The overall structure of the power industry is currently in transition – from one based primarily on a “hub-and-spoke” central generation model with one-way energy flows, to a hybrid system comprised of both distributed and centralized resources with two-way flows.
At the same time, new digital innovations are leading to a more efficient and autonomous grid, in which generation, transmission and distribution are optimized in real time.
In addition, in dealing with the climate change caused by CO2 and other emissions, the system is adapting to incorporate zero and low-carbon power sources and innovations that make traditional thermal sources more efficient and sustainable.
Tapestry
As a consequence, the emerging future electric grid will be one powered by a mix of generation sources – from wind and solar to gas, hydropower and nuclear – that will work in tandem across many different energy markets.
The leading suppliers of gas turbines such as GE (formerly General Electric), headquartered in Boston, and Siemens, of Munich, maintain that there will be no simple transition from fossil fuel sources of power generation to renewable ones, but a tapestry of combinations reflecting market realities and the marriage of old and new technologies, and gas-fired generation will play a crucial role.
This is backed up by the International Energy Agency (IEA), which predicts that natural gas, wind and solar photovoltaic (PV) will supply 70 percent of the additional electricity generated between now and 2040 in nearly equal shares.
By 2040, a total of 1,510 gigawatts (GW) of new capacity for gas-fired power plants will be needed, when factoring in the retirements of many existing plants.
“Gas-fired power plants are the only fossil fuel technology set to grow in almost all regions, thanks to the low upfront investment cost for new plants, the increasing availability of gas, and the role of gas in the flexibility of power systems,” the IEA asserts. “Only with a hybrid system made possible by gas can we build the power grid of the future while at the same time working towards decarbonization.”
While an individual will breathe in around 33 pounds of air each day, a 15MW gas turbine at the heart of a power plant will ingest some 4,700 tons in the same period.
Erosion, fouling and corrosion
While an individual will breathe in around 33 pounds of air each day, a 15MW gas turbine at the heart of a power plant will ingest some 4,700 tons in the same period.
If particles enter the machinery, they can cause erosion, fouling or corrosion of the interior parts of the turbine. This makes air inlet filtration systems essential to their operation and maintenance.
Erosion is a common problem because the turbine blades rotate at very high speeds and abrasion occurs when the blades come into contact with solid particles larger than five microns.
Fouling is encountered when contaminants in the air streams deposit on the blade, leading to a loss of efficiency. Particle sizes as small as 0.1 microns in the inlet air can trigger this.
Corrosion results from the chemical oxidation of metal parts and liquid droplets, as well as solid particles such as salts in the air stream, which enhance the reaction.
To avoid unnecessary damage to the machinery then, gas turbine filter media must meet the most stringent demands in respect of their burst strength, particle filtration efficiency and resiliency.
A range of media for this application are offered by several manufacturers including Ahlstrom-Munksjö, Hollingsworth & Vose, Lydall and Parker-Hannifin, for use in both the static and pulsed (self-cleaning) systems employed for protecting power plants, with filtration taking place at one or several stages with increasing levels of efficiency.
Three-layer structure
Ahlstrom-Munksjö’s Trinitex GT, for example, is characterized by a three-layer structure and each layer can be customized to deliver specific properties and an optimal combination of strength, mechanical particle removal efficiency, and pressure drop. The media is also easy to process on both rotary and knife pleating lines.
The company’s FineFiber GT meanwhile combines the advantages of cellulose synthetic media with fine fiber meltblown technology to enable excellent reverse-pulsing, as well as high dust holding properties for extended pulse cycles.
Ahlstrom-Munksjö’s Nano GT consists of a cellulose-synthetic media coated with electrospun nanofibers on the upstream side – a structure which results in accelerated reverse-pulsing behavior, as well as high mechanical efficiency at the lowest possible pressure drop. Nano GT can also be customized with value-added treatments such as fire retardants.
Fine fibers
Hollingsworth & Vose also has a broad range of media for gas turbine filtration and says that its patented Nanoweb media provides a 500 percent increase in service intervals for pulsed cartridge applications compared to non-fine fiber treated media. The media allows operators to fine-tune their filter change intervals to match other maintenance timelines.
Lydall Performance Materials views its proficiency in cellulosic, glass, ceramic, carbon, polymer and nanofibers as a key competitive advantage, along with expertise in engineering materials for extreme temperatures from –260 F to +3,000 F.
Among recent Lydall product introductions is HD ASHRAE, a wetlaid microglass media for the gas turbine market which is characterized by reduced flow resistance and energy consumption, along with the stiffness and strength to allow for improved pleating.
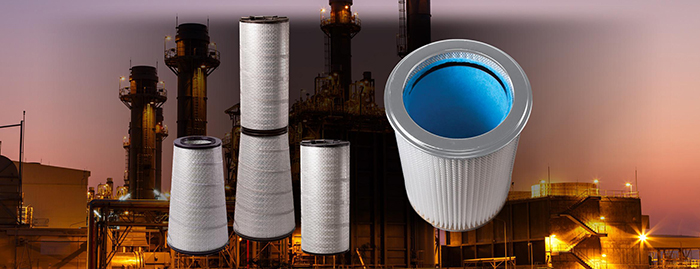
Membrane
Lydall’s Arioso high-performance air filtration composite media is also ideally suited for both pulsed and static applications and is fully resistant to oil and hydrocarbons while containing no fluoropolymers or halogens, allowing for incineration or recycling. Arioso media incorporate proprietary Solupor UHMWPE (ultra-high molecular weight polyethylene) membranes which deliver high-efficiency products with low resistance to air flow.
Engineered from a chemically inert and highly durable polymer, the Solupor membrane is laminated to a support layer to form a composite that is mechanically robust. Numerous functional support layers and/or pre-filter materials are available to tailor the composite structure to individual processing and application requirements.
H Class
In a significant development three years ago, Clarcor (which became a part of Parker-Hannifin at the start of 2017) announced a 10-year strategic arrangement with GE involving the supply of 100 percent of the requirements for filters and components for GE’s latest advanced technology H-class gas turbines and certain other gas turbine platforms.
This positioned Parker Filtration as the sole developer of the next-generation air inlet filtration systems for the H-class gas turbine, which is expected to become industry standard over the next few years.
Central to this development was Clarcor’s 2016 acquisition of FibeRio, the developer and manufacturer of Forcespinning nanofiber production systems, based in McAllen, Texas.
Prior to its acquisition, FibeRio had already delivered several large-scale industrial Forcespinning units and promoted the technology as allowing manufacturers to produce nanofibers on a commercial scale in a cost-effective manner, with the ability to spin a wide range of polymers, both from melts and from solutions.
Forcespinning technology is now enabling Parker Filtration to develop nanofibers and other media solutions with superior filtration capabilities at lower production costs than traditional media and supporting its development efforts for GE turbines.