This article offers a cursory explanation on the practice of micron rating to show that filtration systems for metalworking fluids closed loop applications “study” at this parameter in a manner different from other filter applications. In addition, it shows that the different “look” is an advantage in selecting media and minimizing operating costs.
Definitions
Micron Rating
Micron rating is a practice which assigns a quantitative value on a fabric to register its ability to intercept particles of a given size. There is much discussion on what the number means as far the actual size of the particles intercepted, and the rating is usually qualified with a suffix such as “Absolute,” “Nominal,” and “Maximum.”
These terms are complex and subject to individual interpretation. However, the industry has evolved to use them to generally rank the “degree of tightness” of one fabric over another. For example; a 5-micron barrier is tighter than a 10-micron barrier since the 5-micron material would trap a smaller particle.
Sector of Filtration Applications
Operations – The arena in which this article deals is metalworking fluids, where operations include machining, grinding, honing, rolling, drawing and support functions such as quenching and parts washing.
Coolants – The fluids are oils, water and a full range of water base blends.
Filters – There are many types and styles of filters used in this industry but, discussion is on flat bed filters which use roll media. These encompass gravity, air vacuum, liquid vacuum and some pressure devices. Their design will play an important part in the media selection process. Many times options are dictated by the mechanical function of the filter as well as its ability to intercept the contaminants. Most have increment indexing so the media moves in the bed slowly allowing the cake to accumulate and be maintained.
Media – The roll-media for these applications constitutes all types of fabrics and various manufacturing techniques. The most widely used weights are from .5 to 6 ounces per square yard. This includes single layers, multilayers, blends and high-loft fabrics.
Who Mainly Uses Micron Ratings
The rating function is used mainly by cartridge, bag and other filter manufacturers where it is necessary to rely on the initial tightness of the bare fabric to perform the needed particle interception. Hydraulic and lube oil cartridge filters are good examples. They are on systems to keep “clean” fluid clean. The contaminants they encounter are from either outside foreign sources or minor wear and tear of the system’s components. There is not much contamination but the filter element must be able to intercept the particles as they occur.
Applicability on Metalworking Fluids Filters Applications
Metalworking fluids applications use filters to clean “dirty” fluid. Contamination is a constant input and micron ratings on rolled media are not as significant for evaluating performance. The main reason is that the media is not the primary barrier to intercept the particles. The media is the septum upon which a cake of particles is held and the cake performs the needed filtration function. This works well, since the continuous input of contaminants creates the “body” of cake for better cleaning. The cake offers more depth and can intercept particles smaller than the openings in the media. Hydraulic and lube applications do not have the continuous input of solids like metalworking operations and rely on the initial media tightness to clean the fluid.
Cake Definition
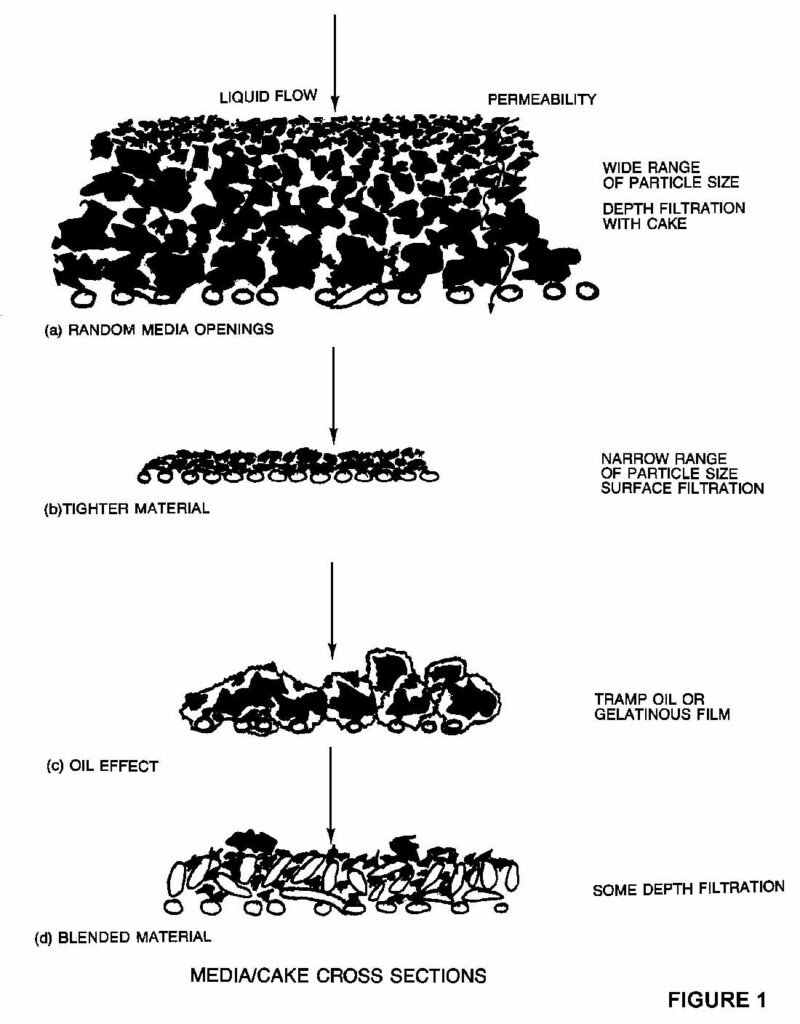
The term “cake” is the industry’s jargon which is referring to the accumulation of contaminants coating the media or imbedded within its fabric to make it a tighter barrier. The cake on the filter media does not have to be a thick layer which can be cut with a knife. It can be a film or even appear as a stain on the fabric.
Figure 1 shows a cross-section of the four types of cakes that are generally experienced with these types of filters. The first illustration (a) “Random Media Openings,” is an application where a thick cake has a wide range of particle sizes. The media openings are random in size and relatively large. The fabric is selected to intercept the larger particles first. The large particles then trap increasingly finer material. This occurs in the depth of the cake as well as on its surface.
The second drawing (b) “Tighter Material,” depicts a situation where the particle size range is relatively narrow. In this case, the filter will be fitted with a tighter media. The rate of flow through the filter is selected to still rely on the cake filtration. This illustration can be applicable to stained media where the stain is not thick enough to offer depth filtration but is still effective in trapping finer material.
The third picture (c) “Oil Effect,” reveals what happens when a foreign tramp oil enters the filter which is serving a water base fluid. The oil coats the particles and acts as a sealing agent which prevents the cake from becoming thicker. The film is still of some use, but it is a “slimy” gelatinous accumulation.
The fourth sketch (d) “Blended Material,” exhibits a different type of media structure. Metalworking applications have more options since the blended media offers a thicker barrier for depth filtration. This is an advantage where there is a relatively narrow range of particle sizes or where it is desirable to intercept larger particles in the body of the media to give it a longer life.
Therefore, for most of the flat bed filters with increment indexing, media selection is based on providing the openness to intercept the largest particles first and let each subsequent layer continuously intercept finer material until an adequate and permeable cake is achieved and maintained. As a result, fabrics with much larger micron ratings are used when compared to hydraulic applications. With all set-up conditions correct, a relatively open media can achieve significant clarity levels with a relatively low usage and lower operating costs.
There are some cases with flatbed pressure filters where the selected media would be tighter since the filter replaces the entire bed when it indexes. It starts with fresh bare media each time. Even with this, the first phase of flow begins to form a cake.
Takeaways
The facts presented here can lead to the following “takeaways:”
- Micron ratings are not as effective in selecting fabrics for metalworking operations since media is more of a septum to build a cake for filtering, instead of being the only barrier to intercept particulate.
- Air permeability, particle retention and cake generation capability are better parameters to use.
- First cost of a roll should not be a
major factor in the decision making process. Operating costs of the media, fluid life and machine performance are more significant factors in the economical
evaluation.