In a world where sustainability and efficiency are paramount, the fish industry faces significant challenges. According to the World Wildlife Fund (WWF), over four billion people rely on fish and fish products as their primary source of protein. Additionally, the growing health consciousness among consumers has increased the demand for fish oils like omega-3, omega-6, and krill oil. By 2030, aquaculture (widely referred to as fish-farming) is expected to account for over 57% of food fish production, surpassing wild-caught fishing.
Increasing production volumes however is not a sustainable solution to meet growing demand. Instead, the industry must adopt climate-friendly approaches, such as ‘upcycling,’ to recover high-value nutrients from existing production ecosystems.
Upcycling
Upcycling involves processing byproducts or waste streams into high-value ingredients, such as proteins. Food manufacturers often hesitate to upcycle because of the high financial investment needed to repurpose what is traditionally viewed as waste or sometimes simply due to lack of knowledge on the possibilities. Therefore, it’s essential to find efficient, reliable, consistent, and cost-effective ways to extract as much high-quality protein as possible from these byproducts.
Sustainable solutions like membrane processing can help the industry recover high-quality fish protein hydrolysates, a highly premium ingredient used in aquaculture and other feed industries. Products such as Pall’s Membralox® ceramic membranes have been proven on a large scale to provide the most efficient protein transmission, separation, and extraction systems for producing high-value, safe, and functional upcycled protein ingredients.
These crossflow filtration systems are fully enclosed, automated, self-cleaning and operate at optimal temperatures to prevent thermal denaturation of the product. Their modular design allows any feed flow rate, continuous 24/7 operation, sequencing batch processes and the membranes’ lifetime extends over years of continuous operation with consistent separation performances and capacity.
Case Study: Pall Membralox® Ceramic Membrane Technology
The Challenge
Fish oil and fishmeal is produced by cooking fish meat and pressing it to separate the liquid. This generates two streams: fish oil and aqueous stick water. Stick water, so-called due to its sticky consistency, is recycled, and evaporated before being mixed with fish meal. However, stick water contains impurities like suspended solids and trace amounts of fat, which if not removed can lead to fouled pipes, fluid movement interruption, additional cleanings, and operational downtime. Traditional processing can also cause equipment scaling, higher energy costs, and larger waste discharge volumes.
The Solution
Pall offers a sustainable filtration solution using its Membralox ceramic membranes. Tangential Flow Filtration (TFF) or Crossflow Filtration (CFF) systems clean the fish stick water before evaporation to remove unwanted suspended solids and oils. This improves drying efficiency and produces a superior quality, more valuable final product.
The stick water, rich in proteins, is then further processed through membranes and evaporators to generate thick liquid fish hydrolysate (up to 80% protein) and dried hydrolysate powder (up to 85% protein), generating a considerable return on investment.
By adopting membrane filtration technologies, processors can upcycle fish byproducts into high-value protein hydrolysates, enhance profitability, sustainability, and product quality, and help meet the growing global demand for fish and fish products.
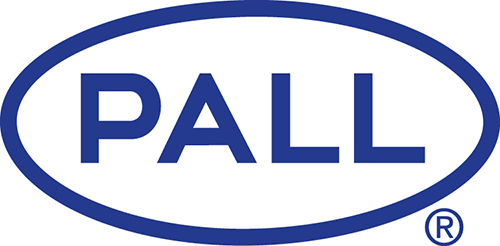