Nanofiber media will increase market share in a changing mobility market. It will provide the lowest total cost of ownership based on an efficiency-to-energy consumption ratio, as well as on initial and maintenance costs. There are two major sub-segments of nanofiber media, depending on the thickness of the fibers and the methods by which they are produced.
With the growth in electric vehicle use there will be a big market for nanofiber media in electric vehicles. Meanwhile, the market for filters used with fossil fuels will be negatively impacted. Cabin air will not be impacted by the EV surge, but it will be positively impacted as the recognition of the need for cleaner air for occupants of mobile equipment continues to increase.
Process | EV Impact |
Battery Separators | Significant |
Brake Dust | None |
Cabin Air | Slightly Positive |
Diesel Emission Fluid | Negative |
Diesel Fuel | Negative |
Engine Air | Negative |
Engine Oil | Negative |
Hydraulic Fluid | None |
There is both a mobile and stationary application for most of the aforementioned processes. This analysis focuses on the mobile applications.
Passenger | Goods Transport |
Construction | Industrial | Agricultural | |
Vehicles | X | X | X | X | X |
Trains | X | X | |||
Water craft | X | X | X | X | |
Aircraft | X | X | |||
Equipment | X | X | X |
Battery Separators: The battery separator market for mobile applications will be significant, but in addition there is big initiative for battery storage for electric power delivery.
DuPont introduced the first nanofiber-based polymeric battery separator.
Researchers at the University of Waterloo classified electrospun separators into five major types: monolayer separator, multilayer separator, modified separator, composite separator and gel polymer electrolyte separator.
Hollingsworth & Vose has developed a family of hybrid separator platforms, as well as the traditional 100% microglass separator.
Brake Dust Filters: Mann+Hummel has introduced a filter to capture the mechanically generated dust created in braking.
Cabin Air Filters: This is a growing market for nanofiber filters. BMW is promoting a cabin air system based on nanofiber filtration and intermittent operation to minimize energy consumption while ensuring clean air for occupants
Diesel Emission Fluid: Urea filters are required wherever SCR NOx control is mandated. Particles 1 micron and larger need to be removed.
Diesel Fuel: Cummins NanoNet technology incorporates a combination of proven StrataPore layers with nanofiber media layers. The Fleetguard high-horsepower FF5644 fuel filter was compared to the NanoNet upgrade version, the FF5782. The FF5782’s higher level of efficiency translates into longer injector life, reduced down time and repair costs, as well as increased uptime and revenue potential.
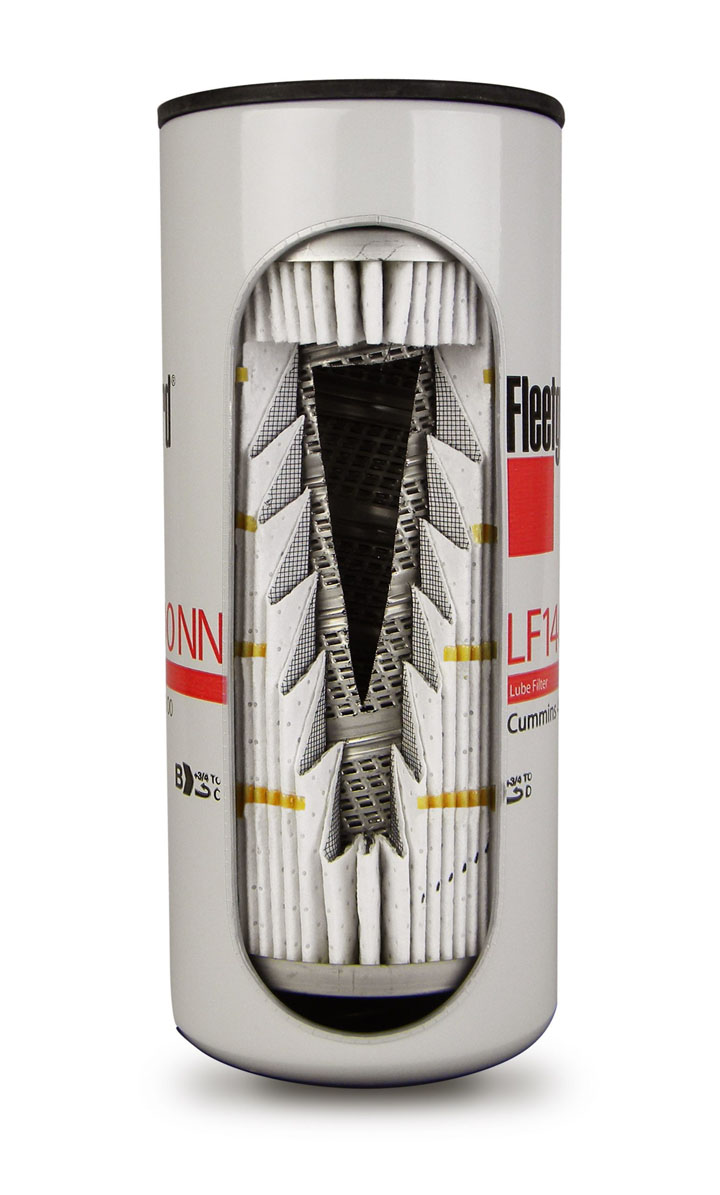
Engine Air: Nanofiber filter media from Mann+Hummel is used in commercial vehicle air filters. It offers an extremely high dust separation efficiency of up to 99.99% for the separation of particles together with low flow restriction and a long service life.
With the Parker Hannifin – Baldwin ProTura nanofiber media, the fine contaminants tend to load on the media surface resulting in higher initial contaminant removal efficiency. The contaminants can be removed by the dust ejector, increasing the filter’s contaminant removal capacity
Engine Oil: The LF14000NN reveals a combination filter. Approximately 80% of the oil flow goes through the Fleetguard StrataPore media, and the remaining 20% flows through the upper NanoNet section to super clean the oil.
Hydraulic Fluid: Donaldson Synteq XP synthetic liquid media delivers high filtration performance in engine, hydraulic and crankcase applications.
Industry experts were interviewed to learn about their perspective on the market opportunities.
Kari Lukkonen, business development manager for Fibertex has a long-standing involvement with nanofibers.
Q: Kari, just how long have you been in the nanotechnology sector and with whom?
A: I started my involvement in electrospinning in the year 2000 when the company I worked with at that time, named Raisio Chemicals, had a joint venture in Korea. Electrospinning was one of the areas we were experimenting with as a longer term R&D project. Eventually Raisio Chemicals was sold on year 2004 and the electrospinning project was continued by the Raisio Chemicals JV partner Jong Chul Park in Korea.
The new nanofiber company was founded 2005 by Jong Chul Park and named Finetex, starting a production plant in Philippines. I joined Finetex in year 2005, and then Fibertex Nonwovens in year 2018 when they established a nanofiber production in Denmark.
Q: The mobile sector has a number of applications; which do you think are the most promising for nanofiber media?
A: Heavy-duty air intake is probably the first and still the largest application area for nanofiber coatings in air filtration. The second established area has been diesel fuel and oil filtrations with larger and thicker nanofiber fibers. Today we also see a growing interest in cabin air for mechanical filtration instead of the traditional electret meltblown.
Q: Why do you single out “cabin air”?
A: The need for better filtration, larger space available with electric cars, etc.
In the average car when the AC system is running, most of the air is circulating back to the cabin. In a relatively short time the amount of small particles accumulating inside the cabin grow to about four times higher than what is the small particles amount outside of the car.
The traditional electret meltblown filters initially have a high efficiency, but loose the electrical charge potentially very quickly when exposed to small particles, especially soot in heavy traffic. Now during the COVID pandemic these filters are not effectively able to filter very small particles like virus-containing aerosols accumulating in the AC system and circulating in the cabin. On average the cabin air filter is changed in most cases once in a year, and it is highly questionable if the filter can perform adequately during this time.
In addition to the need to secure the functionality of the filter media during the lifetime of the filter, new electrical vehicles allow for more space for cabin air filter systems. More space for the filter can be used for a better filtering system. A good example is the Tesla models, many of which have HEPA-level mechanical filter systems to ensure cabin air quality.
Q: How are nanofibers best used for cabin air filtration?
A: With nanofiber-containing filter media, new electrical car models can be equipped up to HEPA 13 or lower efficiency filters, which will perform optimally during the lifetime of the filter. For the existing ICE vehicles, where space and the fan motor limit the design of the filter media, MERV 13- to MERV 15-level of filters can be achieved depending on the design of the filter system. Securing the minimum MERV 13 efficiency for the lifetime of the filter – similar to the recommendation by the U.S. Centers for Disease Control – for HVAC filters in buildings can help to reduce the amount of potentially harmful small aerosols in the cabin.
Damien Deehan, co-CEO of Verdex Technlogies, chose an interesting mobile application for his response.
Q: What assistance can Verdex provide in making better nanofiber filters for mobile applications?
A: With Cruise Ships still stranded at ports throughout the world due to COVID-19, upgrading HVAC systems is critical in getting the cruise industry sailing safely again.
The HVAC systems in cruise ships were never designed to deal with the air pressure (high pressure drop) required to push air through HEPA-level filters. As such, current HVAC systems cannot handle the HEPA filtration needed to capture viruses without burning out the air handling systems; to do so will require major costly upgrades.
This lack of a cost-effective solution is why many other organizations are recommending going from a MERV-8 to MERV-13, which current HVAC systems can handle. Unfortunately, MERV-13 is simply not an acceptable level of filtration to capture viruses needed to ensure cruise ships sail safely again.
Verdex has developed a functionalized antiviral nanofiber HEPA media (E12/H13) that can be retrofitted into existing mobile HVAC systems while keeping the same pressure drop. Verdex’s HEPA media filters 99.97% of viruses ensuring a safe and healthy cruise ship.
Unlike current HVAC media which lacks the ability to capture viruses/submicron particles, the patented Verdex process provides a 3D nanofiber media that combines high submicron particle capture efficiency with high air permeability.
Cruise ships can save billions in retrofit costs needed to upgrade HVAC to handle the required HEPA-level filtration. Verdex’s E12/H13 media lasts longer, resulting in fewer filter changes, lower replacement and labor costs, and less production downtime. With lower pressure drop due to depth loading of particles, the energy and compressed air costs are also dramatically lower.
Thomas Heininger is the director of engineering for Cabin Air Filters at Mann+Hummel. We posed the following question to him.
Q: For cabin air applications particulate efficiency (initially and over the lifecycle), energy consumption, and cost are all important. What role do you see for nanofibers in achieving these goals?
A: The nanofiber filter media produced by Mann+Hummel consists of a carrier media and an extremely thin layer of ultra-fine polymer fibers. This nanofiber-based filter media (fibers with an average fiber diameter of 100 nm) offers the best possibilities to cover all of the main aspects and therefore deliver the best possible air quality inside the vehicle. This fine fiber structure is effectively filtering out particles down to the ultra-fine particles (< 0,1 µm). As they mechanically filter out the particles, the performance stays stable over the filter life time.
Today the standard for cabin air filtration is the so-called electret-based filter media. They offer a good efficiency at the very beginning, but under the influence of temperature and humidity (which is a real challenge for the filter as being installed in the HVAC close to the evaporator), they will decrease in efficiency.
At Mann+Hummel we have developed nanofiber-based filter media for the mobile applications to overcome this issue and have proven the stable efficiency over lifetime in the lab, as well as in extensive field test campaigns. As we are taking about extremely fine fibers, also the resistance against the airflow passing through the filter structure is well balanced and optimized for the application in the vehicle´s HVAC systems where typically cabin air filters are installed. By constant development work over the years and process optimization nanofiber-based filter media also offer a good balance between performance and costs. All this yields the best cabin air quality, which is more important than ever as bad air quality and the proven negative health impacts linked to are becoming more evident. Therefore innovative filter media like this are the way forward in the goal to get clear air everywhere and for everyone.
Barry Kellar is the global vice president of Automotive Filters at Freudenberg, and he provided some added perspective on nanofiber for transport applications.
Q: How has the pandemic changed the cabin air market?
A: The cabin air market was already evolving to products with higher levels of efficiency, increased use of carbon-based media for adsorption of harmful gases, and introduction of more functionality such as anti-allergen benefits. The pandemic only increased the pace of acceptance, broadened the trend more globally, and placed higher emphasis on offering cabin occupants cleaner air due to consumer awareness of the health aspects of improved filtration.
Over the past several years, we have seen our OEM and HVAC Tier 1 customers discussing the concept of health and wellness more frequently, and the desire to highlight this more openly to the end users. The industry witnessed this firsthand when Tesla launched its model X vehicle, and showed the HEPA-like filter it installed in the car during its press launch.
Many OEMs are, or soon will be, introducing sensors into their cars that provide information on indoor air quality of the cabin. This shows they see the demand of their customers growing for healthier environments, and they wish to differentiate from competition with high-end filtration being one aspect.
Q: Where else do you see cabin air filtration gaining importance?
A: Other areas of mobility have also pushed to increase filtration within their offerings. One recent area is the bus market. The pandemic had a strong impact on mass transportation, whether buses, trains or ships, based on consumer health risk concerns when gathering in a confined space with many people. In order to address such concerns, and lower the risk to its users, bus manufacturers and owners are incorporating many new health devices to lower the risk of contamination. We have bus customers in each major region working with Freudenberg to provide much higher filtration performance. I believe other mass transportation will soon follow, whether it is trains or cruise ships. All these areas know that without demonstrating people can travel safely, the return of customers using such transportation modes will be slower.
Q: What about the use of nanofibers or other technologies for cabin air filtration?
A: Currently the main technology used in cabin air filtration incorporates electrostatic technology in the nonwoven media. It allows for high collection efficiency of particles, while maintaining a low pressure performance, which is desirable by OEMs. But with the demand for even higher levels of performance, combined with installation of IAQ sensors, incorporation of nanofiber and membrane technology is increasing. While electrostatic media technology will not simply go away, combining this technology with a membrane or nanofiber layer in a composite structure will increase in use.
While not all electrostatic technology is the same, and Freudenberg technologies are quite robust, discharge does occur over time. While the build-up of the dust cake on the upstream side of the filter assists in balancing out the efficiency as the filter discharges, for products that wish to maintain HEPA-like levels of performance through the life of the filter, adding a layer of membrane or nanofiber media makes sense. Of course, the trade off in using more mechanical media is higher levels of pressure drop, if OEM customers can increase the size of the cabin air filter, usually the pressure drop differential is not too much.
Overall, the cabin air filter market is attractive, and the use of high-performance filtration is increasing in both cars and other mobility applications. There are still many challenges ahead for the industry, but working with our OEM customers and innovating together will enable us to overcome these challenges successfully.
Additional interviews and discussions on this subject will be published online and linked to this article. If you have information to contribute, contact Bob McIlvaine at rmcilvaine@mcilvainecompany.com.