Membrane press filtration is at the heart of the sustainable system that has been established for the treatment and storage of sediment removed from the waterways of Port of Antwerp-Bruges in Belgium.
Port of Antwerp-Bruges is the second largest port in Europe with more than 300 liner services to more than 800 destinations. Every year it handles around 290 million tons of international maritime cargo, in addition to being home to Europe’s largest integrated chemical cluster.
The port directly and indirectly employs a total of around 164,000 people and contributes added value of more than €21 billion to the Belgian economy.
Enabling Draught
As a naturally occurring material which mainly consists of rock and minerals that are broken down over time by weathering and erosion, as well as the remains of plants and animals, sediment moves throughout waterways due to tides, wind and waves, and settles in quiet areas of the water.
Over the years, Port of Antwerp-Bruges accumulated an enormous amount of sediment which was hampering its navigability.
Sufficient “draught” – enabling movement for shipping traffic – is essential and to guarantee this, a large volume of sediment has to be dredged annually. At Port of Antwerp-Bruges, former sediment storage techniques, such as dumping it in quays or underwater cells in a dry dock complex became saturated and such solutions also became unacceptable from a social and environmental engineering standpoint.
AMORAS
Back in 2008, plans were established to develop a unique solution to this problem with the AMORAS – Antwerp Mechanical Dewatering, Recycling and Application of Silt – project. The project was awarded to the temporary trade association SeReAnt, a combination of Flemish dredging company Jan De Nul and Dredging International (DEME), supported by their environmental contractors, with an initial grant from the Flemish government of €480 million.
The plant, which became operational in 2011 and is running until 2026 with operational costs of €29 million per year, ensures the annual treatment and storage of approximately 500,000 tons of dry material dredged from the port each year and dewatered by a minimum of 60%.
Employing around 100 people, this is Europe’s largest processing installation for maintenance dredged sediment.
Preparation
The system starts with an underwater cell zone with a capacity of 300,000 cubic meters, in which the sedimentation dredged from the port docks is temporarily stored before being pumped to the shore for the treatment process to commence.
It then has its coarser elements removed in a sand separation zone using hydroclones which are adjusted to a separation point of 63 microns – the granulometric limit between the sludge and sand fractions. Up to 80 tons of sand is separated and removed every hour based on the difference in density of the two fractions.
Thickening Basins
The remaining sediment is then pumped over a distance of four kilometers through discharge pipelines, with a maximum throughput of 1,500 cubic meters per hour, to the Bietenveld treatment site where it is buffered into four thickening basins, each with a capacity of 120,000 cubic meters.
After a week in the thickening basins and conditioning with lime or poly-electrolytes, the mixture undergoes a further dredging step with two mobile dredge pumps on a 175-metre-long rotating gantry spanning the thickening basins and allowing for fully automated steering of the process. The pumps can move along the entire span and can operate independently of one another. This process makes it possible to feed the filter press with a nearly homogeneous mixture.
Filter Press
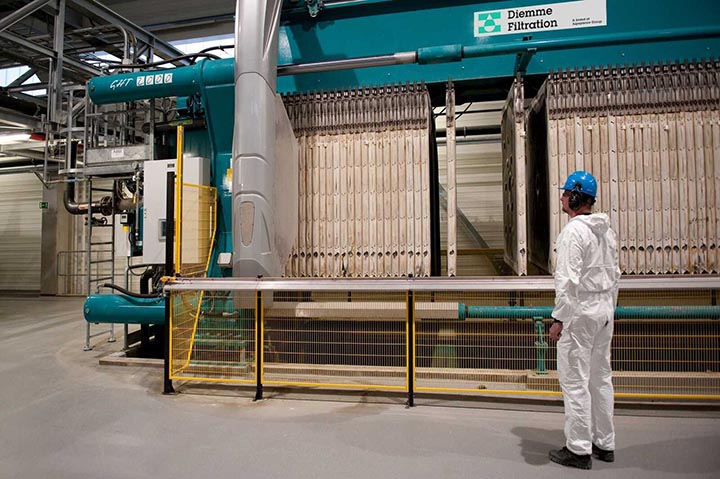
The filter press, supplied by Italy’s Diemme, consists of 12 of the company’s GHT.2000.P19 lines, which are each 27 meters long, five meters high and five meters wide.
This configuration’s 193 vertical membrane filter chambers can produce approximately 30 tons of filter cake with at least 60% dry matter per 90-minute cycle, for a daily capacity of 3,000 tons of filter cake over a 24-hour, three shift operational day.
Diemme has worked alongside the partners since the project’s inception to ensure the smooth running and regular maintenance of the filter press.
The filtered water is then buffered into a wastewater pond before being treated with a two-stage purification process involving a physio-chemical pre-treatment for fine particulate matter and then biological purification via a suspended activated sludge system.
The filter cakes produced are stored under controlled conditions at a 30-hectare site that was formerly a sand extraction pit. Using phased and controlled storage, the aim is for the site to have an operational period of at least thirty years. Potential second-life uses for the filter cakes have been explored, and in parallel with Amoras, the Vamoras project has looked at ways of recycling them as fillers in bricks, lightweight aggregate or concrete for foundations.
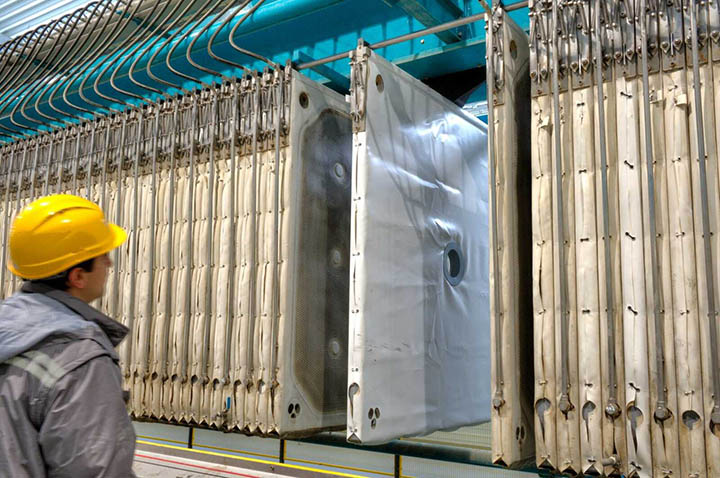
Technology of Choice
Diemme, which is part of the multi-national Aqseptence Group and headquartered in Lugo, Italy, was formed in the early 1970s at a time when the use of filter presses was expanding from traditional applications in the food industry to other industrial sectors as a process technology for the separation of solids and liquids.
Subsequently, the filter press has become the technology of choice for the treatment of industrial and municipal sewage sludge across the mining and chemical industries, power plants and the oil and gas sector, where high dewatering performance, low operational expense and reliability are key drivers.
Diemme’s filter presses were chosen for the AMORAS project at Port of Antwerp-Bruges after a detailed analysis of various technologies, including centrifuges and belt presses, and selected based on the high flexibility of the equipment and the optimal total cost of ownership.