Accelerating Decarbonization with Metal-Organic Frameworks
Filtration and separation systems exploiting the special properties of metal-organic frameworks (MOFs) will have an important role to play in accelerating industrial decarbonization, according to a new report.
Carbon capture technologies, more efficient space cooling equipment and clean energy transitions are all cornerstones of achieving net zero by 2050 and technologies exploiting MOFs are emerging in each of these areas according to the report, Metal-Organic Frameworks (MOFs) 2024-2034: Market, Technology and Players, from Cambridge, UK-headquartered consultancy IDTechEx.
Carbon Capture
MOFs are materials composed of metal ions and organic ligands that form a three-dimensional structure with a high surface area and well-defined pore size and porosity. These properties make them ideal for gas storage and separation, including carbon capture.
According to technology analyst and author of the IDTechEx report, Dr. Shababa Selim, MOFs are increasingly being employed in point source carbon capture solutions targeting industries where emissions are hard to abate.
“Deploying carbon capture technologies is the key to addressing emissions from industries that are hard to decarbonize such as cement and steel manufacturing, supporting low-carbon hydrogen production and removing CO2 from the atmosphere,” he explains. “MOFs can function as highly selective filters that can rapidly adsorb CO2 in the presence of other gases, such as nitrogen and water vapor. The key advantage is that saturated filters can be regenerated within minutes using low-grade industrial heat or mature pressure swing processes, offering lower energy regeneration pathways compared to alternative processes.
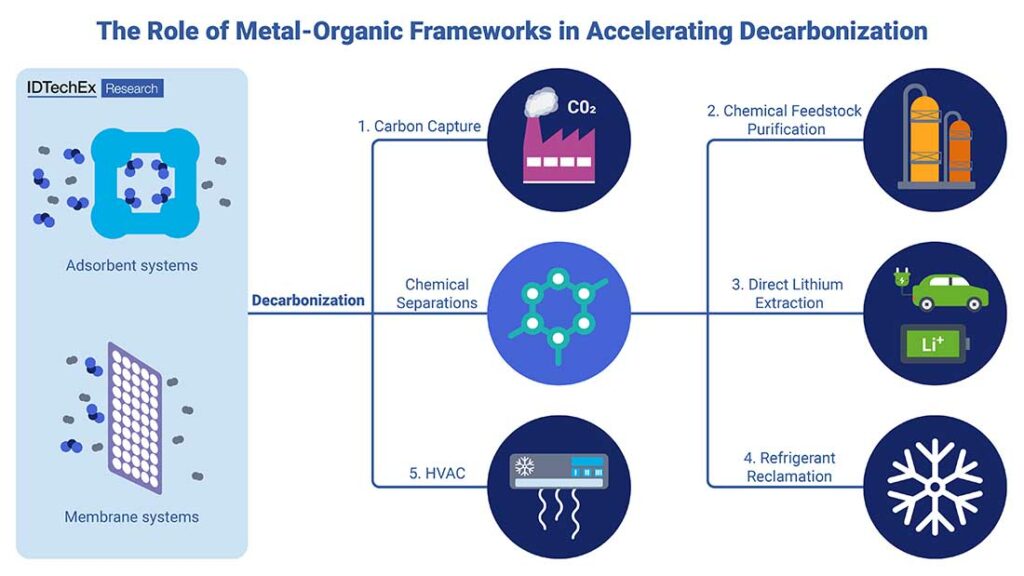
“While these technologies are currently operating at a substantially lower scale than the widely used amine scrubbing, there is the potential to rapidly scale up these modular technologies in the medium term.”
The key advantage is that saturated filters can be regenerated within minutes using low-grade industrial heat or mature pressure swing processes, offering lower energy regeneration pathways compared to alternative processes.
Mammoth
In addition to point source carbon capture, direct air capture (DAC) controversially proposes simply removing huge volumes of CO2 from the atmosphere and in May this year, the world’s largest DAC plant began operating in Iceland.
Mammoth is the second commercial DAC plant opened by Swiss company Climeworks in the country and is ten times bigger than its predecessor, Orca, which started running in 2021. The plant is designed for a nameplate capture capacity of up to 36,000 tons of CO2 per year once in full swing, by filtering it from the air and storing it permanently underground. The plant has successfully started to capture its first CO2, with twelve of its total 72 collector containers installed onsite.
Climeworks is partnering with Icelandic company Carbfix for this sequestration process and the entire operation will be powered by Iceland’s abundant, clean geothermal energy.
As previously reported in International Filtration News, in August 2023, the U.S. Department of Energy (DOE) also announced up to $1.2 billion in funding to advance the development of two commercial-scale DAC facilities in Louisiana and Texas.
Laminate Sheets
Companies actively involved in the development of MOF filtration systems include Vancouver-headquartered Svante, which has a collaboration and supply agreement with Climeworks.
Svante has developed a process for coating MOFs onto laminate sheets and stacking them into high-performance filters which are available for both industrial point-source capture – from hydrogen, cement, steel, aluminum, pulp and paper plants and refineries – as well as for direct air capture. Svante is now working with the major corporations 3M and BASF to significantly accelerate the commercialization of its filters.
Dry Impregnation
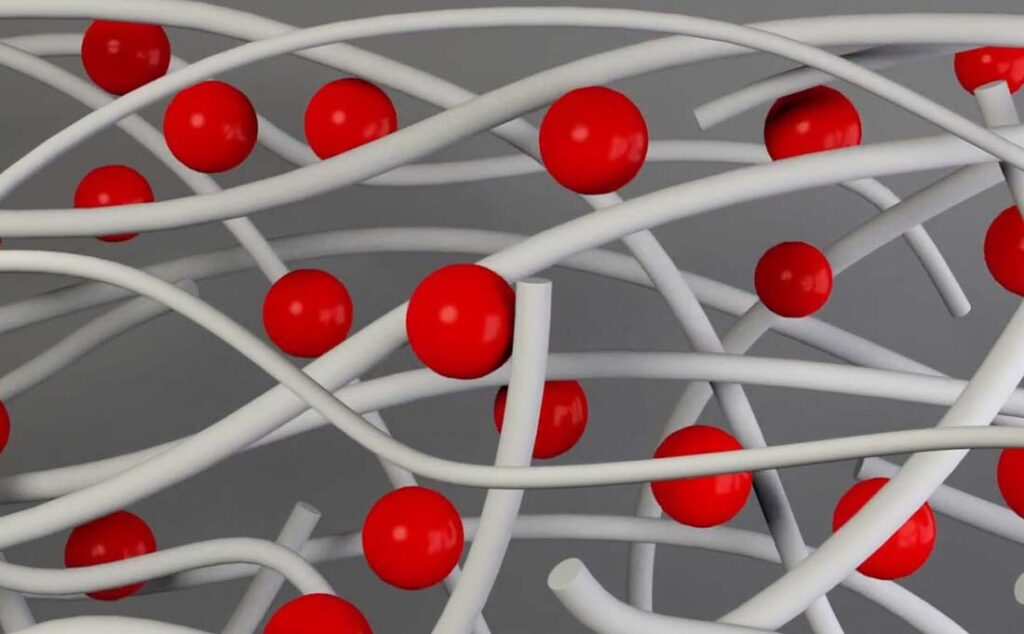
Fibroline, based in Lyon, France, has also recently established partnerships with a number of leading filter companies because its dry impregnation can be used with both thin and relatively thick filter media and many different powders can be incorporated to capture or extract specific molecules from air or liquids, including MOFs, as well as zeolites and ion exchange particles.
Fibroline’s patented dry impregnation technologies enable the homogenous impregnation of powders into porous structures by the use of high intensity alternating electric fields. This technology eliminates the need for water and solvents so there is no polluting liquid waste in processing or need for energy intensive drying.
The use of porous particles with controlled geometries enables targeted molecules to be trapped selectively and such small particles also increase the active filtration area, providing higher
adsorption capacity and faster adsorption and desorption.
In addition to carbon capture, promising results have been obtained in water treatment, including arsenic removal and ion extraction, as well as in air filtration.
Chemical Production
IDTechEx sees another major opportunity for MOFs in chemical separation and purification processes, to replace or supplement existing systems and reduce energy consumption.
Olefin/paraffin separation for propylene or ethylene purification, for example, is amongst the most energy-demanding of separation processes.
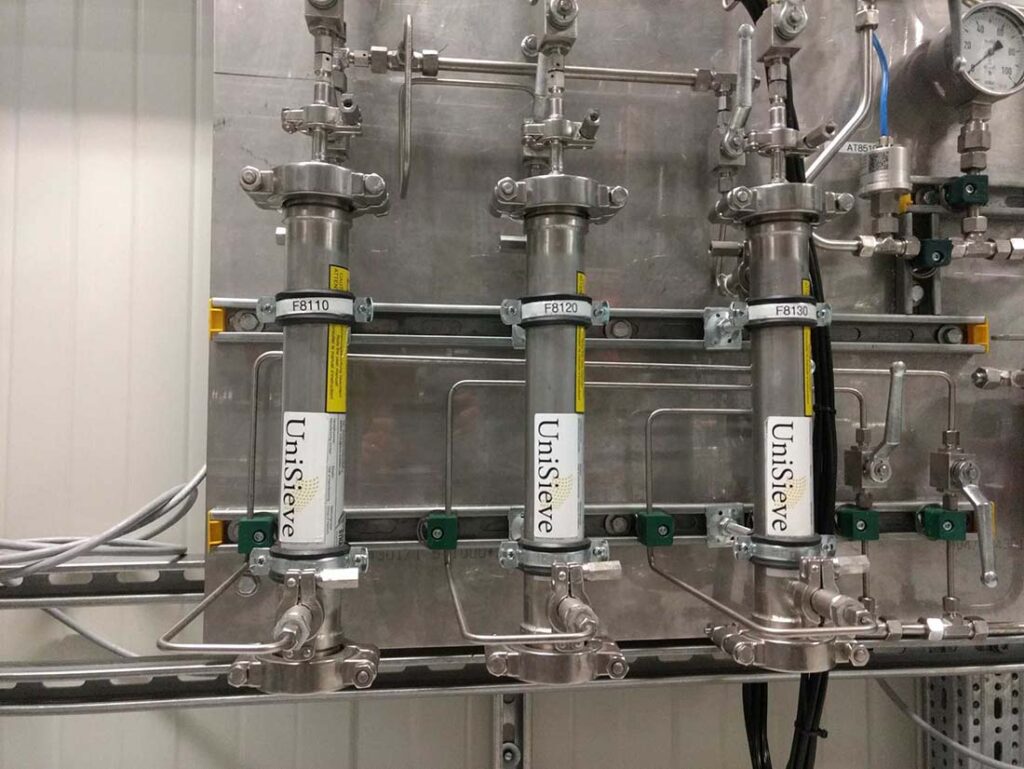
UniSieve, a Swiss-based cleantech company originating at ETH Zurich, has developed molecular separation membrane technology based on MOFs that can reduce the energy consumption associated with separation by around 90% compared to conventional distillation processes by increasing process-energy savings, maximizing product recovery and reducing process CO2 emissions.
The UniSieve membranes separate molecules based on a size-exclusion mechanism, without the need for thermal energy and are mechanically stable and flexible. They can be integrated into standard membrane cartridges and the platform technology allows for precise tuning of the membrane pore sizes, making the technology available for a broad range of challenging applications.
Precise Cut-Off
The UniSieve technology offers a uniquely precise molecular cut-off, to enhance the molecular sieving separation.
Compared to other membrane technologies, UniSieve membranes can efficiently separate molecules that vary only by a fraction of angstroms in diameter – such as propylene from propane. The smaller molecules permeate the membrane while the larger molecules get retained with the precise molecular membrane cut-off enabled by integrated crystalline molecular sieves.
In April 2023, UniSieve successfully closed an over-subscribed $5.5 million funding round with participation from a venture capital consortium including the Amadeus APEX Technology Fund, Wingman Ventures, Ciech Ventures and Zürcher Kantonalbank.
Direct Lithium Extraction
Vast quantities of critical minerals are necessary for clean energy technologies such as electric vehicle batteries and 60% of the total demand for lithium is currently from clean energy. This demand is set to grow to 90% by 2030 according to the International Energy Agency (IEA).
The demand for lithium is projected to be over 700,000 tons by 2030 and anticipated supply is expected to meet only 70% of this demand, according to IDTechEx.
“Rapid expansions and the diversification of robust and sustainable mineral supply chains are essential for continued growth and the ability to tailor MOFs to selectively separate chemicals can be leveraged for direct lithium extraction technologies, as an alternative to conventional lithium isolation methods,” says Selim.
EnergyX, headquartered in San Juan, Puerto Rico and Austin, Texas, has developed a proprietary modular lithium-ion transport and separation technology, which uses MOF-based membranes.
It is currently running pilot demonstrations of its technology across North and South America and has received investment from General Motors as part of a $50 million funding round closed in April 2023.
Refrigerants
A further promising field for MOF filters is in refrigerant reclamation.
Fluorocarbon refrigerants have a global warming potential that can be several thousand times greater than CO2 and as a result of recent legislation, the production of hydrofluorocarbon refrigerants needs to be reduced significantly by 2036.
In response, Osaka, Japan-headquartered refrigerant and HVAC equipment manufacturer Daikin is actively promoting refrigerant reclamation.
MOF-based separation technologies being developed in Japan are enabling the separation of fluorocarbon refrigerants with small differences in boiling points, which is not possible with conventional separation methods such as distillation.
HVAC Systems
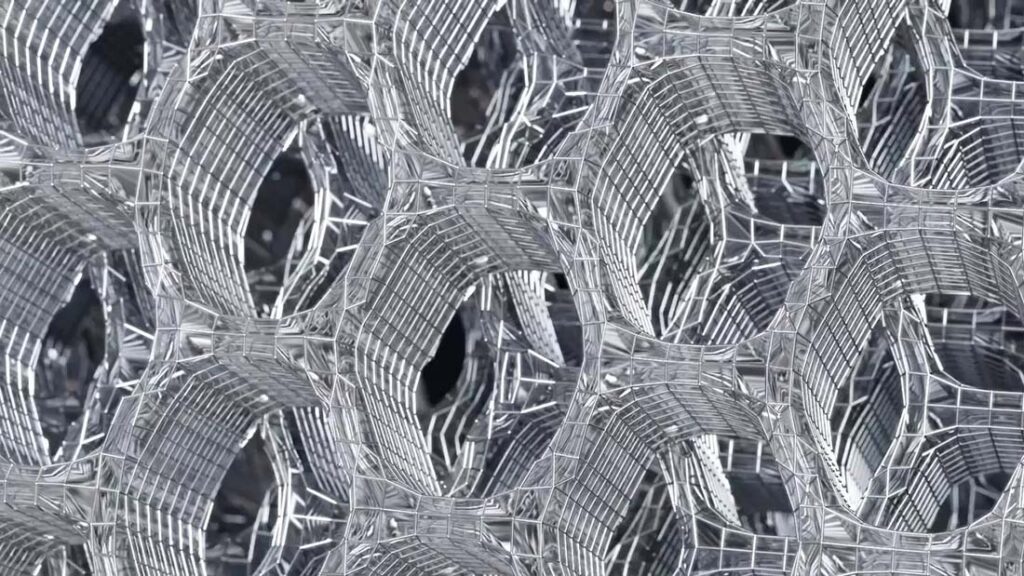
Finally, IDTechEx sees a significant role for MOF filters in HVAC systems, to tackle the high energy consumption associated with cooling indoor areas.
“According to the IEA, energy consumption associated with space cooling is set to more than double by 2050, with increasing demand for air conditioners in emerging markets and developing economies,” Selim observes. “To manage the strain on electricity generation and infrastructure, more energy-efficient air conditioning systems are needed.”
He cites the commercialization of AirJoule by Ronan, Montana-based Montana Technologies for integration into HVAC and atmospheric water harvester systems as a significant development.
AirJoule uses MOF-coated aluminum contactors and eliminates refrigerants to reduce electricity consumption by around 75% and Montana says it has solved the thermal constraints which have previously prevented the commercialization of MOFs in this application.
Using a proprietary MOF technology and coating system, the need for external heat to release water vapor during the desorption process is eliminated, which means that instead of using excess external heat AirJoule is able to harness heat from the absorption process. This both reduces the need for energy and allows the chambers to release the water vapor. Unlike conventional systems, AirJoule also eliminates the need for refrigerants and works in both humid and arid environments.
Montana has attracted substantial funding from partners including BASF and GE Vernova.
Strategic Investments Are Key
“MOFs can unlock the advent of the disruptive next-generation technologies that are essential for industrial decarbonization,” says Selim in conclusion. “However, there are several challenges with economically manufacturing MOFs for industrial applications and developing robust, scalable technologies that integrate these materials. Partnerships between MOF manufacturers with technology developers are essential, with strategic investments by industrial partners being key to bringing these technologies to market.”
The IDTechEx report provides an independent analysis of all of these trends and considers further applications for MOFs in several other early-stage technologies.
Further details: www.IDTechEx.com/MOFs