Large-scale industrial manufacturing relies on heavy machinery and automation to meet its demanding 24/7 productivity and delivery targets. All too often, vital parts of an operation can be brought to a halt by unscheduled equipment repairs or replacements due to a component failure. And in a world where environmental issues are at the forefront, industry is increasingly looking at ways to conserve energy and resources, which means running machinery efficiently with limited throwaway parts.
A primary way of reducing machine failures and conserving the lifespan of the equipment is to implement appropriate industrial filtration solutions. They protect the integrity of the machinery by filtering out impurities and contaminants that may harm the integral moving parts, which can eventually lead to a breakdown.
In the longer term, protecting equipment from contamination improves efficiency rates, reduces the need for ongoing repairs or part replacements, and dramatically improves the usage lifespan of a particular mechanism. For businesses, this translates as dramatic savings in energy consumption and less materials wastage, which helps to reduce their environmental impact. It also means less downtime for the plant, which can result in missed delivery deadlines and disgruntled customers.
The old adage that prevention is better than cure stands true. Reliable machine engineering should focus on the prevention of the build-up of contaminants, but this is not always possible. Many processes using heavy machinery suffer the negative impact of impurities, such as particulates, liquids, and gaseous contaminants, which must be controlled and removed.
These unwanted contaminants are produced by a variety of processes and sources. They can be generated from the repetitive, abrasive movement of heavy machinery creating debris from friction and pressure. Impurities can also enter from the environment, built-into system components, included in the supplied oil, or generated from interaction with fluid additives.
Manufacturing equipment frequently encounters contamination that over time will result in detrimental wear within the mechanical structure which, decreases its operational longevity and functionality. Eventually, in a worst-case scenario, the ensuing damage to a key component may lead to a complete failure of a piece of machinery, resulting in an operational shutdown while the part is repaired or replaced.
Industrial filtration processes have the power to significantly reduce or eliminate exposure to these harmful contaminants. As such, they should be seen by plant operators as the most effective line of defense. Installing appropriate filtration safeguards should be a priority, as they are critical in limiting machinery downtime, which can have financial and reputational impacts. Boosting the reliability and longevity of costly manufacturing equipment also dramatically improves the return on investment, critical at a time when the world is under increasing economic stress as it emerges from a global pandemic.
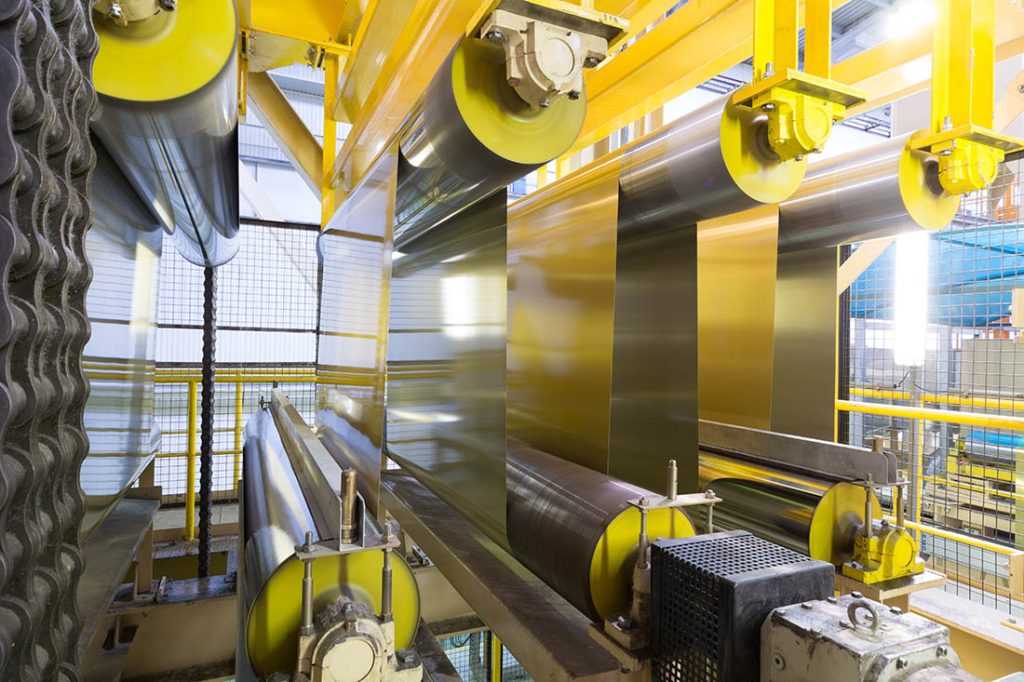
The other positive knock-on effect of good filtration practices is that maintenance planning is more effective. The servicing on equipment focuses on maintaining the condition of the machinery rather than responding to unscheduled, and sometimes catastrophic failures of a moving part resulting in an emergency repair. This means that running costs are significantly reduced as overall operational efficiency is improved.
There are numerous documented cases where contaminant control has been shown to have practical results. A Japanese steel mill reported that industrial filtration solutions have directly led to an 80% reduction in hydraulic pump repairs, accompanied by an 83% decrease in lubricating oil consumption. In addition, the plant saw a 90% fall in the frequency of lubrication failures across its plant.
These figures are impressive and certainly do not stand alone. There are countless examples where filtration solutions have led to marked improvements in equipment reliability and usage lifespan. In fact, those working in manufacturing and maintaining hydraulics systems attribute 80% of all component failures to particle contamination in fluids and not a result of an underlying weakness in the system’s components. Furthermore, analysis has revealed that contamination is responsible for more than 90% of rolling elements bearings failing before reaching their design life expectancy. A significant proportion of these premature failures are directly attributed to the presence of contaminants in the lubricating oil.
Digging down further into the available statistics again highlights the critical role that industrial filtration units play. At least 70% of hydraulic systems will seize up during their lifespan due to contamination. A significant proportion of these costly events could have been avoided had appropriate filtration solutions been implemented at start-up.
The most common cause of a machine breakdown is the result of a single component failure due to the degradation of surfaces coming into repetitious contact with fluid contaminants. This means that key parts will need to be repaired or replaced. In hydraulic systems, 20% of all replacements are the result of material corrosion while a further 50% are caused by particle induced wear and tear.
Furthermore, there is a four-to-ten-fold increase in the life of a pump, motor, gearbox, and transmission system where appropriate filtration units are applied. This solution can also eliminate valve stiction and promote the life of a valve by five-to-100 fold while extending fluid life.
Therefore, as part of an ongoing maintenance program, industrial plants must regularly scrutinize their filtration solutions to ensure that their performance continues to support the wellbeing of their equipment. These regular and thorough maintenance checks can also identify filtration-related weak spots within a manufacturing process, such as evidence of component decay or imminent failure which may result in a wider contamination event.
Filtration units need to be serviced to maintain peak performance, with filters replaced regularly as they complete their usage lifecycle. Filter replacement frequency is directly proportional to the working environment and the condition, age, and operating parameters of the machinery they are supporting.
Filtration must be a priority consideration for an industrial plant to ensure that its machinery continues to operate efficiently and effectively over its usage lifespan. Businesses realize that in an increasingly competitive world they cannot afford downtime while critical components are repaired or replaced. Installing the appropriate filtration solutions in advance and undertaking a proper maintenance program gives them the leading edge in keeping their operations flowing.