“When you can measure what you are speaking about, and express it in numbers, you know something about it, when you cannot express it in numbers, your knowledge is of a meager and unsatisfactory kind.”
Lord Kelvin
Measurement is the fundamental concept in the study of the sciences, engineering, and other technical fields. It is essential to almost all everyday activities, since in our daily life, we come across different measurement types for length, weight, times, etc. We can look at the measurement as the process of associating numbers with physical quantities as an activity intended to produce knowledge about the state of an experimental system. Measurement theory covers principles of how numbers are assigned to objects and phenomena, how different measures relate to each other, and the associated amount of error in the measurement process.
According to Eisenhart], measurement is defined as “the assignment of numbers [or values] to material things to represent the relations among them with respect to particular properties.” The process of assigning numbers results in an output that can be controlled using statistical techniques, and the value assigned is defined as the measurement value. Three fundamental concepts presented in his publication were immediately accepted:
- Measurement process requires statistical control.
- Statistical control implies a process which is repeatable and reproducible.
- Measurement values must include a statement on uncertainty.
Eisenhart’s work had a permanent effect on measurement processes at NIST and throughout the metrology community; it is widely accepted and utilized by standardization organizations.
The comprehensive process to obtain measurements, which can include the collection of instruments or gauges, standards, methods, fixtures, software, and personnel, resulting in the assignment of a number to the feature characteristic being measured is called the measurement system. Because the output of the measurement process is used in making decisions about the product and the manufacturing process, the quality of measurement data, which are commonly characterized by the bias and variance, are critical. The value of using data-based procedures is limited by the quality of the measurement data, which is related to the statistical properties of multiple measurements obtained from a measurement system.
Standardization
Standardization is as old as interactions within human communities and standards have existed since early historical times. The primary purpose of early standards was to bring human activities in line with natural occurrences; first standards were ways of measuring time and space. Time-unit standards were
employed by ice age hunters approximately 20,000 years ago, by carving lines in caves to keep a count of the days between different phases of the moon. King Henry I in 1120 AD created the preferred unit of measurement based on the length of his arm, which was called the “ell.”
Standards that exist in science, technology and manufacturing have a great impact on our lives since they prevent technological problems that could happen. Technical standards bring improvements to everyday life and solve problems that have advanced everything from manufacturing to public safety.
Wars have often forced standardization as Greek philosopher Heraclitus stated, “War is the father and king of all.” One example of standardization for military is interchangeable rifle parts, popularized in America when Eli Whitney used them to assemble muskets in the first years of the 19th century.
One of the examples related to the public safety is the Great Baltimore Fire of 1904, which burned for more than a day and destroyed 1,500 buildings. Fire companies from New York, Philadelphia, Wilmington, and Harrisburg came to Baltimore to combat the fire; however, most of their fire hoses could not be connected to the fire hydrants. With the lesson learned, the U.S. started many standardization projects.
One of the latest examples of standardization is the charging connector for electric vehicle. Standardizing the North American Charging Standard (NACS) connector will ensure that all manufacturers will
be able to install the NACS connector on electric vehicles and at charging stations.
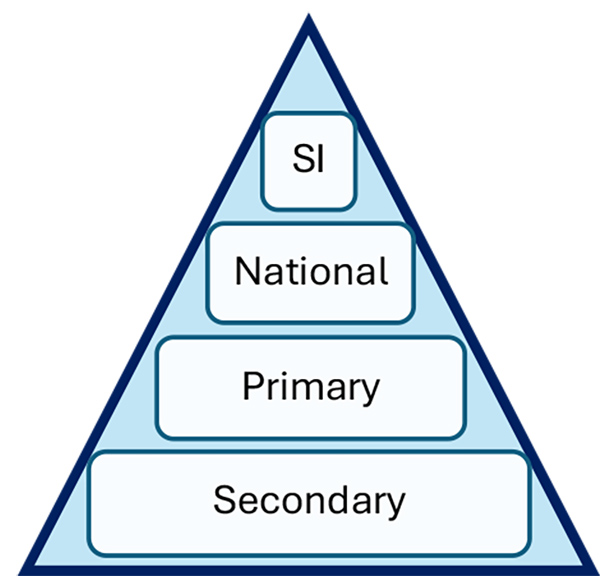
Based on the above examples, the specific meaning of the term “standard” can vary depending on context. It can refer to a unit of measurement, set of practices, specific part or a way of looking at the world. In general, standards assure that technology work properly since they:
- Provide basic terms to measure and evaluate performance.
- Make interchangeability of components made by different manufacturers possible; and,
- Protect consumers by ensuring safety and durability of products.
Major categories of standards include:
- Measurements standards: Fundamental reference for a system of weights and measures.
- Documentary standards: Test methods, sampling procedures, classifications, and others.
Examples of measurement standards include NIST – F1 and F3 atomic clocks, which serve as the basis for civilian time in the U.S.; and the Kibble balance, which is the basis for all mass measurements.
National Institute of Standards and Technology (NIST). The NIST was founded in 1901 and is the principal standard organization in the U.S. with responsibility of coordination its measurement standards with other countries, development and distribution of measurements and calibration procedures to other measurement systems. A calibration procedure is the process used to transfer the measurements with the intention of bringing the other measurement systems into agreement with measurements produced by NIST. This transfer process typically involves a hierarchical system of transfer; each level relies on its own system of standards.
There are several hierarchy levels of physical measurement standards:
- National standard: usually held by NIST.
- Primary standards: measurements are transferred to it by NIST using state-of-the-art calibration.
- Secondary standards: transferred by an organization with access to a primary standard.
- Working standards: used to calibrate the measurement systems at production facilities.
Measurements that are connected back to NIST through the proper calibration procedures are defined as traceable to NIST. Similarly, the Department of Defense defines traceability as “the ability to relate individual measurement to national standards or nationally accepted measurement systems through an unbroken chain of comparisons.” Traceability is an important concept since measurements which are traceable to the same standards will agree more closely than those that are not traceable. Traceability can have a positive impact on the reduction of re-testing and rejection or acceptance of products. Figure 1 shows the traceability pyramid; the higher location of the standard in the pyramid, the more accurate the standard (smaller measurement uncertainty).
As indicated, it is impossible to determine the accuracy of a measurement system without using traceable standards. Manufacturing and testing organizations which do not have their own metrology departments typically use services of outside organizations called “calibration labs.” Calibration labs are capable of establishing, under given conditions, the relationship between a specific measuring device and a traceable standard of known reference value and uncertainty.
Technical Standards
Technical standard is a specialized form of document which attempts to create a consistent and uniform practice among a specific community of practice. There are different ways in which organizations develop consensus around standards.
The method of developing standards and the formality of the process determine the type of standard. The two primary recognized types of standards are:
- De facto: widely accepted in practice by an industry and its customers, but not formally sanctioned.
- De jure: approved by an official standard organization and developed through a formal process.
Compliance with both types, de facto and de jure standards, is voluntary. However, there are some cases when the de jure standards are cited by legal codes or regulations, which could make it mandatory to follow. In some cases, a de facto standard can become a de jure standard if taken through a formal standard process.
What is a Standard? One of the best descriptions of a standard can be found on the website of the International Organization for Standardization (ISO). According to ISO, the ISO standards are internationally agreed by experts, and they represent the distilled wisdom of people with expertise in their subject matter and who know the needs of the organizations they represent. A standard is like a formula that describes the best way of doing something.
The ASTM International, formerly known as American Society for Testing and Materials, defines standard in a formal way as “a document that has been developed and established within the consensus process of the Society and that meets the approval requirements of ASTM procedures and regulations.”
ASTM publishes six different types of standards which include: (a) test method, (b) specification, (c) classification, (d) practice, (e) guide, and (f) terminology.
Standard Development. Standardization Includes a wide range of considerations – from the actual standard development to its publication, acceptance and implementation. The U.S. standardization system is a decentralized system that is partitioned into industrial sectors and supported by independent, private sector standards developing organizations. It is also a voluntary and demand driven system in which standards are developed and implemented by stakeholders in response to specific concerns and needs expressed by industry, and consumers.
In the U.S., the American National Standards Institute (ANSI) which was founded in 1918 is an organization that administers and coordinates the U.S. standards as well as a conformity assessment system. It approves standards as American National Standards (ANS) and is the U.S. national member body to the International Organization for Standardization (ISO), the International Electrotechnical Commission (IEC), and other organizations.
The International Organization for Standardization (ISO) is an independent, non-governmental international standard development organization composed of representatives from the national standard organizations of member countries. As of 2023, there are 167 members. The organization develops and publishes standards in technical and other fields.
A common misunderstanding about standardization is that, the publication of a standard is considered as success and the work is done. It is incorrectly believed that standard adoption and conformance will follow by itself.
As stated before, the voluntary system serves as the foundation of the U.S. standardization; standard development depends upon data collecting, discussion and agreement among diverse range of stakeholders. For these reasons, when developing a technical standard, it is critical to include a broad group of contributors in the process.
These contributors must be knowledgeable in order to develop a standard which reflects the current technologies and needs. In order to achieve optimal results, it is important to have a balance between specific contributor groups such as product manufacturers, end users, technical experts and standard experts. Despite having proper representation, it is possible that two groups look at the standardization outcome with a totally different assessment.
For example, specific manufacturers might feel that a proposed standard fails to fit with their products, while other manufacturers feel it fits well with their technology. Both groups have different opinions of a successful standard. The majority of contributors to the standard development want the standard to succeed; however, the understanding of success might differ between participants. A common misunderstanding about standardization is that the publication of a standard is considered as success and the work is done. It is incorrectly believed that standard adoption and conformance will follow by itself.
Another challenge associated with voluntary standard development is a potential collusion, when two or more technology manufacturers work together to push for a standard which benefits their technology.
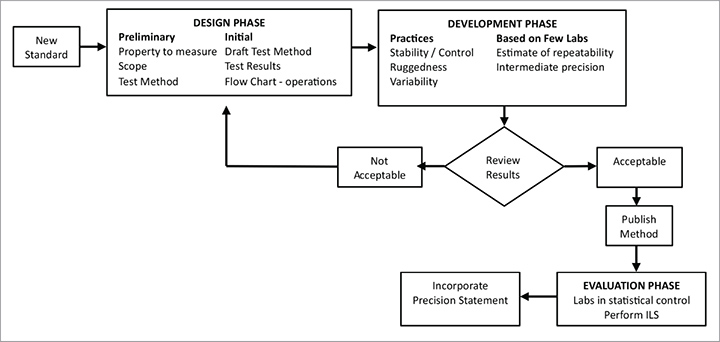
As noted before, the main goal of a technical standard is to unify specific practices (for example, test method) within a particular community. It is a challenge to develop a standard which satisfies all parties and recognizes different goals and priorities of the various contributors which is important when negotiating consensus on specific test methods and features.
In addition to the organizational part of standard development, the engineering and scientific efforts are equally critical for the creation of a successful standard. Rigorous engineering practices must be applied through all stages when developing new test methods.
New, standardized test methods should be validated for their intended purpose and application range. In the validation process the ultimate goal is to assure that the test method represents characteristics of the product with the required reproducibility and repeatability. The ASTM E 1488, Standard Guide for Statistical Procedures to Use in Developing and Applying Test Methods2 provides guidance how to develop estimated precision and bias statements. This standard recommends several specific phases during the development of a test method. Figure 2 shows some of the steps.
Four steps are recommended:
- Design phase
- Development phase
- Evaluation phase
- Monitoring phase
After the interlaboratory studies (ILS) are completed, the precision statements are included in the test method to provide specific estimates of variation anticipated when using the test method. The purpose of precision statements is to provide information on how close or far apart different test results may occur. The repeatability and reproducibility are the two measures of variability obtained for the test method. It should be noted that the ILS results can underestimate the measurement variability due to the well-known Hawthorne effect3. Blind measurements when operators do not know that an assessment is conducted could result in different (higher) variability.
Inclusion of precision statements is required by all ASTM test methods, and this recommendation is based on the Eisenhart1 study. Unfortunately, some standards related to the measurement of filtration efficiency, including ASHRAE and ISO standards, do not include the precision statements. These statements could have a significant impact on publication of test results, comparison and filter selection decision process.