Founded in 1959 by Lambert (Bud) H. Mott, Mott Corporation provides custom-designed filtration and flow control products for applications that require precise outcomes.
Mott’s Customer Innovation Center (CIC) provides design and development engineering resources, as well as full lab testing capabilities. Lab testing services include SEM/EDS analysis, cleanliness testing, filter feasibility testing, porous media characterization, failure analysis, lifecycle testing, mechanical properties testing, and computational fluid dynamics analysis.
Mott works primarily with sintered porous metals in the design of its filtration media, but also produces polymeric, ceramic and other metal products utilizing additive manufacturing. Mott also offers coatings to increase corrosion resistance, improve durability and filter performance.
Mott’s filtration and flow control products are used in semiconductor, medical, chemical, aerospace, clean energy, refining, food & beverage and the bioprocessing industries. These products can range from filter elements mounted in skids several stories tall to porous flow plugs so small the eye can barely see.
Mott is a 100% employee-owned company. It has two manufacturing facilities in Farmington, Connecticut, and maintains Class 100 and Class 10,000 cleanrooms for customers with strict cleanliness requirements. The company is ISO 9001 Certified and has a worldwide sales network.
In this edition of IFN, we interview Mr. Boris Levin, president & CEO at Mott Corporation.
Ed Gregor: Mott supplies to many markets. What do you see as the greatest growth areas?
Boris Levin: Mott does indeed supply to many markets. Our ability to customize filtration and flow control products to customer specifications allows us this diversity. We have seen a great deal of growth in the Life Science market through the advent of COVID-19 relating to components in the diagnostics area, as well as customer collaborations solving issues in biotherapeutics. Of course, another current growth area is the semiconductor industry. Our products are in heavy demand as new wafer fabs are under construction at an all-time record pace. Mott has a well-established product and service reputation with fab facilities, integrators, tool makers, gas suppliers and a distribution network worldwide which makes this a significant growth area.
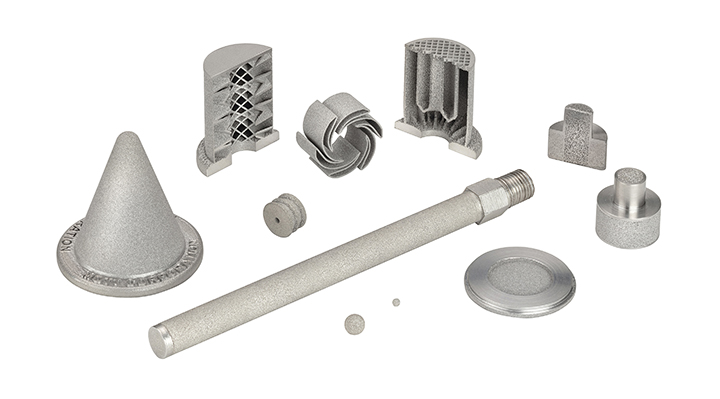
Ed Gregor: What pore range can you provide in these areas?
Boris Levin: Mott typically provides filter pores in the range of 0.1 to 100 microns, but we excel at pushing the boundaries on these limits with custom innovations. In our innovation center located here in Farmington, Connecticut, we can use a customer’s own sample fluid to tailor the exact porosity needed for the optimal result, a process we call Filter Feasibility Testing. This process of honing a solution exactly to the application at hand is at the core of what we do here at Mott.
Ed Gregor: Are there any products or variations you would like the company to pursue in the future?
Boris Levin: Mott prides itself in offering custom-designed engineered solutions to the world’s most technically advanced companies. We will always remain at the cutting edge of filtration requirements, focusing on extreme environments, exotic alloys, new materials like polymer or ceramic or new manufacturing methods like 3D printing. As we grow, our customers continue to seek more encompassing solutions from Mott where we might provide an adjacent product in the same process given our quality and speed to deliver.
Ed Gregor: What are some of the unique products you make that you would like to mention?
Boris Levin: Mott makes ultra-high purity filters and filter systems that can capture particles as small as 1.5 nm to 9-log retention – the best in the industry. There are few places in the world – or even the solar system – that our filters haven’t been. Another area where we are unique is our product range; we make filters that range from extremely small – almost invisible to the naked eye – to products that are the size of three-story buildings.
Ed Gregor: Can you give our readers an example of one or two areas that set Mott apart from competition regarding innovation and new technologies?
Boris Levin: We custom design to exact customer requirements and build these custom products faster than anyone in the industry. Often times we see our competitor offering an off-the-shelf product, which is great if that product works for your application.
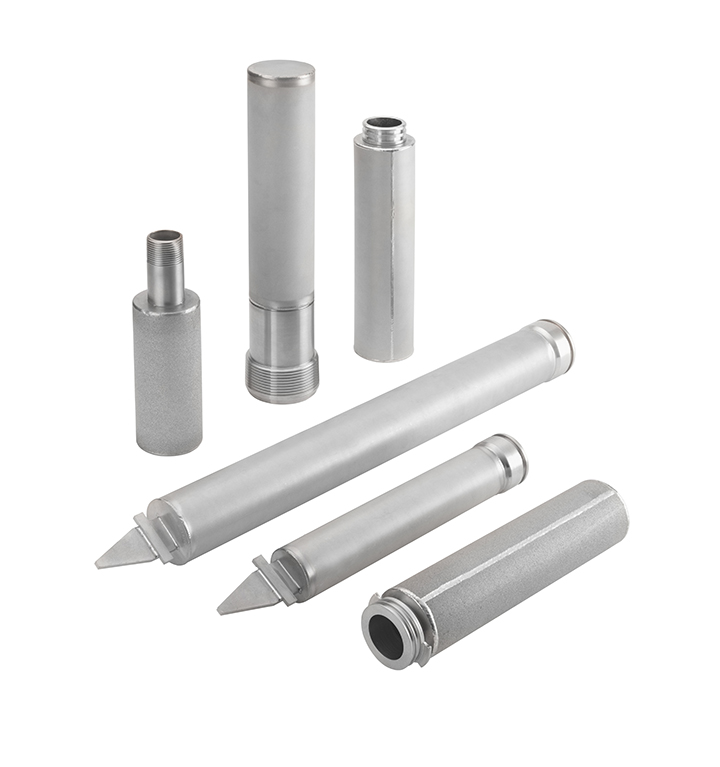
Ed Gregor: Where does innovation and new technologies rank at Mott?
Boris Levin: We have increased investments in innovation every year for the last 10 years. It is our first priority. Where we excel is developing next-generation solutions that, in most cases, aren’t within the capability of today’s products and often require investment in engineering and equipment. We’re committed to inspiring engineers to escape the ordinary – our company’s purpose – and we’ll establish partnerships to collaborate very closely to make a customer wildly successful in projects critical to their business.
Ed Gregor: Any examples you care to mention?
Boris Levin: Mott’s full skid filter systems are built on average twice as fast as competition and are turn-key, closed-loop, fully automated systems that give our customers decades of reliable performance. These filters are designed in ways that not only optimize performance but improve safety of their operators and can be proactively maintained utilizing predictive analytics.
Mott additively manufactures gradient porosity filters – a dynamic pore size from smaller to larger pores in a single component – for specific applications that would not be possible with conventional methods. These types of filters and products can integrate a large bill of materials into one component, eliminate unneeded weight and excess material, and reach flow to pressure drop combinations that weren’t previously possible.
Mott makes ultra-high purity filters and filter systems that can capture particles as small as 1.5 nm to 9-log retention – the best in the industry. There are few places in the world – or even the solar system – that our filters haven’t been.
Ed Gregor: Are there any industry trends you foresee in your industry going forward?
Boris Levin: We see trends for smaller, cleaner and smarter products. These trends fit our capabilities very well and often require very demanding new tolerances put on our products. We accept these challenges and are proactively solving for them.
Ed Gregor: Can you see either Mott or your industry outpacing GDP in the future?
Boris Levin: Absolutely. The demand of cleaner processes is only going to increase. Combined with our ability to expand to new applications, we see significant potential to grow alongside our customers.
For follow-up inquiries to this article, contact Patty Cruickshanks, sales and marketing services manager at pcruickshanks@mottcorp.com.