Lydall, Inc., headquartered in Manchester, Conn., has global manufacturing operations producing specialty engineered products for the thermal/acoustical and filtration/separation markets. The company’s Performance Materials business segment includes filtration media solutions for air, fluid power, and industrial applications, air and liquid life science applications, and thermal insulation solutions for building products, appliances, and energy and industrial markets. As the COVID-19 pandemic has taken hold and continues worldwide, Lydall has been particularly active in ramping up its filtration capacity.
In June, Lydall announced an investment in an additional fine fiber meltblown asset. The new production line enables Lydall – one of the few American manufacturers capable of producing high-quality fine fiber meltblown filtration media for N95, surgical and medical facemasks – to significantly increase its supply and help alleviate the shortage of meltblown materials, both in the U.S. and internationally.
The new asset complements Lydall’s existing global meltblown capacity and is estimated to supply the filtration media for one billion facemasks per year, almost a third of the 3.5 billion that the U.S. Department of Health and Human Services has projected as necessary to protect healthcare workers.
Later that same month, Lydall announced the signing of a $13.5 million contract award with the U.S. Department of Defense (DOD). The contract supports Lydall’s investment in U.S. meltblown production capacity and allowed them to invest in a second new production line. By May 2021, when both new lines are operational, Lydall will supply enough meltblown filtration media to support the monthly domestic production of 140 million N95 respirators or 540 million surgical masks, as well as high-performing air filtration media to improve air quality in indoor spaces.
We’re focused not only on serving the immediate need for high-efficiency filtration media caused by COVID-19, but also on addressing future viruses and other threats to indoor air quality. To that end, we have established a Filtration Center of Excellence at our facility in Rochester, New Hampshire that is dedicated to advancing filtration science and developing new applications for our filtration media.
In July, Lydall hosted a groundbreaking ceremony to celebrate a major expansion of its production facility in Rochester, New Hampshire. The ceremony marked the beginning of construction on Lydall’s Filtration Center of Excellence, where the company will develop new, high-performing and environmentally sustainable media for air and liquid filtration. The new facility will also house two new production lines in spport of the company’s increased production of fine fiber meltblown filtration media for N95 respirators, surgical masks and air filtration systems.
In September, Lydall also announced an investment in a new production line at its production facility in Saint-Rivalain, France, to create fine fiber meltblown filtration media for facemasks (FFP2, FFP3 and surgical masks) and high-efficiency air filtration systems. The line, expected to begin production in the second quarter of 2021, substantially increases the company’s capacity to supply the European market.
And later that same month, Lydall announced a partnership with XPRIZE, a nonprofit organization that uses global competitions to crowdsource solutions to some of the world’s biggest challenges. Lydall will supply fine fiber meltblown filtration media to the 25 qualified teams of XPRIZE’s Next-Gen Mask Challenge. Launched in July 2020, this four-month challenge invites young adults around the world to develop the next generation of surgical-grade consumer facemasks. In addition to sharing a one-million-dollar prize, the three winning teams will be connected to rapid manufacturing opportunities in the U.S. to bring their designs to life.
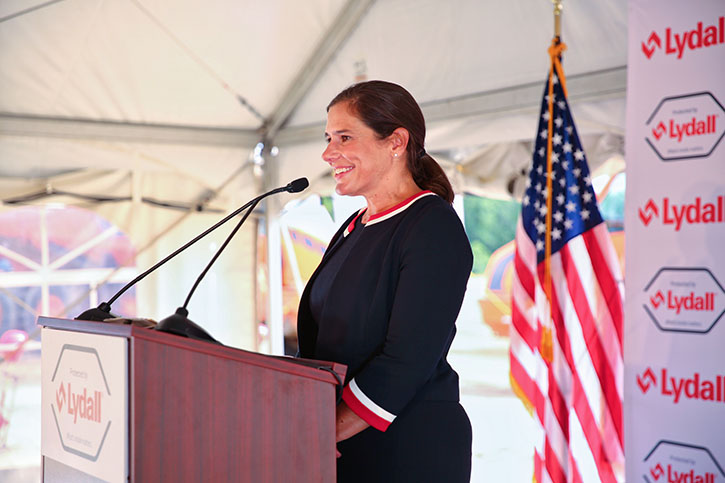
Along with the recent moves Lydall has made in its response to the needs of the COVID-19 pandemic, the company named Ashish Diwanji, Ph.D., as President of the Lydall Performance Materials business unit. Dr. Diwanji succeeds Paul A. Marold, who departed the company in June to pursue a new opportunity.
Prior to being named president of the Performance Materials business unit, Dr. Diwanji served as Lydall’s Senior Vice President, Innovation and Chief Technology Officer, focusing on advancing product-line rationalization and maximizing strategic technological development across the three business segments. Prior to joining Lydall, Dr. Diwanji led the product investment strategy and was the Chief Technology Officer for the Consumer Solutions division of U.S. Steel, and he also spent nearly 20 years at Owens Corning with his last role being the Vice President of Innovations for the company’s composites business.
International Filtration News interviewed Paul Marold in January 2019 to get a sense for Lydall Performance Materials’ strategic position within the filtration space. Much has changed since then, so we asked Dr. Diwanji if he would be interested in speaking with us about Lydall’s recent moves within the filtration space and the company’s long-term vision. He graciously accepted our invitation, and our discussion follows here.
Matt Migliore: Lydall is involved in a number of businesses beyond filtration, such as thermal acoustic insulation, sealing systems and technical nonwovens. How does filtration fit into Lydall’s business model and long-term strategy?
Ashish Diwanji: For nearly a century, Lydall has been a leader in specialty filtration solutions. Specialty filtration is an important part of Lydall’s legacy, and it is also a strategic cornerstone of our long-term growth and expansion. Today, we manufacture and sell microglass and meltblown filtration media products. To keep pace with COVID-19-related demand for our specialty filtration products – specifically, the fine fiber meltblown filtration media that is a critical component of N95 respirators, surgical masks and high-efficiency air filters – we have done everything within our capacity to maximize production, and we have made significant investments in this component of our business because we see a long-term need for these products. We expect the demand for facemasks will continue through 2021, and we anticipate a demand shift in a mix of filtration media as indoor air filters move toward higher MERV ratings.
We’re focused not only on serving the immediate need for high-efficiency filtration media caused by COVID-19, but also on addressing future viruses and other threats to indoor air quality. To that end, we have established a Filtration Center of Excellence at our facility in Rochester, New Hampshire that is dedicated to advancing filtration science and developing new applications for our filtration media.
Matt Migliore: Lydall has a number of business units involved in different aspects of filtration. What are Lydall’s filtration-related businesses, and how are each involved in filtration technology and applications?
Ashish Diwanji: Lydall Performance Materials is made of two segments – specialty filtration, which is legacy Lydall, and advanced sealing materials and parts, which is part of Lydall’s acquisition of Interface in 2018. Performance Materials offers a suite of air filtration media solutions – fine fiber meltblown filtration media, micro glass, cellulose and synthetic air filtration media – and also manufactures media for liquid filtration applications.
Technical Nonwovens, another business unit at Lydall, manufactures nonwoven filter media and filter bags for industrial applications.
Matt Migliore: As you mentioned, Lydall recently announced an investment in the construction of a Filtration Center of Excellence in Rochester, New Hampshire. What is the Filtration Center of Excellence, and how will it be leveraged as part of Lydall overall filtration commitment and strategy going forward?
Ashish Diwanji: Our Filtration Center of Excellence will be dedicated to the development of new, high-performing and environmentally sustainable media for air and liquid filtration by Lydall’s team of engineers and material scientists. It will also house two new production lines that will enable Lydall to dramatically increase production of meltblown filtration media for PPE and to serve our long-term customers for high-efficiency air filters.
Once construction is completed in May 2021, our Rochester, New Hampshire facility will be the largest site for the production of meltblown filtration media in the United States. With the addition of the two new production lines, we will supply enough filtration media for 1.7 billion N95 respirators or 6.5 billion surgical masks per year.
Beyond meltblown filtration, our Rochester facility will be expanding its capability for making new products in liquid and gas-phase filtration. We will be launching new products for the gas phase and hydraulic, lube, diesel and transmission markets in 2021.
Matt Migliore: Lydall also recently invested in a fine fiber meltblown line in France. What is the intention of this investment, and what are the expected outcomes near and long term? What does this investment mean for Lydall’s position in the European market?
Ashish Diwanji: As with the two new production lines we are adding to our Rochester, New Hampshire facility, our investment in the new line for our Saint-Rivalain, France facility was supported in part by the French government. Once the new line is operational in the second quarter of 2021, Lydall will support EU production of 600 million FFP2/FFP3 respirators (the European equivalent of N95 respirators) or 2.2 billion surgical masks per year. The investment solidifies Lydall’s position as one of the world’s largest suppliers of meltblown filtration media.
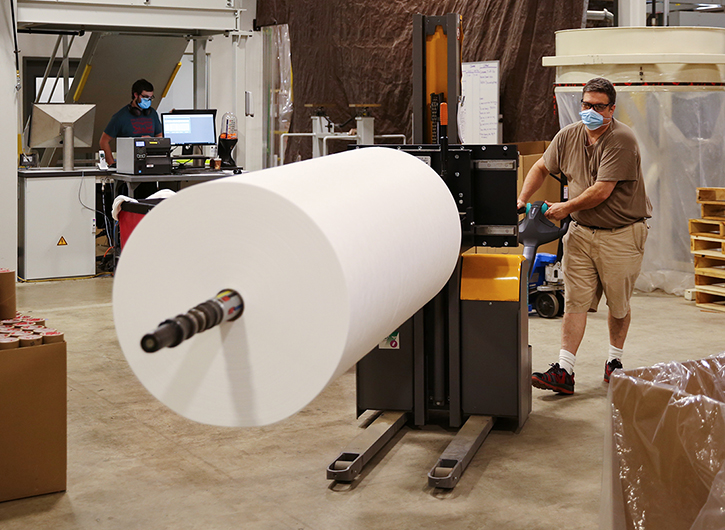
For more than 30 years, Lydall has manufactured medium- and high-efficiency filtration media at our Saint-Rivalain, France facility, which already has one line dedicated to meltblown production. Similar to the U.S., we see a long-term demand for N95 respirators, surgical masks and high-efficiency air filters in the European market. Even more critically, we believe that COVID-19 will have a long-lasting impact on the global supply chain, and that countries like the U.S. and France will continue to support domestic supply chains of products that are critical to national security and public health, such as PPE.
Matt Migliore: Lydall has been particularly active in the COVID-19 response – with the announcement of its Filtration Center of Excellence, adding meltblown capacity in Europe and signing a $14.5M contract with the U.S. Department of Defense to support facemask production in America, among its recent announcements. How has the COVID-19 pandemic impacted Lydall’s filtration business and areas of emphasis?
Ashish Diwanji: COVID-19 accelerated changes that were already in motion when it comes to reexamining indoor air quality. A number of environmental and societal factors have contributed to the need to higher-efficiency filtration for air quality applications, but COVID-19 created an immediate and urgent demand for these solutions.
The pandemic has forever changed how we think about the air we breathe, and even after things get back to “normal,” people are still going to want assurance that the air filtration systems in their homes, offices, schools and other public spaces are state-of-the-art and capable of protecting them from harmful particles. In response, we are partnering with many of our largest customers to co-develop the next generation of innovative filtration solutions to address new filtration standards for indoor air quality, globally. “Protecting places and spaces,” as our President & CEO, Sara Greenstein, puts it, is an important part of Lydall’s past, present and future.
Matt Migliore: How do you see the COVID-19 pandemic impacting the filtration industry and filtration technology development in the long term?
Ashish Diwanji: The pandemic has piqued consumer interest in high-efficiency air filtration systems, and products that previously had niche applications – for example, HEPA filters used in surgical suites and airplanes – are seeing demand for more widespread use. Even after the worst of COVID-19 is behind us, we expect this trend to continue.
We also believe that the localization of supply chains for PPE production will be a long-term effect of COVID-19. Over the past several decades, production of facemasks and other PPE had shifted overseas to China in pursuit of the lowest cost. Once COVID-19 hit, governments around the world were unable to secure an adequate supply of PPE to protect their first responders and healthcare workers. As a result, we believe that the U.S., France and many other countries will continue to prioritize the domestic production of PPE long after the pandemic is over so they will not be caught in that situation again.
Matt Migliore: Beyond COVID-19, what are the other application and/or technology areas related to filtration that you see as promising and/or particularly exciting.
Ashish Diwanji: Beyond applications related to COVID-19 and indoor air quality, there are two other areas of filtration science that I find particularly exciting. The first is liquid filtration for hydraulic, lube, diesel and transmission applications. Those include purifying and recycling water, making sure oil filters in cars effectively remove dirt and other particles, and cleaning liquids used in hydraulic systems such as large industrial equipment.
The other area where we are seeing a lot of growth is gas-phase filtration, or trapping particles to control and eliminate odors. Some examples of applications include filtering food odors in restaurant kitchens so it doesn’t reach patrons, and filtering smoke odors from an apartment so it doesn’t reach neighbors. Lydall is also working with high-end vehicle manufacturers to create carbon filters that eliminate odors from the road.
Matt Migliore: You recently stepped into the role of president of Lydall’s Performance Materials business segment. What attracted you to this role, and what do you find particularly exciting about it as you look toward the future?
Ashish Diwanji: I was fortunate to work with Sara Greenstein, Lydall’s President & CEO, for many years at U.S. Steel, and I was immediately drawn to her vision of Lydall: to be the global leader in specialty filtration and advanced materials solutions and to create a cleaner, safer and quieter world. I was also drawn to the opportunity at Lydall because it allows me to leverage my 18-plus years of advanced materials business experience at Owens Corning in glass fibers and nonwovens in a global environment.
What excites me most about Lydall’s future is our focus on innovation and our ability to partner with our customers and suppliers. We are creating some of the most critically needed products – not only today, but also for the years and decades to come.
Matt Migliore: We very much appreciate you taking the time to participate in this interview. Are there any parting thoughts and/or filtration-related topics you’d like to bring to the attention of the global filtration community before we wrap up? Anything I may not have touched upon in the interview?
Ashish Diwanji: Filtration has always been important, but never in our lifetimes has it been more critical to our health and safety. The filtration community has always done its best to create a cleaner, safer world, and the next phase of innovation will involve creating products that are connected to the information society we live in. That will require working with data scientists and leveraging technology like the Internet of Things, smartphones and sensors so people can make better-informed decisions about the air they breathe.
Just as there is an air quality index that measures pollution and irritants, imagine if there were an indoor air quality index that measured dust, mold, bacteria and virus particles. Imagine if the air filters in your home were equipped with sensors that told you exactly how effective they are at removing harmful particles. Imagine if the gas phase filter in your kitchen let you know just how many odor particles it is eliminating.
Beyond working with data scientists and others involved in the Internet of Things, we also need to make sure we’re empowering the next generation of innovators. That is why it is important for the filtration community to support vehicles like XPRIZE, which holds competitions to crowdsource solutions to some of the world’s biggest challenges. Lydall is proud to serve as a sponsor of the XPRIZE’s Next-Gen Mask Challenge, providing our meltblown filtration media to participants, as well as counsel and support from our team of engineers and material scientists.