With benefits including precisely tailored flow rates and accuracy – wire diameters and mesh apertures can be customized to perfectly match targeted contaminants – woven metallic filter fabrics continue to be essential for many demanding filtration operations.
In addition, metal mesh filters – primarily made from stainless steel – can withstand a wide range of impurities, pressure changes and extreme temperatures without compromising performance, in addition to thorough backflushing and cleaning regimes.
At the recent FILTECH 2022 held in Cologne, Germany, March 8-10, specialists in metal mesh filtration, with many decades of knowhow, were well represented.
Proprietary weaving
They included Haver & Boecker, of Oelde in Germany, which was founded in 1887 and has developed advanced proprietary weaving technology in-house, enabling the production of a wide range of media based on wires of stainless steel, as well as non-ferrous metals including aluminum, nickel, phosphor bronze, brass and copper in diameters of 16mm down to 0.015mm.
The company’s recently developed Minimesh RPD Hiflo-S has a three-dimensional pore geometry with a significantly increased open surface area that can make a number of industrial filtration processes more efficient, faster and more economical than previously possible. Compared to a conventional filter cloth of the same pore size, Minimesh RPD Hiflo-S has twice the flow-through rate, with optimized flow conditions and turbulence around the media effectively avoided.
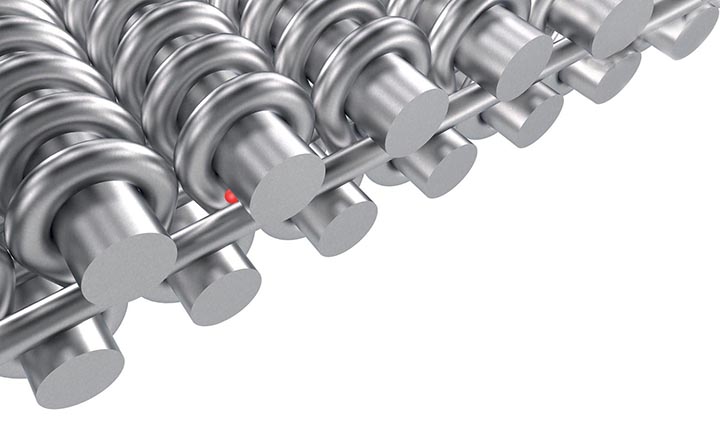
The pore size within a batch can be calibrated as desired from 5μm to 40μm and it is now possible to create corrosion and temperature-resistant filter media with pore sizes below 40μm. The depth structure of Minimesh RPD Hiflo-S provides a high separation effect without rapid blinding and enhanced dirt-holding capacity.
Haver and Boecker uses GeoDict software, developed by Math2Market, of Kaiserslauten, Germany, for the multi-scale 3D image processing, modelling of materials, visualization, material property characterization, simulation-based material development and optimization of processes. With GeoDict, the company is able to determine in advance the best-suited media configuration for specific applications.
Working closely with the Institute of Mechanical Process Engineering (IMVT) in Stuttgart, Haver and Boecker has also carried out extensive research into the effects of different gradient structures and layer configurations in single and multi-layered woven wire mesh combinations. Through specific selection, both load-dependent fractional separation efficiency and dirt-holding capacity can be positively influenced for improved service life.
At the recent FILTECH 2022 held in Cologne from March 8-10, specialists in metal mesh filtration, with many decades of knowhow, were well represented.
Sintered products
Another major German player with long experience in this field is Dorstener Drahtwerke (DDD), founded in 1918 and a weaver of stainless steel and corrosion and heat resistant alloys as fine as 3 microns for strong and precise filter media.
An important development for this company has been in the production of diffusion-bonded – sintered – woven wire mesh, which provides opportunities to enhance performance in many applications.
The SinterPore range of materials is produced by DDD company Porous Metal Filters in Spring, Texas, via precise diffusion bonding.
Its robust, monolithic materials are used in a wide variety of engineering applications ranging from industrial filtration to aerospace transpiration cooling, while two and three-layer SinterPore fluidizing laminates with customer-specific permeability and flow rates are often used in bulk powder handling. Standard five-layer laminates are meanwhile used in pharmaceutical, polymer, liquid and gas filtration processes, and fully cleanable filter element cartridges are available in an infinite range of woven and nonwoven metal laminate materials. Custom cartridge designs are highly permeable and back washable, with superior cake release properties, and filter element cartridges are available in a broad range of micron ratings, permeability and mechanical strength.
A woven mesh sandwiched into a light gauge, welded mesh is another recent DDD development for applications in which larger woven mesh partitions need stability – often a requirement for air intake applications in pre-filters.
Magnetics
Magnetic filtration is a specialist field of MTK, based in Solingen, Germany, with a wide range of industrial applications.
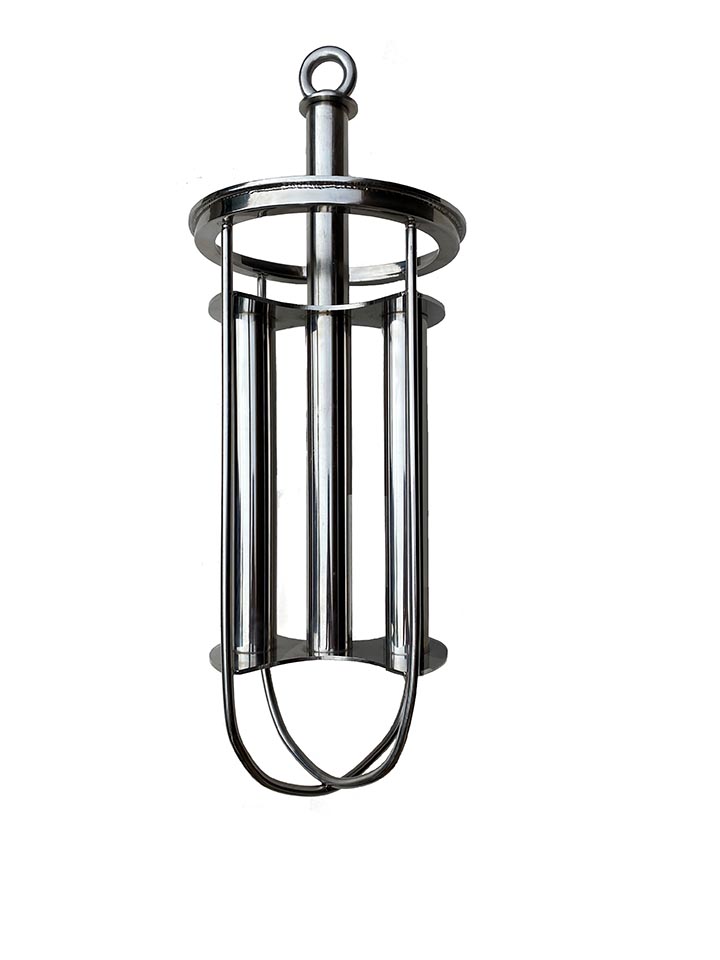
MTK’s funnel magnets are particularly suitable for filtering out ferritic impurities in plastics processing, on injection molding machines and extruders, and for the special processing of granules, regrind, powder or liquids. The company’s filter rods are an effective and cost-efficient method of removing ferritic impurities from coolants, hydraulic fluids and lubricants, sliding emulsions, etc., and their service life is practically unlimited.
With an easy clean variant of the filter rods which are held in place by magnetic racks, cleaning couldn’t be quicker – once removed from their housing the rods simply lose their magnetism and discharge the collected filtrate.
SLM
Ushering metal filter manufacturing firmly into the 21st Century is Croft Additive Manufacturing, based in Warrington, UK, which for a number of years has been developing selective laser melting (SLM) as an additive manufacturing (AM) technology for the creation of components layer by layer, delivering the design freedom to produce complex geometric components.
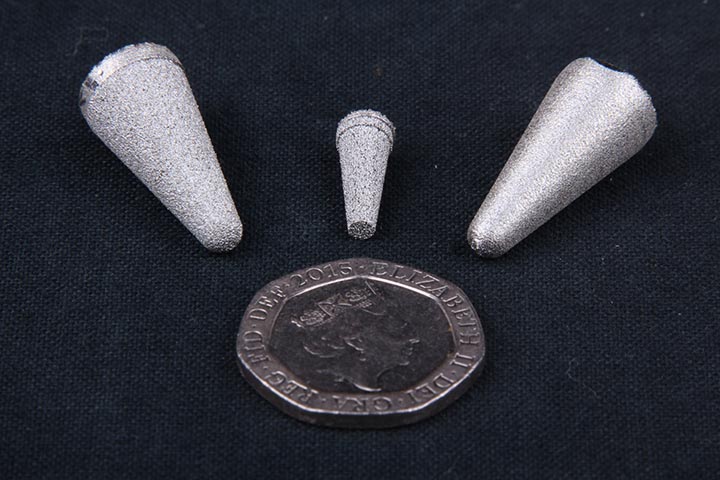
In a paper presented at FILTECH 2022, the company’s director, Neil Burns outlined the added value that the AM process can deliver to improve filter media efficiency, using design to add function.
The overall shape and size of metal filters is defined by end-user requirements, in terms of aperture size, as well as considerations such as available space and operational pressures, Burns explained. For coarse filtration, the media can consist of screens and filters manufactured with wedge wire, a sieve formed from perforated plate or a single layer of woven wire mesh. For finer filtration, the media aperture size can range from millimeters to the nanometer range. Finer woven wire mesh alone, however, can become distorted if damaged under operational pressure and flow rates.
Aperture alignment
When a filter is employed in a conduit, it forms a barrier and thus creates resistance. Resistance across the filter is due to the pressure differential, with fluid flowing from high to low pressure across the filter. The pressure drop across the filter is dependent on the fluid flow rate and the amount of resistance that the filter type exerts on the fluid. More energy is required in the pumping/filtration system by increasing flow rates to overcome the filter’s inherent resistance.
SLM technology has been exploited at Croft to produce the company’s Straightliner cone filter, which has apertures perfectly aligned to its fluid flow.
When passing through a cone filter, Burns explained, fluid has to turn away from the direction of flow to pass through the filter media and then turn again to continue to flow through the pipework. Movement of the flow from the directional flow path creates turbulence and pressure drop across the filter. Allowing the fluid to pass through the filter without turning reduces this turbulence and hence the pressure drop.
The principal of engineering the holes in line with the fluid flow has been applied to a latticework design where the filter support and filtration portion are integrated together as a single part.
Supports
For powder bed fusion AM – where the laser melts the metal powder – build supports are added to anchor the part to the build plate but in addition, build supports must be added to support overhangs of parts to prevent the meltpool from being swept away.
A filter support portion in a conventional filter is designed for optimized geometry and loading to provide strength and protect the mesh from damage, as well as supporting the mesh to prevent buckling or collapse under increasing fluid flow. Woven wire mesh when in planar form has uniform aperture size and shape.
However, when the woven wire mesh is shaped through an angle, the aperture size and shape become distorted and are no longer uniform. In conventional filters, when the filter support is covered with woven wire mesh, the mesh conforms to the shape of the filter, is no longer planar and so can have variable pore shapes and sizes.
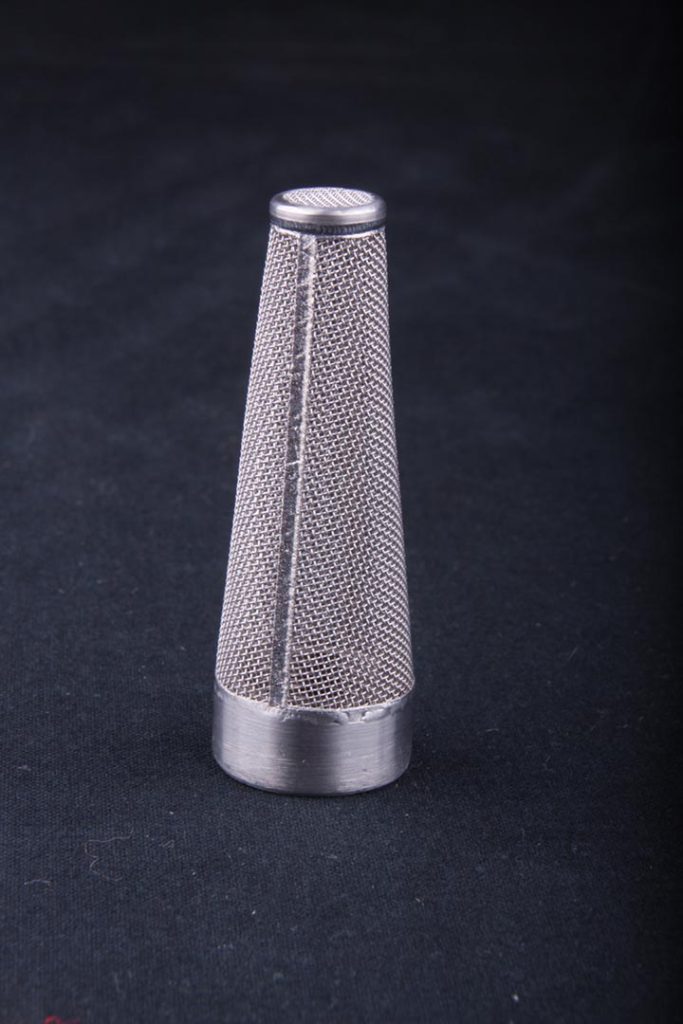
This led to the development by Croft of a filter assembly that has integrated support and filter layers in which the repeating units form the support due to the strength of the metal lattice, and the rigidity prevents distortion of aperture size.
The results demonstrate that by engaging with AM technology that can manufacture parts layer by layer, novel arrangements of apertures are possible in a filter that can directly reduce the turbulence of fluid flow through the filter. This reflects a decrease in the pumping energy required and hence a potential decrease in energy use of at least 15%.
Hybrids
Further benefits can be obtained from hybrid filter media, Burns explained. Filter media manufactured using woven wire mesh alone have a maximum open area outside of the welded joints. The overall strength of this filter type, however, is low and Croft has employed AM to add support structures to woven wire mesh so that when the filter media is formed, the mesh-only filters have a greater overall strength. The filter design can be customized and the amount of supports can be varied. The strengthened mesh-only filters can then be welded to conventional fixtures.
“SLM AM has been used successfully to manufacture innovative filter media that have a greater efficiency through their design, as well as lower lead times,” Burns said. “Conventional woven wire mesh has also been combined with the AM process to create a new type of filter media that has additional strength compared to conventional mesh-only filters.”