The Essential Role of Nonwovens in Filtration Underlined at FILTECH
The latest developments in engineered nonwoven media for air, liquid and gas filtration were showcased at the recent FILTECH exhibition which took place in Cologne, Germany, from November 12-14, 2024.
It was particularly notable at the show that the integration of nanofiber particles and webs into nonwovens is gaining increasing importance and in addition, filter media pleating – a process unique to the industry – is becoming ever more widely adopted as technology suppliers increase performance speeds. The accommodation of sustainable raw materials as an alternative to synthetics into systems was another key theme.
Cleaner Electrospun Media
As the leading provider of nanofiber technology with its NanoSpider system, Czech Republic-headquartered Elmarco reported that it has now extensively trialed and tested the use of many renewable feedstocks and environmentally friendly solvents in the production of electrospun nanofibers.
The company advises, however, that there are specific challenges associated with scaling up, mainly to do with the volumes of solvents required for processing, which in turn further emphasizes the need for process optimization. This comes from gaps in the fundamental understanding of how the electrospinning process works for fibers on the nanoscale, making it difficult to predict the types of interactions between a polymer and solvent pairing.
Elmarco can provide support and guidance to help reduce the costly burden of research and development for creating or adapting a new electrospinning process for new polymers or solvents.
Sustainable Polymers
The sustainable polymers Elmarco already has experience with include PETG, a cost-effective polyester derivative as an eco-friendly alternative to PET which eliminates the need for processing with fluorinated solvents. PETG’s versatility allows it to be functionalized, making it ideal for specific applications, and it can be spun into thinner structures than traditional PET. Polylactic acid (PLA) and polycaprolactone (PL) are other biobased polymers, with PLA being particularly biocompatible for numerous biomedical applications, while TPU and polyamides boast excellent strength and chemical resistance, making them well-suited for certain applications, particularly in the realm of wound compatibility. Their electrospinning enables the creation of very small fiber dimensions and they exhibit high solubility.
Cellulose can also be electrospun into ultrafine fibers as small as 300nm, possessing low thermal expansion while remaining lightweight yet strong, while chitosan is a bio-based polymer with excellent water uptake properties and is used to form hydrogels. Bioactive compounds can also be incorporated for use in medical compounds and wound treatment.
Solvents
Green solvents offer the potential to replace toxic substances or those derived from petrochemicals in electrospinning, yet there are still certain barriers to their widespread adoption, Elmarco advises.
Challenges in their sensitivity to environmental conditions leads to complexities in their utilization and there is a need for further process optimization. Nevertheless, green solvents have been used to produce nanofibers with desirable traits such as air permeability, repellency and enhanced filtration capabilities and some can be seamlessly integrated into advanced electrospinning techniques for the creation of functionalized nanofibers.
How well a specific polymer/solvent combination spins depends on the type of solvent-polymer interaction, and in this context, solubility emerges as a critical factor in identifying compatible combinations.
The solvent must effectively dissolve the starting polymer materials and various fluid properties, including viscosity, surface tension, elasticity and conductivity, significantly influence the ultimate properties of the fibers. When the Taylor cone is formed during the electrospinning process, for example, it is the Rayleigh instability that determines when capillary breakup occurs. To avoid unwanted breakup, it is important to find combinations of solvents with the right surface tension to match the viscoelasticity of the polymers related to the polymer concentration being used. Elmarco is now well positioned to advise on such challenges,
Over 600 Machines
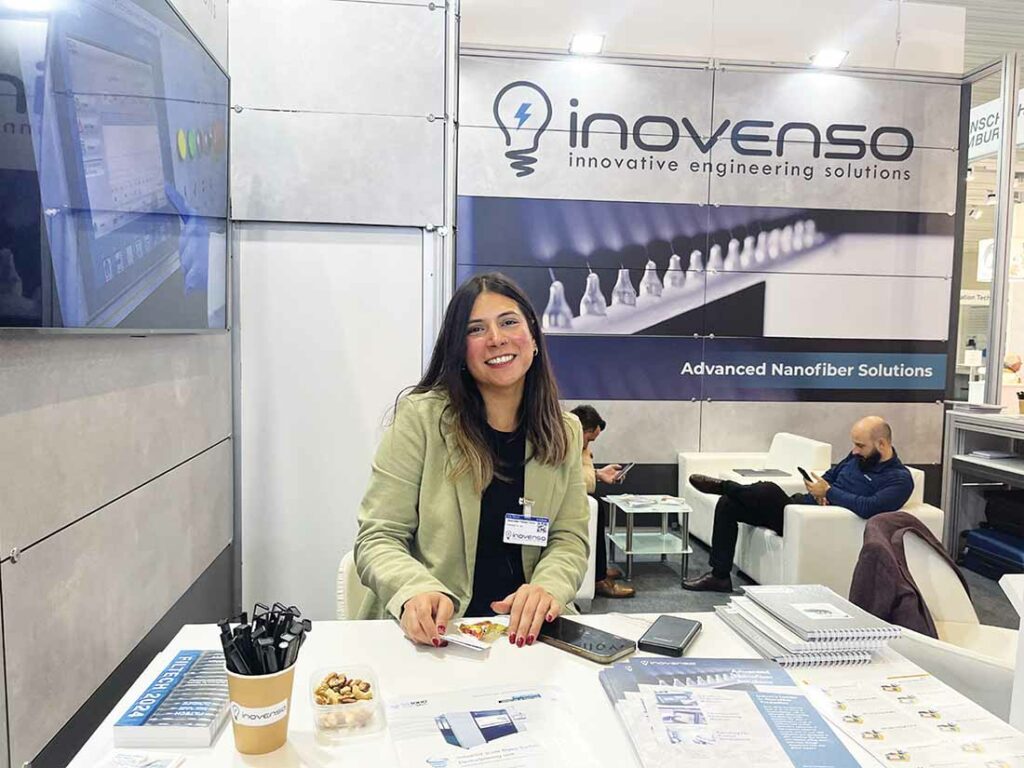
Another key manufacturer of electrospinning technology is Inovenso, with headquarters in Istanbul, Turkey and Incheon, South Korea, which has now sold laboratory, pilot and industrial-scale systems machines to over 600 institutions, universities and companies in more than 60 countries to date.
In 2017, Inovenso operations in Boston, Massachusetts were established to provide dedicated services to North American customers. At its Boston laboratory, the company also offers R&D services and demonstrations.
“Inovenso’s proprietary high-capacity Open Surface and StreamSpinner technologies open up new possibilities for applications in various industries,” said the company’s sales specialist Becky Tunio.
These machines are characterized by a smart dynamic feeding system that provides extremely homogenous production and precise adjustment of the flow rate, while their software sets the desired thickness by automatically adjusting flow rates and winding speeds. The patent pending technologies are compatible with a wide viscosity range of polymeric solutions.
Matregenix Expansion
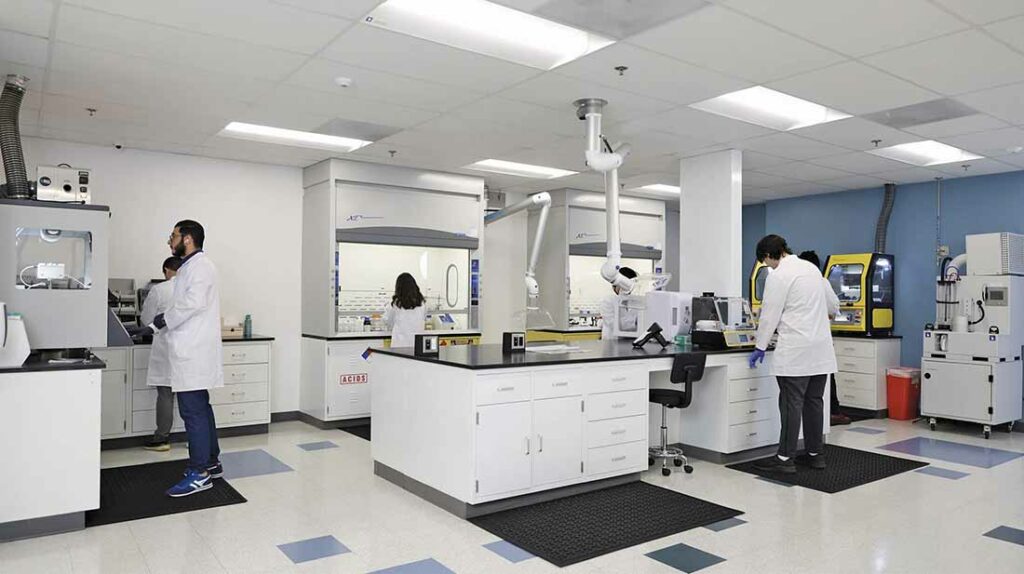
A new developer of both nanofibers and new machines for their production is Matregenix, founded in 2018.
In 2024 the company moved into a bigger facility in Mission Viejo, California, housing state-of-the-art clean rooms designed for clinical-grade manufacturing on a range of its proprietary nanofiber production machines, alongside fully outfitted laboratories.
The company’s key products include MatriNova for soft tissue repair, which establishes a non-biological, antimicrobial and programmable fiber matrix similar to the human extracellular matrix. Unlike other synthetic materials, MatriNova is said to break down into amino acids and does not produce acidic by-products that cause tissue inflammation. The new biomedical nanofiber structure promotes tissue growth while preserving strength and flexibility, presenting a new approach for the $20 billion soft-tissue repair market and shifting away from traditional xenografts, allografts and synthetic tissue-engineered scaffolds.
Turbo Technology
Matregenix says its proprietary technology also overcomes the challenges of consistency and scalability with electrospinning.
The company’s industrial-scale machines are modular, supporting both needle-based and needleless technologies. The Matregenix Turbo needleless moving head feeds a slit spinneret electrode connected to high voltage of up to 120 kv, allowing nanofibers to form from the thin polymer layer on the spinning electrode.
The roll-to-roll machine is available in working widths of up to 1.6 meters and can achieve speeds of up to 25 meters per minute.
Integrated Nanofibers
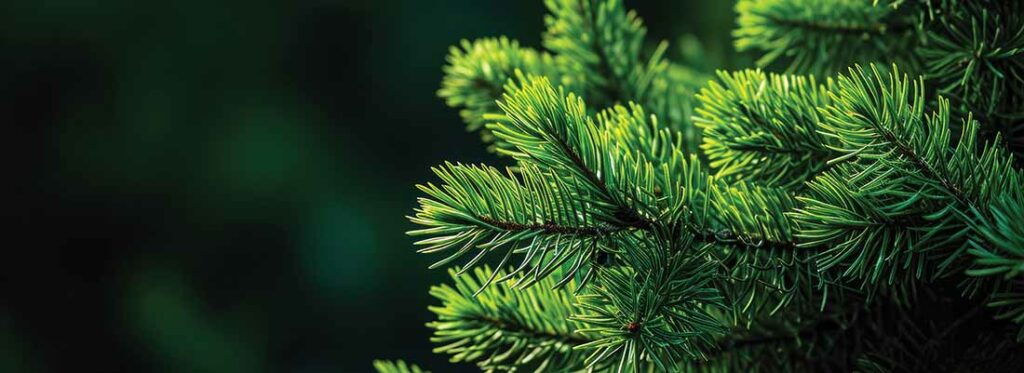
In other media developments, Mativ brand Gessner has developed MecNa, which unlike many nonwovens incorporating layers of continuous electrospun fibers, is characterized by individual nanofibers directly integrated into the nonwoven at formation stage, to enhance both durability and performance.
This media was initially developed in response to the Covid-19 pandemic, when guaranteed efficiency for critical healthcare-related filtration applications became essential.
The 3D nanofiber structured construction of MecNa overcomes the typical limitations of the reduced lifespan of filter elements due to low dust capacity, ensuring high initial resistance to airflow. Additionally, since it relies on mechanical filtration, there is no drop in particle removal efficiency as is often experienced with electrostatic filter media.
As such, MecNa ensures the consistent delivery of clean and purified air, seamlessly adapting to a diverse array of environments for both conventional and challenging settings like HVAC systems, industrial air filtration and clean rooms.
Lignin
Gessner is now saturating its wet-laid nonwoven cellulose filter media with lignin-based resins, as opposed to commonly-used phenolic products.
Lignin is a natural polymer found in the cell walls of plants, providing structural support and rigidity. Initial calculations show that the new lignin-saturated filter media offers a much lower carbon footprint. The cellulose-lignin media are currently being employed in various automotive filter media applications, including engine air intake, oil and fuel filtration, but are not limited to these. The use of the lignin also decreases formaldehyde emissions during the curing process.
Cabin Air and Alternative Drives
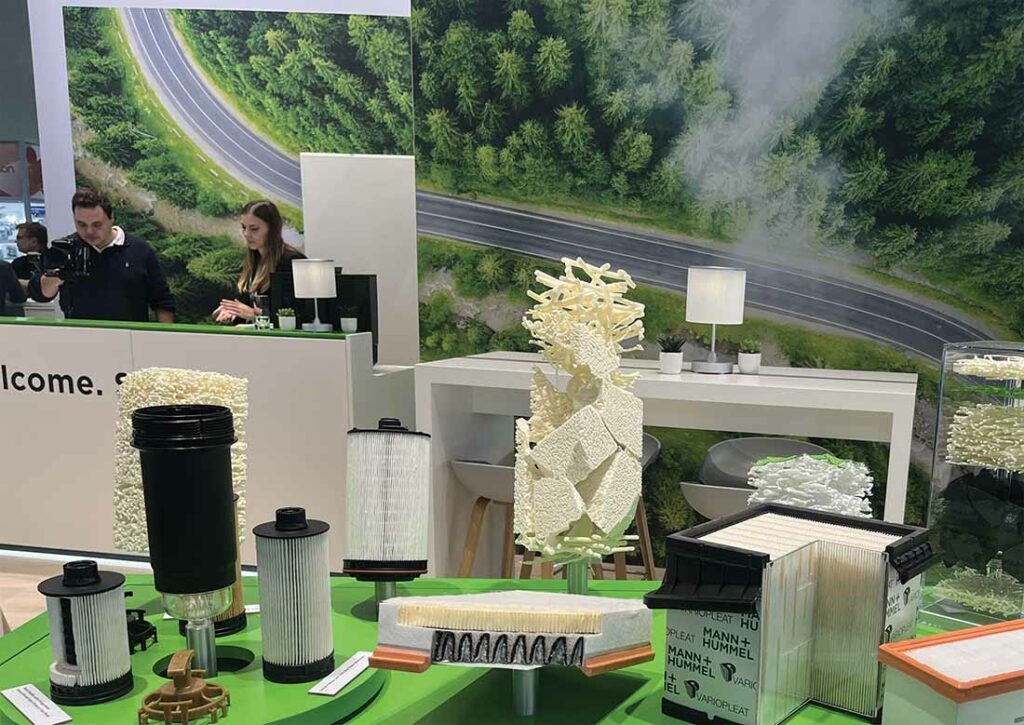
Tier 1 automotive industry supplier Mann+Hummel, headquartered in Ludwigsburg, Germany, is also now incorporating nanofiber layers into its cabin air filters for vehicles.
The layers increase mechanical separation to ensure that the performance of the filters remains consistently high over their service life. PM1 and ultra-fine particles, which can pose serious health risks due to their size, are effectively removed from the air.
Mann+Hummel is also developing solutions for alternative vehicle drives such as a new flat cathode air filter element developed to achieve optimum air quality and performance in fuel cell systems. This efficiently removes harmful gases from the cathode air path and protects the system from contamination and consists of four components. The first and second stages are a synthetic nonwoven for pre-separation and a cellulose particle filter element for high dust holding capacity. This is followed by an adsorption filter that efficiently removes harmful gases such as sulfur dioxide (SO2), nitrogen oxides (NOx) and ammonia (NH3), while a synthetic layer on the clean side ensures high cumulative clean mass (CCM) performance in respect of removing particulate matter.
Ionization and Polarization
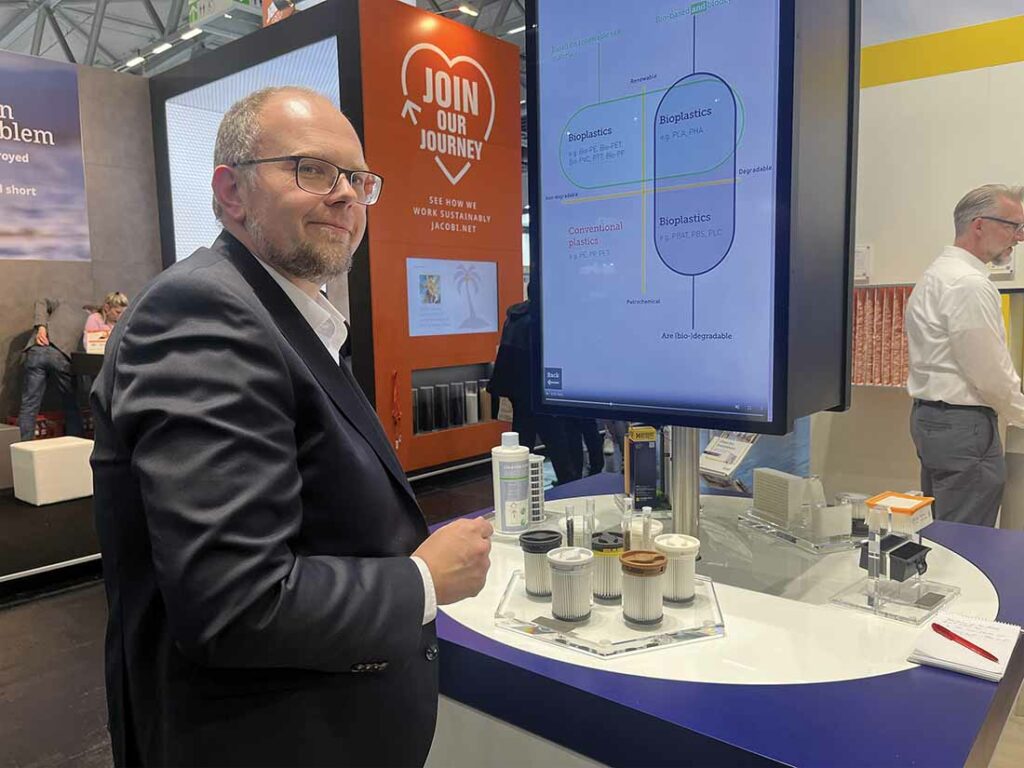
Another major German-headquartered Tier 1 supplier to the automotive industry – and rapidly expanding into other fields – is Münster-headquartered Hengst.
This company’s Blue.ion automotive cabin air filter achieves advanced purification through a combination of ionization of airflow particles and polarization of the filter media.
The ionizer ensures that the particles are electrostatically charged and makes them easier to filter via the media that is also charged. Ionization alone, however, will reduce the charge in the filter over time and lead to reduced particle separation. It’s at this point that polarization has a complementary effect. By building up an electrostatic field, the charge in the media is permanently maintained, ensuring consistently high filtration over the entire service life. This provides maximum protection against pollutants, viruses and allergens and makes a significant contribution to a healthy and hygienic interior climate in the vehicle. In addition, the filter has a compact design, requires little energy for the fan and produces only low noise emissions.
Resource Savings
Among a range of resource-saving developments for other sectors, Hengst has developed a replaceable filter concept for the vacuum cleaners of BSH Hausgeräte – the largest manufacturer of home appliances in Europe.
The plastic filter cassette is designed as a high-quality service life component and only the flat-fold filter, including the seal need to be replaced when necessary, to reduce the amount of waste. Resource-saving recyclate is used as the base material for the frame, and the packaging is also FSC-certified.
Grünbeck water filters are another example of sustainable with the filter media and end caps welded directly to each other, eliminating the need for adhesives.
“Every application has its own challenges, which can be solved with the right filters and the appropriate know-how, and our approach to sustainability is through intelligent production processes and product designs,” said Hengst product manager Markus Wilkens.
ProLine Double Gradients
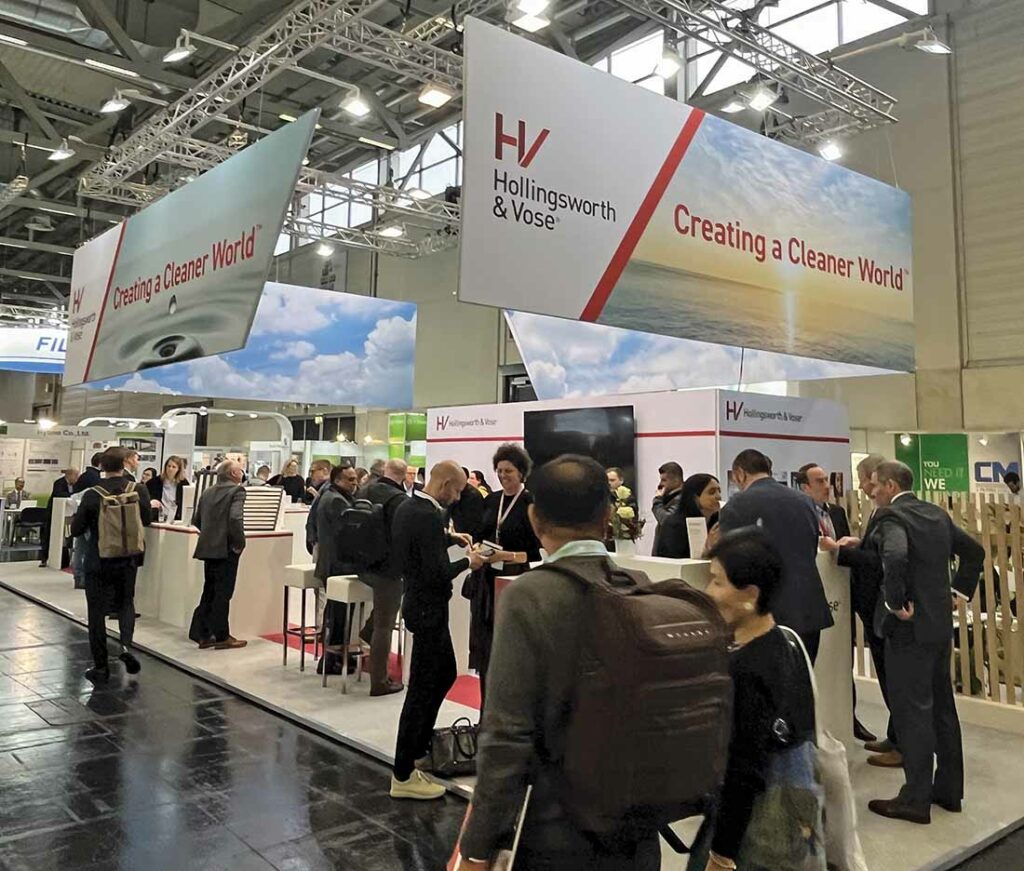
Typically, to achieve higher dirt-holding capacity for a given efficiency, a filter media is designed to be dual phase, with a gradient density in the Z direction.
Now, however, Hollingsworth and Vose has developed and patented a new media called ProLine which not only provides gradience in density, but also in fiber orientation.
The result is a significant improvement in dirt-holding capacity and air permeability for a given required efficiency.
A substantial rearrangement of the fibers in ProLine media generates both a higher surface area and new channels for air and liquid contamination capture. As a result, filter elements produced with it can also offer a significant improvement in both service life and/or pressure drop, or a combination of both.
This enables the basis weight of a specific ProLine media to be modified for an equivalent performance with lower media consumption in the filter. The initial development of the ProLine is focused on applications in hydraulics and fuel and engine air filtration.
PFAS Zero
Also new from H&V is the PlusZero range of high-performance media manufactured without using PFAS, or ‘forever chemicals.’
“After years of research, we have developed a line of zero added PFAS solutions that are not only better for the environment, but smart for business,” said Mike Clark, H&V’s division president. “PlusZero solutions will deliver the same high performance in most applications and largely carry the same price as their legacy counterparts.”
Pleating Machines
Through pleating, filters can offer increased surface area and density without impacting airflow, enabling more particles to be collected without increasing pressure drop or energy consumption.
The developers of pleating technology are continuing to enhance their machines and at FILTECH Switzerland’s JCEM demonstrated its latest P7 heavy-duty speed pleater for multi-layer mesh pleating with a fully automatic inline slitter blade changer, enabling slit widths to be changed without any operator involvement and without the removal of material.
JCEM’s latest P8 model can insert up to 500 25-40mm pleats into a media per minute, for a machine throughput of approximately 30m/min.
Length-Wise Cutting
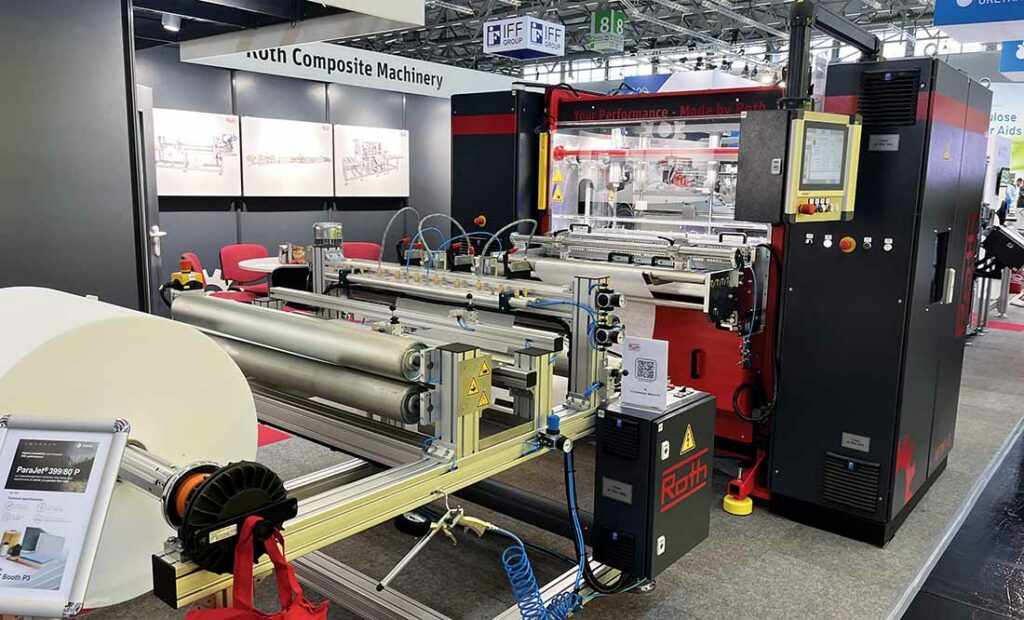
Similarly, Germany’s Roth Composite Machinery introduced its new MFM3-S servo-driven knife pleating machine with a high degree of automation and maximum speed of 510 pleats per minute and the company also presented a swiveling length-wise cutting system for knife pleating machines.
This enables an increase in production output, since the maximum width of the filter material is fed into the machine and the filters are cut through in individual widths lengthwise to the material web.
“If a customer wants to produce ten centimeter high filters, ten times the amount of filters can be obtained in one production run with a filter material of one metre width, compared to production with only one filter height,” explained senior sales manager Winfried Schäfer. “This is why length cutting systems are establishing themselves on the market and for better and risk-free handling in the production process, we have further developed the positioning of the cutter in the machine which brings a number of advantages.
“The operator can swivel the table by 90 degrees so that the cutter practically swings out of the machine. The swivel position is deliberately chosen at the centre of gravity of the infeed table so that the swiveling process can be carried out easily. The operator can make the necessary adjustments on the length cutter directly and without physical exertion.”
The cutting system is based on the principle of scissor cutting and works with round lower and upper knives. These run at a speed set by the machine corresponding to the folding speed.
Variations
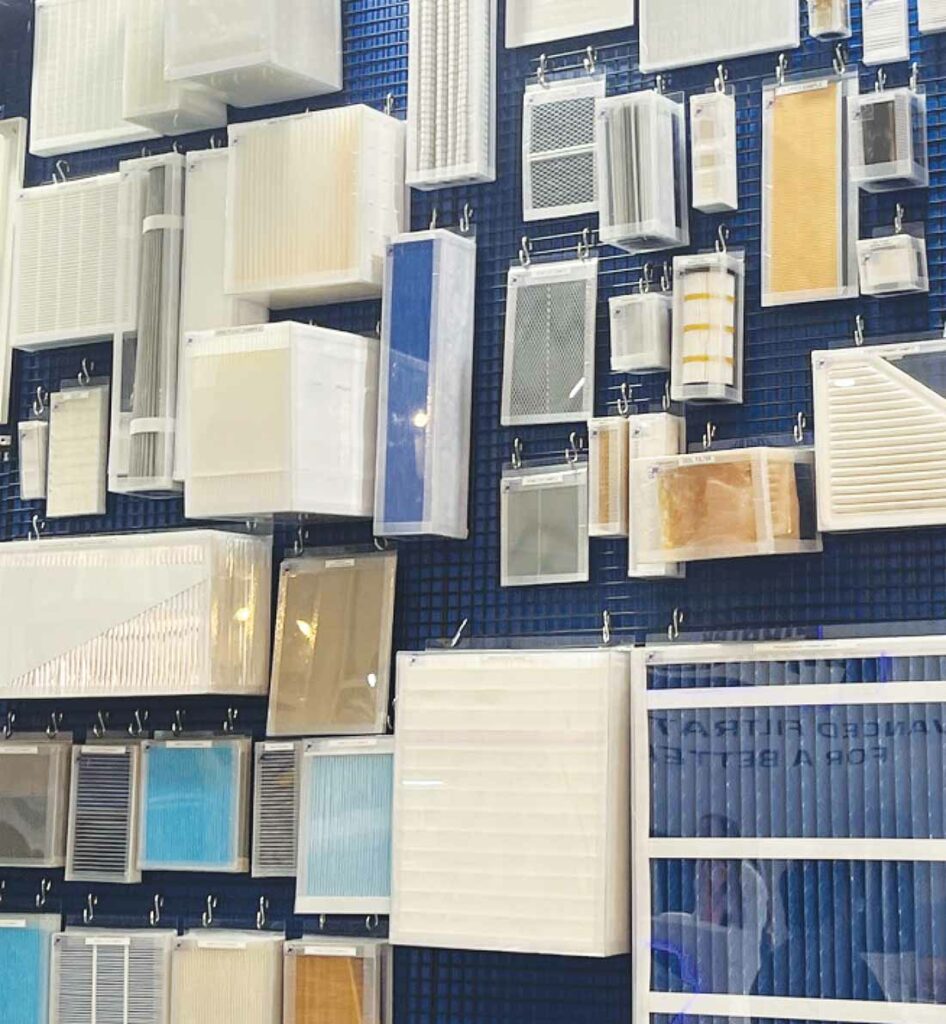
Versatility is meanwhile the key to the portfolio of India’s A2Z Technologies for cost-effective filter pleating, including blade, rotary, servo, star and mini pleating systems, as well as custom and hybrid solutions. A2Z specializes in working closely with its customers to identify the correct process to meet pleating needs.
At FILTECH, the company demonstrated the high speed A2Z mini pleat line with a foamed hotmelt system which enables a variety of media including glass fibres as well as synthetics to be processed, with change overs for pleat depth and pitch and hot melt patterns on the fly. The operator can save and access up to 2,500 stored product variations, allowing multiple combinations/part numbers to be produced. The machine’s unique flexible design helps filter manufacturers widen their product range and meet the market’s ever-changing needs.