Fibers are main raw materials for making filter media in aerospace and automotive filtration applications. They can be chosen from a wide range of materials, including celluloses, thermoplastics, and glass fibers. Among them, cellulose fibers are popular choices in making filtration paper in fuel filters, cabin air filters, engine oil filters, and engine air filters in automobiles, aircrafts, and spacecrafts due to their advantages of good processability, desirable chemical and mechanical properties, and relatively low cost. The most common cellulose fibers available in the market for filtration purposes are plan-based pulp fibers, including hardwood pulp fibers, softwood pulp fibers, cotton pulp fibers, and their treated (e.g., mercerized, bleached) versions.
Cellulose fibers are bio-based materials. They are derived from cellulose, a natural polymer serving as a structural component of plant cell walls. Their bio-based origin means that they might have less environmental impact, or smaller carbon footprint, than their petrochemical-based counterparts such as polyethylene terephthalate (PET), and polypropylene (PP) if being manufactured in an appropriate way.
At the same time, cellulose fibers are also biodegradable, which means that they can be broken down to based substances such as water and carbon dioxide in a relatively short period of time by living organisms. However, as the used cellulose fibers contain oil and contaminants, and are mixed with metals and petrochemical-based fibers and polymers, they often end up being burnt in metal recycling or energy recovery facilities before they are decomposed by organisms.
On the other hand, used cellulose paper can also be broken down into single fibers by fiber disintegrators, after removing polymers and other unwanted substances. The single fibers can be used for making recycled filter paper. Research from China’s Tianjin University of Science and Technology (TUST) shows that recycled cellulose filter paper would have slightly lower bursting strength, stiffness, and tensile index than new paper, but still good enough to be used in some less demanding applications.
However, in real practice, cellulose filter paper is usually not recycled because this is not economically favorable – metal and oil are usually the primary goals of in a filter recycling process. In California, used metal-encased oil and fuel filters will be crushed and recycled to recover metal, while used paper-only oil and fuel filters are recycled as a source of fuel at energy recovery facilities. In some other places, filter paper is picked out from metal canisters or mesh by hand, and then made into a mush to separate out the oil – that mush is difficult to be recycled or reused, and often burnt or sent to landfills.
In fact, there are some patents that focused on recovering filter papers from engine air and cabin air filters. For example, the China-based Bengbu Hongfa Filters Co. Ltd. has a patented technology to recycle filtration paper from engine air filters by using high pressure nitrogen and a repair fluid. Although these kind of technologies have never been really commercialized, they may have a chance to take off in the future as a part of the world’s greener economy.
Bio-Based Cellulose Composites
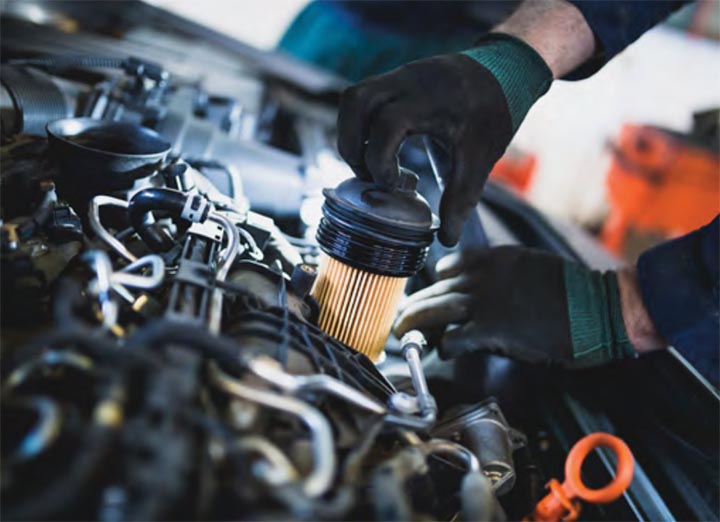
Different types of cellulose fibers are often mixed together to produce composites that combine their advantages for aerospace and automotive filtration applications. In general, hardwood pulp fibers are relatively low-cost, while softwood pulp fibers may have higher permeability.
On the other hand, mercerization treatment often increases a pulp fiber’s permeability and cost, while reducing its strength. In other words, composites made of different types of cellulose fibers may achieve a balance among permeability, pore sizes, strength, contaminant holding capacity, cost, and other characteristics.
The MA-based Hollingsworth & Vose (H&V) and the Finland-headquartered Ahlstrom Oyj (Ahlstrom), among several others, are leading global suppliers for cellulose fiber-based filter media. Other companies mainly focus on regional markets, providing tailored solutions serving their local customers. As a whole, they are actively working on developing new filtration composites with innovated structure, producing a substantial number of patented technologies related to aerospace and automotive filter media every year.
Some research also incorporates other cellulose fibers such as lyocell, viscose, and cellulose nanofilament (CNF) into the above-mentioned popular hardwood, softwood, and cotton pulp fibers. These composites provide additional functions while maintaining relatively low cost and bio-based and biodegradable benefits.
For example, the China-based Qilu University of Technology (QUT) developed a composite from hardwood pulp fibers, lyocell and CNF. Their research showed that when the lyocell content reached 60% in terms of weight, the composite would achieve a good balance between filtration efficiency and resistance – it can remove 98.97% of particulate matter 2.5 (PM2.5) when the filtration resistance is at 146.7 Pa. In this structure, CNF is applied on the surface of the composite to increase the efficiency for capturing small particles.
Recycling filter paper from used engine oil fibers is not yet economically viable, TUST’s patented technology does open a door to the future possibility.
Bio-Based and Degradable Binders
Binder is a crucial component for improving the mechanical properties of filter media. It is usually made of thermoset resins such as epoxy, acrylic and phenolic aldehyde, and applied to the fibers by spray impregnation, dip impregnation, or coating methods. In addition, it is often modified by or incorporated with other materials such as carboxylic nitrile latex to further improve its binding ability, and consequently the filter media’s mechanical properties.
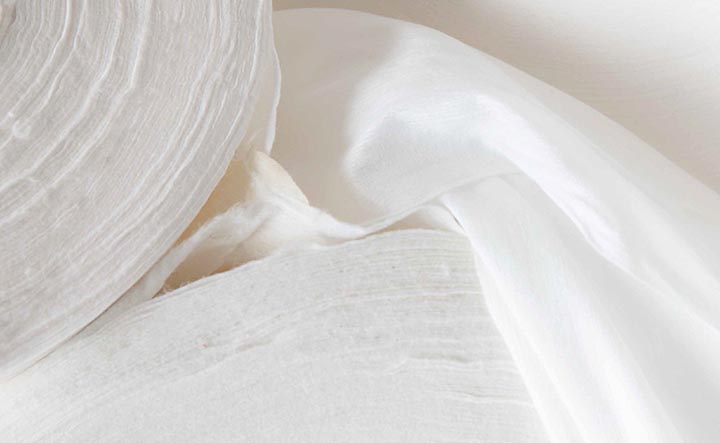
However, these thermoset binders are usually not bio-based, nor biodegradable. Although bio-based and biodegradable binders have shown in the market, their applications are currently not available for aerospace and automotive filtration. For example, the Sweden-based OrganoClick has developed a bio-based binder called OC-BioBinder™ from residual streams in the food industry such as orange peel, shrimp shells and wheat bran. It is used for binding nonwoven and technical textiles made from most fiber types, including cellulose fibers, showing a potential for a wide range of industries in the future, although it is not yet used in aerospace and automotive products.
Other researchers are trying to use petrochemical-based but easy-to-degrade binder materials to replace conventional thermoset resins. An example is a patented technology developed by TUST. This technology uses polyhexahydrotriazine (PHT) resin to replace phenolic aldehyde resin as a binder material for pulp fiber-based engine oil filter. TUST found that the degradation rate of PHT would reach 94.2% when the resin was put into a hydrochloric acid and acetone solution at a room temperature for half an hour. After removing PHT, a filter paper can be easily broken to single fibers and recycled.
TUST’s results showed that the tensile index and bursting strength of recycled cellulose fiber filter paper would decrease, respectively, 16.14% and 2.27%, while their other characteristics maintain at similar levels as original filter paper. Although recycling filter paper from used engine oil fibers is not yet economically viable, this patented technology does open a door to the possibility in the future.
Demand for Durability
Although being bio-based, biodegradable and having many other advantages, cellulose fibers often have to incorporate other materials, such as chemical fibers and glass fibers, to improve their durability and reliability when they are exposed in the environment where cellulose-based filter media could easily burst, for example, at a high temperature of 125 to 135°C (257 to 275F) in engine oil. The chemical fibers used for this purpose are mostly thermoplastic fibers such as polyethylene terephthalate (PET), polybutylene terephthalate (PBT), polypropylene (PP), polyamides (PAs), and polyacrylonitriles (PANs). The glass fibers used here are mostly microfiber with diameters of only several micrometers.
New composites made by these materials continue to show up. For example, in the last few years, Ahlstrom has developed a series of patented technologies for producing a series of self-supporting pleated oil media from cellulose fibers, thermoplastic fibers, glass fibers, thermoset binders, and additives. These media exhibit a much higher bursting strength than conventional oil filter media, while eliminating the use of expensive metal meshes that support the pleated structure to save some material cost.
There are also many other patented multiple-layer structures developed by other companies every year for the purposes of automotive and aerospace filtration. These activities indicate strong demands for new composites and structures in these industries, which have driven new advanced materials to enter the market as well. Examples include blended fibers made from electrospinning high-strength or high-thermal-resistant resins, such as aramids, polysulphonamide (PSA) and polyimide (PI), with other polymers. Although these materials still have not been available in the market at a large scale, their research and development will no doubt provide new solutions for filters used in tough or new environments, such as fuel-cell vehicles in the future.

Also, every material also has potential to provide additional benefits – a fiber could exhibit significantly different characteristics when it is in different forms. For example, researchers from China’s Xi’an Polytechnic University (XPU) developed a needle-punched nonwoven from regular PET and three-dimensional crimp PET as filter media for engine oil. When the proportion between regular PET and its three-dimensional counterpart readjusted, the nonwoven’s strength, bulk, pore sizes, permeability, and filtration efficiency of the filter material would change accordingly. A desirable combination of different filtration properties can be achieved in this process.
Nanofibers made from different types of materials have also long been used to increase the filters’ ability to capture small particles. For example, the Ultra-Web® Media Technology by the MN-based Donaldson Company, Inc., which adds a layer of nanofiber on cellulose media, provide a filter media with high dust holding capacity and high filtration efficiency in engine air filtration.
The China-based Newstar Industry (Newstar) also developed a filter material with a nanofiber layer. The base filter paper is a composite made of cotton pulp fibers and softwood pulp fibers. Newstar’s research showed that with additional 4% nanofibers added on the filter paper’s surface, the filter media will have an average porosity of 23.8 μm, while maintaining an air permeability of 115.4 L/m2s when the pressure difference is at 200 Pa. This filter material also shows desirable bursting strength and excellent initial filtration efficiency for removing nanoparticles.
Evolving Media
The cited examples illustrate that cellulose fibers are often partially or even totally replaced by petrochemical-based and non-biodegradable fibers when pursuing durability and reliability. On the other hand, bio-based or biodegradable fibers, such as PLA, chitosan and nylon 56, are also being researched to replace petrochemical fibers in these applications. Some research even focuses on the development of PLA composites for air filtration applications, including cabin air filtration. Although the use of these bio-based materials is still in early stages, a promising and fast-growing market could be expected for the future – similar to what has occurred in the bioplastic industry.