July/August 2014 | Volume 33, No. 4
In today’s world, effective filtration is becoming increasingly important. Whether it’s the air inside your residence, the drinking water in an urban metropolis, or the fuel in a heavy-duty vehicle, filters are being asked to do more. In turn, filter manufacturers are seeking optimum product solutions and cost-efficient application processes that deliver performance, quality, and value.
A variety of adhesive technologies have long been used for bonding and sealing a range of air, water, fluid and medical filters. The technologies include hot melts (EVA, PSA, polyolefin, polyamide, PUR), thermosets (polyurethanes, epoxy), flame-retardant products (polyurethane and hot melts) and low VOC and BHT content products.

While traditional hot melt adhesives continue to be the choice for many filter manufacturers, the associated assembly process is always under scrutiny for reduction in time, temperature and cost. The foaming of hot melt adhesives offers the solution many global filter manufacturers have been seeking.
THE FOAMING PROCESS

The hot melt foaming process utilizes a standard hot melt unit to melt and feed the adhesive through a heated hose to an in-line mechanical mixing head that mixes an inert gas (typically nitrogen based on cost and availability) into solution under hydraulic pressure. The hot melt is then released out of a heated hose and dispense head. Once the hot melt is exposed to atmospheric pressure, the nitrogen in solution expands as the hot melt is cooling – to ideally form a closed cell foam structure. The amount of nitrogen mixed in solution is critical in producing stable closed cell foam. Typically hot melts can foam from 30-60%, resulting in a 30-60% reduction in adhesive usage among the other benefits listed below
BENEFITS OF FOAMED HOT MELTS
Increased Open Time: Nitrogen bubbles insulate the material, increasing the work time and offering more flexibility.
Faster Set Time: Foamed materials require less force to compress, producing a thin bond line. The thin bond line decreases the set time for better production rates.
Volumetric Increase: Increased volume has better gap-filling capabilities to improve bond strength.
Reduced Adhesive Consumption: Foaming can reduce material consumption up to 60% percent depending on the hot melt material.
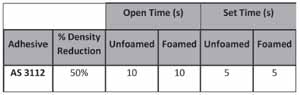
Increased Penetration: Foamed hot melt penetrates porous material for a stronger bond.
Improved Wetting: Foam requires less force to compress allowing penetration of impervious surfaces to enhance application versatility.
Lower Heat Density: Foamed hot melt materials reduce thermal distortion of temperature sensitive substrates and improve operator safety.
Reduced Sagging or Running: Thixotropic nature of foamed material reduces tendency of adhesives to run or sag on sloped surfaces.
ADHESIVE SOLUTION
Technomelt┬« AS 3112™ is a thermoplastic Ethyl Vinyl Acetate (EVA) hot melt adhesive/sealant that is specifically formulated to foam for use in industrial and automotive air particle filter operations, including pleating (Figure 3) and frame assembly as well as pass the UL 900 smoke test. The adhesive also has a low softening point of 203┬░F to allow for a lower application temperature translating into lower energy costs.
The Technomelt AS 3112 was evaluated at foamed levels from 20 to 60% and the results can be seen in Figure 1.
At a 20% foaming level, the density of the resultant adhesive is deemed to not allow enough cost savings to offset the capital equipment expense to foam. At the 30% and 40% foaming level, the resultant Technomelt AS 3112 hot melt adhesive is a closed cell foam. The optimal foaming level to achieve a closed cell foam structure and maximum cost efficiency was determined to be at 50%. Foaming levels of greater than 50% produced open cell foam, which was deemed over foamed (Figure 2).
When most hot melts are foamed, the foam itself acts like an insulator and prevents the product from cooling down as fast as if un-foamed. This could be an advantage for most applications as foaming would provide the best of both worlds: a longer open time or work life and a shorter set time or time to fixture (if used in a bonding application squeezed between two substrates to displace the heat). However, in a filter pleating application the adhesive is left in a bead and the heat is retained. Therefore, most hot melts that are foamed in a pleating application will likely have longer set times and as a result slow down the line or require manufacturers to take up more floor space to allow for product cooling.
The Technomelt AS 3112 is uniquely formulated to have the same open and set times foamed or un-foamed. This unique attribute makes the adhesive well suited for high speed pleating lines where the product can be used at the same speed foamed or un-foamed. This allows the line to maintain its fast throughput while realizing the 50% reduction in adhesive usage.
At the targeted 50% foaming level, the key properties of the adhesive were evaluated versus the un-foamed hot melt adhesive (Figure 4).
TECHNICAL PARTNERSHIP
Henkel has done extensive work with its comprehensive hot melt product line to determine the optimal levels of foaming. This allows for quicker and more complete adhesive recommendations. Companies can contact Henkel if interested in evaluating the foaming of hot melt adhesives for an existing or new assembly application, including a detailed report with optimal foaming parameters and a cost analysis that clearly indicates if foaming is a good technical and financial option to pursue. Henkel’s Filter Specialists will conduct production line audits; provide adhesive and process recommendations, and also present a cost analysis to validate the savings provided by foamed adhesives for filter assembly.