July/August 2014 | Volume 33, No. 4
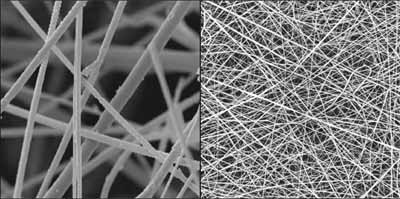
Nonwoven microglass fibers have been used for decades to address high performance material requirements in applications ranging from air filtration to liquid filtration and from acoustic insulation to thermal insulation, among many others. Microglass fibers are favored because their fine fiber diameters (often measuring in the nanoscale at the low end) generate high surface to volume ratios and small pore structures that in turn can be manipulated to create high performance media for these end uses. Furthermore, the glass is thermally and chemically stable so it can withstand many of the environmental challenges faced by the end product.
In recent years there has been a noticeable shift away from glass toward synthetic media. The drivers behind this move are the shedding of the glass fiber that leads to persistent health and safety concerns, abrasion that leads to equipment wear, and blocking problems in filtration applications1. Furthermore, the glass fiber tends to require high basis weights that are very thick, causing higher pressure drop performance that leads to high energy cost in the end application.
In order to overcome these challenges, nonwoven producers have turned to synthetic microfiber, which has demonstrated some promising results. However, synthetic microfiber media has lagged in matching the equivalent performance of glass media. Therefore, the technology roadmap calls for synthetic nanofiber (submicron), which is required to match the structure, surface area and pore sizes of the glass media that it is intended to replace2. With average fiber diameters of <800nm, <500nm, and as low as 200nm, nanofibers are not only capable of matching the performance of glass, but can often exceed the performance while reducing media thickness and weight by as much as 50%.
The primary challenge moving synthetic nanofibers into end products has been the severe limitations of the production platform. Productivity has been very low and operating expense has been very high. This production platform, electrospinning, utilizes high levels of solvents with solution concentrations of up to 94% solvent and 6% polymer that hinder industrial level production, which makes scaling difficult. Additionally, commercial level electrospinning is limited to a selection of solution-based materials dependent on their dielectric properties such as polyvinyl alcohol and polyamide 6. And while polyamide 6 has many uses, it may not be appropriate in applications where humidity may impact filter performance due to the hydrophilic nature of the resin. Furthermore, electrospinning has basis weight limitations with ranges reported between .02 gsm – .5 gsm3 and .03 gsm – 10 gsm4.
Forcespinning® technology is the premier platform for commercial nanofiber production because it uses centrifugal force to process a polymer solution or polymer melts into nanofiber. This leads to line speeds and operating cost equivalent to those of meltblown and glass fiber. Furthermore, the ability to melt spin polymers such as polyolefins and polyesters enable the use of robust cost effective polymers with fine fiber structures and pore sizes. And the ability to solution spin polyamides and fluoropolymers into nanofiber at basis weights up to 30 gsm in a single pass is unique and leads to superior performance in air and liquid filtration and other applications. The variety of materials made available through this mechanical process sets the stage for a revolution in nonwovens where synthetic fiber replaces glass in mid-level to high-end applications. Companies deploying Forcespinning technology in the filtration market space will have a strong competitive advantage as the go-to source for non-glass oriented high performance media.
The best way to demonstrate the superiority of synthetic nanofiber from Forcespinning over commercial grade glass media is by comparing performance at the highest level. In Figure 3, a direct comparison is made between HEPA filtration level glass media to HEPA filtration level synthetic nanofiber. The quality factor, which measures the filtration efficiency performance per metric of pressure drop (the impact on air flow) is plotted with the material weight required to achieve the quality factor. The HEPA rating specifies the efficiency so the determining factor is the pressure drop, which is very high in glass fiber leading to a lower quality factor rating than the nanofibers from Forcespinning.
The synthetic nanofiber has a quality factor over 40 while the commercial glass fiber media measures slightly over 25. This performance is achieved using less than half the weight of synthetic nanofiber compared to glass fiber. Hence, the synthetic media is much thinner, creating enormous opportunity in composite media and filter element design. The issues of high pressure drop and low permeability are performance-based challenges for glass fiber media in most uses.
Figure 4 demonstrates that at an equal pore size, the synthetic nanofiber has much higher air permeability (indicated by bubble size). Again, the performance differential is the result of synthetic nanofiber using less than half of the material to generate the same pore size structure.
Similar benefits are observed with liquid filtration. Figure 5 shows that synthetic nanofiber again requires less than half the basis weight to achieve a high level of efficiency for a 4 micron sized particle. In this example, Forcespinning has been used to melt spin PBT (polybutylene terephthalate), which is widely known to withstand the environmental challenges of fuel and oil separation in combustion engines among other challenging liquid environments.
Producing a similar or superior structure to glass, that can match the sturdiness of the glass media in demanding environments from a wide range of materials, is a unique capability that Forcespinning delivers. A range of products, including acoustic insulation and thermal insulation, are positioned to complement or replace glass.
Forcespinning is available to roll goods and vertically integrated companies only via the Fiber Engine® product line. This nanofiber production system is designed and manufactured by FibeRio Technology Corporation to provide the highest output of any nanofiber processing equipment in the world. This makes nanofibers commercially viable by providing superior performance or reducing the cost of media through lower weights. It is also the only equipment in the world capable of both melt and solution spinning nanofibers in a single system. This unique capability delivers a versatile platform technology that can be cost effectively leveraged into a multitude of applications while driving a differentiating factor for the end product.
The Fiber Engine FS 1100 is the first continuous production nanofiber system delivering Forcespinning technology to the production floor. It comes in multiple roll to roll configurations and can be configured for both melt and solution spinning.
The 1.1-meter width can be adjusted from 0.5 up to 1.1 meters wide. It excels as both a pilot and manufacturing line and is already being used in a variety of industries ÔÇö from filtration to medical devices. The FS 1100 is an order of magnitude higher in output than commercial electrospinning lines and is capable of turnkey nanofiber production processes, including:
- Polypropylene
- Polybutylene terepthalate
- Polyvinylidene Fluoride
- Polyamides 6
- Cellulose acetate
- A range of sol-gel derived ceramics
FibeRio is currently developing standard processes for Thermoplastic Polyurethane (TPU) and Polyethylene terephthalate (PET), which are appropriate for a variety of barrier applications. The company engages in joint development projects with roll goods, end application, and resin partners to provide unique nanofiber based solutions. The 15,000 square foot advanced nanofiber center is equipped with two full scale Fiber Engine FS 1100 systems and a custom high temperature test bed (process temps above 450┬░C) for engineered polymers. It also includes a comprehensive characterization lab with the capability to measure material viscosities, fiber diameters, basis weights, air permeability, differential pressure, porosity, and hydrostatic head.
FibeRio is continuing to scale the productivity of the technology to higher output rates and wider widths to meet the demands of the apparel, medical nonwovens, liquid filtration and, eventually, the hygiene industry. A next generation system, soon to be announced, will operate at lines speeds of 15-100 meters/min. These next generation high throughput systems further enable synthetics to penetrate the markets that have traditionally only had glass as an option for high performance filtration media. Forcespinning technology accomplishes all this while lowering the environmental impact by reducing raw material usage through lower basis weight requirements, efficiently using energy and eliminating or dramatically reducing solvent usage.
For more information contact:
FibeRio Technology Corporation
Tel: (956) 207-5448 Ext. 42 | Fax: (956) 665-8957
Email: kgramley@fiberiotech.com
References
- Ina Parker, G. C. (2013). Advances in Hydraulic Filter Media Solutions. AFS Conference Fall 2013 (pp. 1-21). Cincinatti: Ahlstrom.
- El Marco. (2010). NS Production Line NS 8S1600U. Retrieved July 10, 2014, from El Marco: http://www.elmarco.com/nanofiber-equipment/nanofiber-production-lines-ns8s1600u/
- Swaminathan, S., & Yu, H. (2013). High Efficiency Fuel Filtration Media. AFS Conference Fall 2013 (pp. 1-9). Cincinatti: Hollingsworth & Vose.
- Timothy Grafe, K. G. (2003). Nanofiber Webs from Electrospinning. Nonwovens in Filtration – Fifth International Conference (pp. 1-5). Stuttgart: Donaldson Company, Inc.