As countries look to translate the recent global plastics treaty negotiations into action, it is vital that governments consider optimal pathways to advancing circularity through a combination of reduction, re-use and recycling strategies. Chemical recycling through pyrolysis (often referred to as ‘advanced recycling’) has emerged as an important piece of the puzzle, serving as a powerful complement to mechanical recycling due to its great versatility in processing different types of plastic waste.
There are, however, numerous technical hurdles associated with the pyrolysis process, particularly when it comes to contamination. Numerous types of plastics and non-polymeric sources are combined in mixed plastic waste feedstocks. Those feedstocks contain coarse to fine particles (e.g. filler, flame retardants, etc.) and other materials which are detected in the oil downstream in the pyrolysis process (e.g. coke). Besides the particulate matter, a variety of additional contaminants such as organic gels, dissolved metals and dispersed liquids are found as a side product in pyrolysis oil. The complex mixture of those contaminants needs to be extracted from the oil.
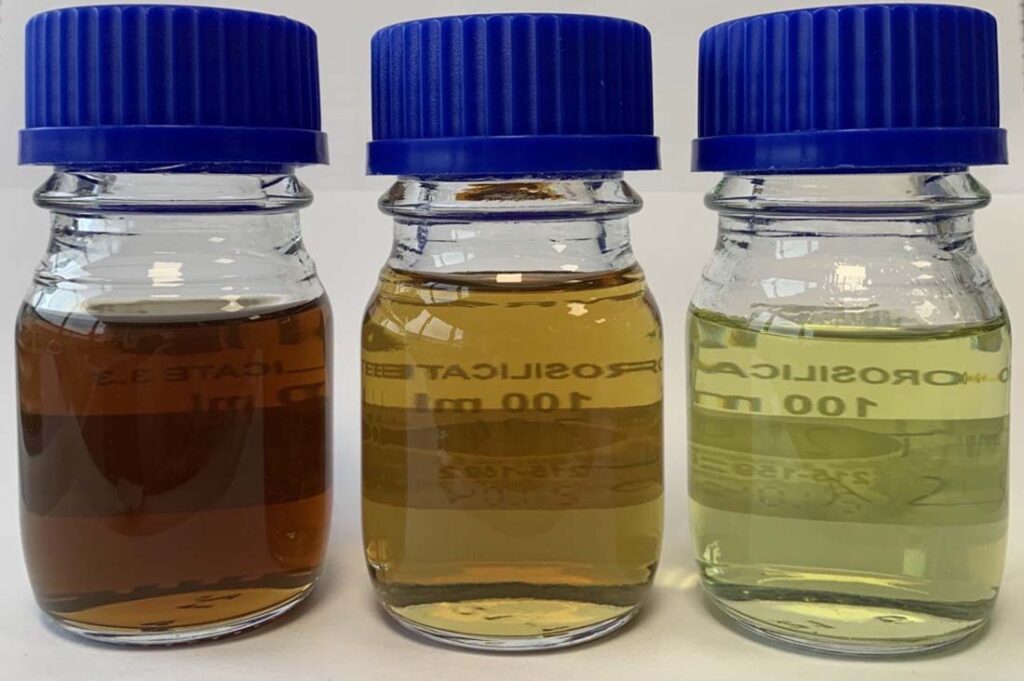
Appropriate filtration media and coalescer technologies are key at various stages of the process to remove particles and separate water from pyrolysis oil or liquids from gas. The retention and separation of contaminants not only purifies the oil and gas, making them more suitable for downstream processing, but also helps prevent equipment fouling and unnecessary maintenance downtime.
To further refine the pyrolysis oil for use as fuel or feedstock to produce plastic again, it must be transferred to a steam cracker to convert the oil into lighter olefins. The presence of particles and metal contaminants in crude plastic waste pyrolysis oils may have significant negative impacts on the steam cracker‘s furnace and recovery section such as furnace run-length reduction due to coking increase.
However, using depth filtration is an efficient and cost effective way to remove harmful contaminants and reduce the contamination levels of plastic waste pyrolysis oils to the thresholds accepted for crude naphtha feed in steam crackers.
It is imperative that international governments more strongly acknowledge the crucial role of chemical recycling in advancing the circularity of plastic production and reflect this through supportive policy measures and greater investment. This will allow the technology to scale up to a level that significantly enhances the circular economy and disincentivizes the production of virgin plastic from fossil fuels. We must use all the tools at our disposal to ensure a greener future.
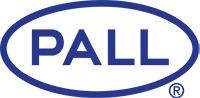