While primarily associated with German engineering prowess, BMW is also, perhaps surprisingly, the largest automotive exporter of vehicles from the USA. BMW Manufacturing in Spartanburg, South Carolina, which is celebrating its 30th anniversary in 2024, assembles more than 1,500 vehicles per day, running on two shifts, and in 2023 exported cars with a value of $9.6 billion to 120 countries.
Robot Army
Central to the Spartanburg operation are its two paint shops, which employ 240 of the army of 2,600 highly efficient robots that are working alongside human co-workers at the plant.
These provide each car body with five coats of paint and two protective corrosion coatings in a process which takes 12 hours, during which time the vehicle has travelled a distance of around four miles. The entire process adds just 20 pounds of weight to the body – a thickness of 120 microns, which is the equivalent to the width of five human hairs.
Filtration systems in BMW’s automotive spray booths worldwide are crucial to ensuring high-quality surface finishes, as well as protecting worker health and maintaining environmental standards.
Designed to remove contaminants from the air within the booth, prevent dust, overspray and other particles from affecting the painting process, the technology behind these systems continues to evolve to meet ever more stringent industry requirements and environmental regulations.
Pre-Filters
Primarily based on glass or polyester media, pre-filters are the first line of defense in a spray booth filtration system, capturing larger particles such as dust and debris before the air enters the booth, in order to extend the life of the primary filters by preventing them from becoming clogged too easily.
At BMW’s plant in Leipzig, Germany, for example, specialists from Freudenberg Filtration Technologies – a long-time supplier to the auto maker – identified the greatest savings potential in the pre-filter area. Here, existing filter elements showed excessive pressure drop in comparison to their separation rate, resulting in a high level of energy consumption. These were replaced with Viledon WinAir 45 pocket filters designed for dealing with coarse dust at very low pressure drop. Test series and service life tests have subsequently demonstrated a noticeable increase in efficiency, enabling BMW to save 700 MWh a year, corresponding to a CO2 reduction of around 365 tons.
Overspray
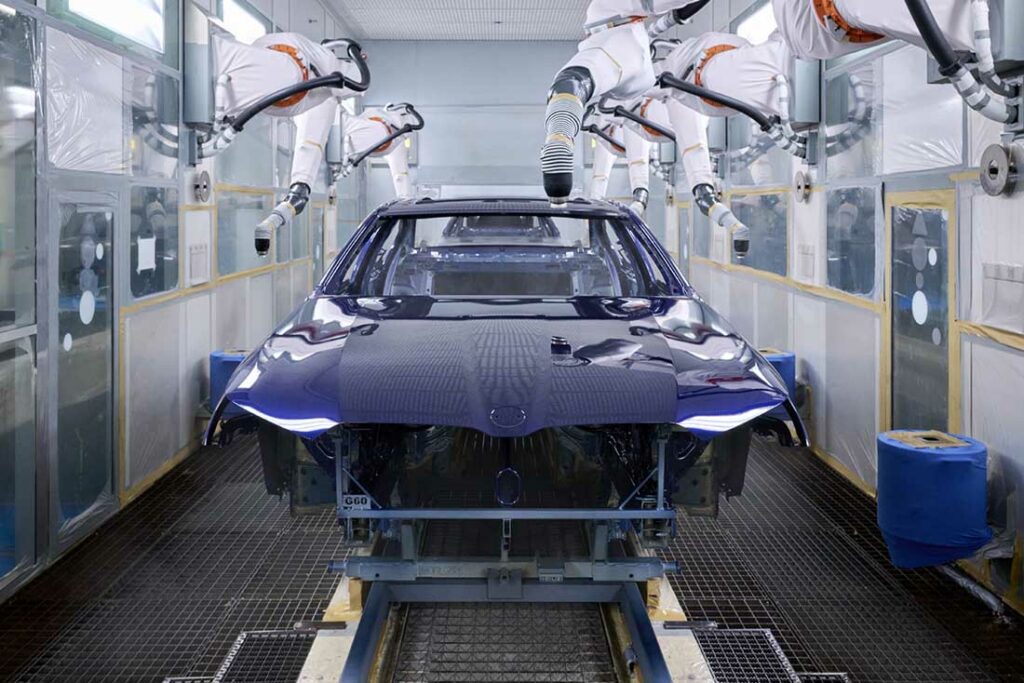
The primary filters in the airflow path within the spray booth are responsible for capturing paint overspray and critical to maintaining a clean painting environment. HEPA filters are often employed to capture finer particles.
Exhaust filters then capture any remaining contaminants before the air is expelled from the booth and help to ensure the air released into the environment meets regulatory standards for air quality. Activated carbon filters can be used at this stage to remove harmful volatile organic compounds (VOCs) and odors.
Dust Particle Analysis
However, even with state-of-the-art filtration technology, the content of the finest dust particles in spray booths varies depending on the ambient air drawn in.
If the dust content exceeds the threshold, the still wet paint can trap particles, visually impairing the painted surface.
BMW specialists have been involved in a project aimed at avoiding this at the company’s plant in Munich, Germany.
Each freshly painted car body at the Munich plant undergoes an automatic surface inspection in the paint shop and the data gathered in these inspections is being used to develop a comprehensive database for dust particle analysis.
AI algorithms have subsequently been employed to compare live data from dust particle sensors in the spray booths and dryers with the database.
“Data-based solutions help us secure and further extend our stringent quality requirements to the benefit of our customers,” explains Albin Dirndorfer, senior vice president of Painted Body, Finish and Surface at the BMW Group. “Smart data analytics and AI serve as key decision-making aids for our team when it comes to developing process improvements. We have filed for several patents relating to this new dust particle analysis technology,”
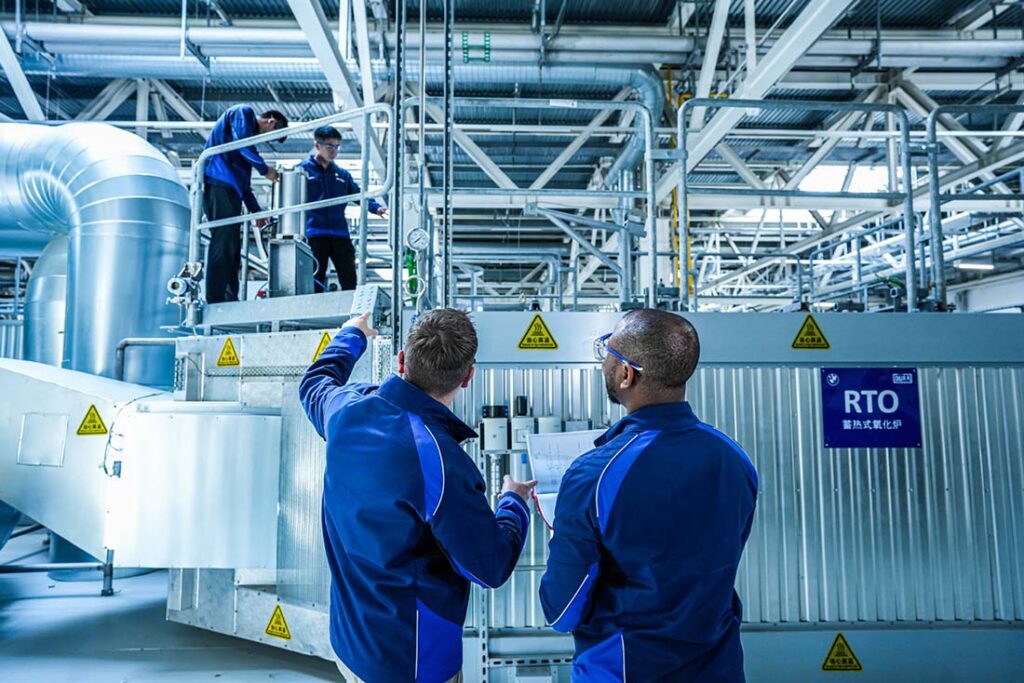
Patterns
The algorithm can detect, in good time, when dust levels are set to rise due to the season or during prolonged dry periods and is able to determine, for example, an earlier time for filter replacement. Additional patterns can be detected where the algorithm is used alongside other analytical tools.
The BMW specialists see enormous potential in dust particle analysis. Based on information from numerous sensors and data from surface inspections, the algorithm monitors over 160 features relating to the car body and is able to predict the quality of paint application very accurately. The AI solution will be suitable for application in series production when an even broader database for the algorithm has been developed.
In particular, this requires additional measuring points and even more precise sensor data for the car body cleaning stations. The AI experts are confident that once the pilot project in Munich has been completed, dust particle analysis will become standard practice at BMW’s plants worldwide.
Regenerative Energy
BMW is also now on the way to powering the paint shops across its global manufacturing plants with regenerative energy, due to a new method of achieving the high temperatures needed for the thermal purification of exhaust from its spray booths and drying areas.
Before being released into the atmosphere via chimneys, exhaust from spray booths and drying areas is purified to prevent paint shop solvents from harming the environment. This is done by passing it through a bed of ceramic media, where the solvent residues are burned off.
To do this, the air has to be heated up to very high temperatures of up to 1,800°F in a short space of time. The energy needed to do this could previously only be provided by natural gas, but the eRTO – electric regenerative thermal oxidation – system now makes it possible to purify exhaust with electricity from renewable sources.
The eRTO system is installed between the painting booth, drying process and chimney. Thermal energy is recovered by a flat, two-meter-deep ceramic bed which serves as a recuperator. Electrical heating rods heat the surrounding ceramics, and because most of the heat is retained, with only small amounts escaping, a connected load of just a few hundred kilowatts is sufficient to run the system.
The eRTO system was initially function-tested in ongoing paint shop operations at BMW’s plant in Regensburg, Germany, and is being further validated at the BMW Brilliance plant in China, where an eRTO system is used to purify exhaust from the drying system for car bonnets.
BMW is also now on the way to powering the paint shops across its global manufacturing plants with regenerative energy, due to a new method of achieving the high temperatures needed for the thermal purification of exhaust from its spray booths and drying areas.
The first European BMW Group facility to use the technology in series paint shop operations is at Dingolfing Germany, where one of four paint lines has already been converted for electric exhaust purification. More such systems are planned for the production network, and the new BMW plant in Debrecen, Hungary, will purify paint shop exhaust purely by eRTO.
Reverse Osmosis
Back in Spartanburg, a further recent development has been the installation of a high-pressure reverse osmosis unit for the two paint shops. This is enabling wastewater from the paint processes, which would normally be pretreated and discharged to the sewer, to be filtered and reused.
In 2023, this process reduced the Spartanburg plant’s water consumption by an impressive 15.9 million gallons.
The BMW Group announced in 2022 that it would invest $1.7 billion in its U.S. operations, including $1 billion to prepare the Spartanburg plant to assemble fully electric vehicles, along with $700 million to build a new high-voltage battery assembly plant in Woodruff, South Carolina.
“After 30 years of successful production, we are further expanding our commitment to South Carolina and in late 2026, the production of fully-electric sports activity vehicles will get underway here in Spartanburg – as a further step towards strengthening our global resilience,” said Milan Nedeljkovic, a member of BMW AG’s board, during an anniversary celebration at the plant this June.