It All Depends on Your Expectations, in My Experience
When does it make sense to add automation to your process? Let’s dive in: In my 30 years of sales and machinery experience helping customers choose the right machine systems for their company needs, I have witnessed firsthand the power of automation on productivity, profits, employee well-being, corporate advancements, and more.
About 20 years ago, through the company I represented, we began to offer clients equipment with a FANUC robotic arm integrated into a gluing machine solution built for the filtration industry. It was the beginning of an era in equipment advancements, and a whole new conversation with clients on what these types of improvements will and won’t do for their business models.
I have walked decision-makers through all the objections, questions, and scenarios to help them make educated decisions. Frankly, most objections were due to myths they believed – and also,
justifying the cost that automation carries with it.
So, here is what I believe you need to know.
Getting Past Misperceptions
Let’s take a step back and talk about exactly what we mean by “automation.” If you Google “automation,” you’ll get a nice definition: The use of largely automatic equipment in a system of manufacturing or other production process. I like that; however, I don’t like the can-you-use-that-in-a-sentence example they include –“…unemployment due to the spread of automation.”
No, that’s not it! Your workforce is not at risk; in fact, they will greatly benefit from automation.
When implemented by a healthy growing company, automation re-tools the workforce, provides a safer more efficient workplace, and leads to better jobs – not fewer jobs.
In fact, misconceptions about robotics and automation performing the same tasks that human manufacturing workers perform is ingrained in our society. From the early days of modern industry to today, ideas are cultivated in books, film and television of what a world with automation could be. From the cyborg Tin Man introduced in L. Frank Baum’s The Wonderful Wizard of Oz, written in 1900, all the way to 1960s and ‘70s pop culture shows like The Jetsons, Lost in Space, and Star Trek®, to current entertainment brands like Avengers® and Transformers®, the lines are continually being blurred between humanity and machinery.
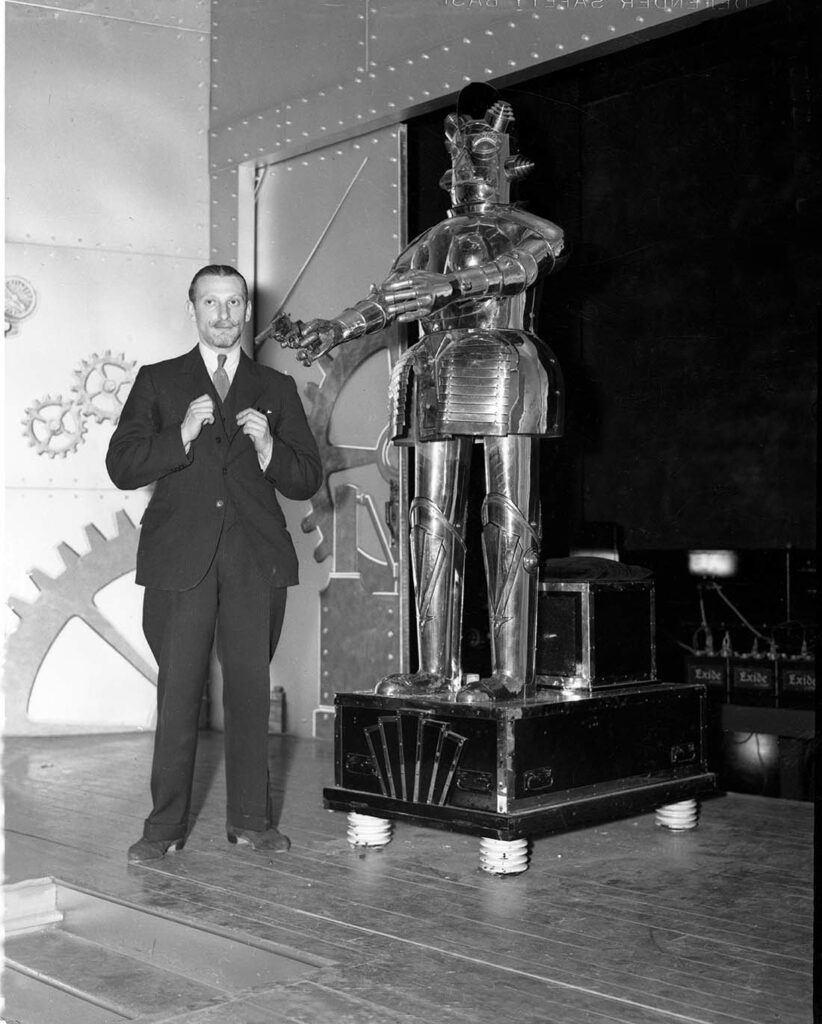
News stories of inventors of automation and their scientific quest to create human-like functioning “robots” also fueled the fires of misperception.
We see stories like Harry May, a professor in the UK, who built a robot he called “ALPHA” in 1932. His robot was designed to mimic human behavior, actions, and sort of appearance. May used a simple form of voice control to have ALPHA respond to his commands. Logically, one of the first things May taught
ALPHA to do was to aim and fire a revolver. Big surprise when one day, while May was setting up a demonstration for some dinner guests, ALPHA stood, aimed his revolver, and shot May in his outstretched, panicked, hand as he was preparing the real target.
I can only imagine the reception of that news as it spread and how that vision likely stuck in people’s minds for years after, as more refined engineering was being developed to better use such technology.
In 1939, another humanoid robot, “Elektro,” debuted at the World’s Fair. The seven feet tall, 265 pounds of steel gears covered by aluminum skin was able to perform tasks by voice command, such as walking and speaking (700 words). It could even smoke cigarettes, blow up balloons, and move its head and arms.
Those early images of robots with human features (like Rosie from the Jetsons) were ingrained for decades in the minds of people, and also prompted the fear of robots replacing people.
But, now we know better! Today’s fears revolve around artificial intelligence (AI) taking over our lives and workplaces. Yet, I believe there are benefits and uses for automating tasks that we previously relied on human labor to accomplish, not as a replacement of people, but an enhancement of people’s time spent on more productive efforts.
To Automate or Not to Automate Is the Question
Is automation for everything and everyone? No. There are and always will be things done better with a human touch.
While automation will work to get most callers to their proper contact when calling a company, there is no replacement for the personal interaction of a friendly human being that answers the phone. (Just think back to a time when you repeatedly yelled “representative” at an automated service. Hey, it happens!)
Just because we can automate, doesn’t always mean we should. Artists and craftsmen still get my vote when I am looking for that special gift or souvenir, rather than a mass-produced trinket. I’d still rather watch grainy footage of Elvis Presley, the King of Rock and Roll, over new AI-generated updates. Craftsmanship is of high value, with all of its perfect imperfections.
Craftmanship brands are built on the personal touch and are priced accordingly. Carmaker Lamborghini has a price tag that reflects 100% customization and hand-crafted interiors, assembled in one factory in Italy, producing 10,000 vehicles a year. Yet it still manages to make around $2.5 billion U.S. dollars a year. Rolex is another, selling one million watches per year with sales $11.5 billion U.S. dollars, where machines are operated by humans, and key parts are assembled by hand.
For most manufacturer brands, artisanship is not a factor – quality is, and automation can help with that. Automation has a wide reach. It can be applied across numerous industries, markets, and jobs.
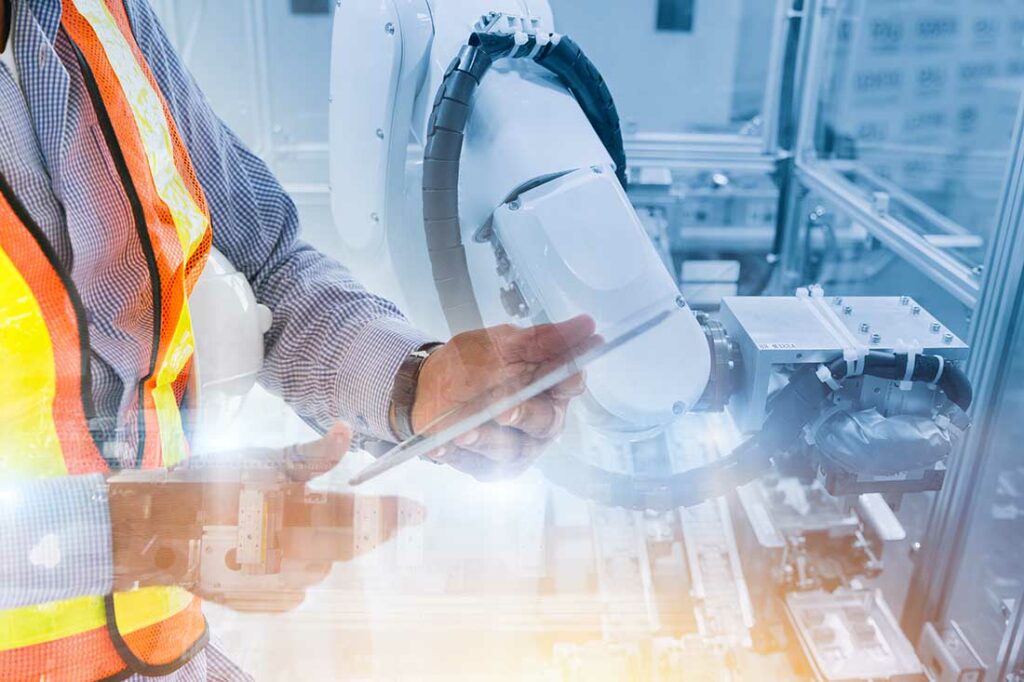
For example, I was recently reading Convenience Store News and came across an article on automation. Although the applications are widely different, the goals were much the same as we see in the manufacturing sector – increased efficiency and production, cost reduction, improved accuracy and timeliness, enhanced safety and security. To note, there was no mention of replacing people in that article.
In searching for a good example of automation that had negative impacts on quality, I was hard-pressed to find some. So how do we choose what to automate, and what to use labor to accomplish? Each company must do their own homework to choose the best manufacturing practices with impact to the bottom line.
We can look to the principles of LEAN manufacturing to get us most of the way there – safety, quality, delivery, and cost, just like our friends in the convenience store business.
In making a case for automation, safety is probably the easiest to justify. OSHA does a great job of outlining what we can and cannot have people do. We should ask ourselves:
- Where our workers are getting injured and why.
- What environments are we requiring them to work in?
- Are there distractions that keep them from focusing on the task at hand?
- Are they getting bored and/or careless?
- Are there repetitive motion impacts and injuries?
These are the considerations that plant managers can easily identify and begin to consider automation options.
A Case Study
I was visiting with a medical disposables customer who was rolling undercast padding, the soft cotton material that a doctor wraps around your broken arm before applying the cast. They had a process that remained the same for decades. It became quite routine, but the machine they used was starting to wear out. As we looked at replacing the machine, we saw that improvements could be had.
We looked at how involved the operators were in the process. Although technically they were using an automated piece of equipment, the actions were so labor intensive that the operators had to rotate tasks every half hour to prevent fatigue.
The machine would wind the cotton onto ½” diameter rods. The operator had to pull the full rod out of the machine and place it into a strip-off unit that pulled the rolls off and onto a conveyor.
They had to manually keep track of how many rolls they were making and place the rod in the proper position to stack up the finished rolls.
I visited again after the machine was installed, and I thought they were going to hug me. No one lost their jobs. Efficiency improved. Each worker was now staying at their position for the full shift. They now had time to conduct quality control testing of the finished products – carefully and not skipping details.
They were using a squirt bottle to lubricate rods. They actually just hosed down the area and the rods ‘just happened’ to get lubricated in the process.
Our engineering team built them a machine that automated all interaction with the winding rod, automatically lubricated each one, precisely stacked the finished products, and made life a whole lot easier.
Addressing employee concerns, I could see the worry on the operators’ faces when our engineering teams were studying their efforts. They were proud of what they were doing, moreover they wanted the job security to keep on doing it. I visited again after the machine was installed, and I thought they were going to hug me. No one lost their jobs. Efficiency improved. Each worker was now staying at their position for the full shift. They now had time to conduct quality control testing of the finished products – carefully and not skipping details. The area was clean, and the company began to look downstream to make additional improvements.
This illustration shows the impact of solving the most significant problem, in this case safety, and gaining other many other benefits in the process.
Trickle Down Effect of Automation
In the case study, quality did improve, but it was not the focus. Quality can come from the repeatability that automation can offer. When we get tired, we get sloppy. When our back hurts, our performance suffers. When we cannot focus, quality drops off.
A survey by the National Safety Council finds that 90% of U.S. employers have been impacted by exhausted employees. Half of the respondents’ report catching someone sleeping on the job. Ninety percent say they will meet with the affected employee to try to understand the root cause of their fatigue, but only 55% say they would be willing to adjust the employees work schedule as a result.
Furthermore, a Forbes article defines a condition called “boreout” – chronic boredom at work. Studies show that being bored at your job can cause depression, anxiety, stress, insomnia, and higher turnover. A Korn Ferry survey claims that boredom is the top reason why people leave their jobs.
Consider the placement of glue lines in a spiral wound reverse osmosis element. For those not familiar, a spiral element contains a number of “leaves.” Each leaf uses a u-shaped bead of glue to create the active filtration area. Typically, an operator uses a manual glue applicator, not unlike a pneumatic caulk gun, to apply or draw the glue path onto each sheet. Those sheets are then combined with a permeate carrier and rolled into a spiral element. The effectiveness of the finished element relies very much on the placement of that glue path.
Imagine spending your eight-hour work shift leaning over a table and drawing glue paths over and over, hundreds of times per day. I’ll bet that first line is fantastic – straight lines, perfectly placed, in the making an exceptional element. However, I bet that last line – the one right before heading for the door, one last element to hit your goal for the shift – doesn’t need those little lines on the tape measure to check deviation.
In the beginning of this article, I mentioned that the first robotic arm integration we implemented worked with a filtration application. We used a FANUC robotic arm to apply the glue lines onto membranes. Not only does that robot place the line precisely where we tell it, the precision doesn’t waver. It improved the operator’s work life by eliminating repetitive motions, thereby fatigue and boredom stressors.
Also, the throughput increased, and more significantly, increased the effective area of the finished element. Consistent, quality results provide the company sales team more confidence in products they sell, leading to more sales, and so on!
Production Improvements
How many companies lost production time during the COVID-19? How many are still worrying about sufficiently staffing each shift? The more we automate, the more we control production demands.
In a machine shop, you can stack boxes of work in front of a row of a manual milling machine, it will get done, with great precision. A skilled machinist will load each piece of raw material into the machine and craft it into a finished part. It will be manually checked against the drawing, and it will function properly to be installed on its intended machine.
Yet, this all requires the machinist to show up for his workday; not be interrupted with another request; and/or pick and choose the easier jobs first for the day.
By automating, not only are we putting the responsibility of quality onto the equipment, but we are streamlining spindle time and machine shop efficiency. We now have equipment capable of running “lights out” manufacturing. We feed it a list of jobs, make sure it has the proper tooling loaded, line up our raw materials, and away we go. We no longer need to have one man tied to one machine. We elevated machinists to be supervisors of our second and third shifts. They check on the automated cell, then tackle the next job on the list.
Productivity.com gives a nice explanation of automation versus delivery: We need to maximize the labor available to us.
Over the next three decades more than 76 million workers will retire with only 46 million new workers available to take their place. Your labor challenges are not going away!
Just In Time Hurdles
Automation provides the option for 24/7 productivity, “just in time” manufacturing, and more up time. Automation makes time for operators to perform secondary operations like gauging, washing, deburring, etc. It can include real-time factory communications. Equipping new machines with Ethernet connectivity allows you to send production data and communicate with other production equipment. Automation can provide quick changeover for multiple parts, tooling, etc., and flexible multi-operations capability.
Yet, we sometimes must “unlearn” some things. You have to be open to change old habits. You must work closely with your machine designers and builders to reduce bottlenecks in their process to improve quality, get cost out of commodity products, and improve employee satisfaction.
Find partners in this process that seek to collaborate with you and appreciate being involved from the start of a process review. They should be working not only the top-level management, but also considering the needs of the front-line employees who must operate the equipment daily.
Elephant in the Room
The biggest hurdle is often cost.
As a career salesman, I’ve tackled the “how much” question sometimes just to get in the door of a potential customer. However, when we talk about the cost of automation, we have to make sure we don’t have our blinders on. Total system cost is important and must make financial sense, but other cost factors of lost opportunity, lost productivity, lost time, and lost employees should be added into the equation.
On the plus side, make sure to calculate the new corporate opportunities and employee/workplace benefits that new automation can trigger. The financial or accounting team must consider the long-term gains, as well as the quick ROI calculations.
Here is a notable scenario: Consider investing in machinery versus securities. An example from Investopedia.com illustrates a business with $20,000 of available funds.
In deciding to invest or purchase of a new machine, whichever they choose the potential profit from the other is called “opportunity cost.” In the example, investing the money would return 10% per year. At the end of the first year, they will gain $2,000. At the end of the second year, $2,200 and $2,420 in year three.
On the other hand, if they purchase a new machine, the company will be able to increase the number of products they sell. The first year will include training, installation costs, and require time before maximum efficiency is achieved. At the end of the year, they may only see a $500 gain in profit. They will begin to hit their stride and gain $2,000 the second year, then the increased sales capacity will earn them an extra $5,000 in year three.
The point is, if we only look at a two-year plan, we are not seeing the full potential.
Proceed with Education
The key is to be educated and understand what your company is entering into. Automation has complex impacts and is not for every situation.
Here are some things to consider:
High initial investment. Careful planning and ROI calculations are needed with the considerations we discussed earlier.
Technological complexity. There are learning curves and challenges that come with new technology. Such as, now needing an IT person working the factory floor.
Job displacement. The goal should be to retrain or relocate employees to a new opportunity in your company. Yet, you may not always be able to elevate your workforce to take on these new roles.
Increase in cyber security protection required. As we connect our equipment to the internet there are dangers associated. Companies should invest in protecting their data assets against cyber risks.
In the end, we must find a balance. Consider how you will proceed.
- Carefully select the areas that will most positively gain from automation.
- Train and reskill employees. Don’t make it about simply reducing head count.
- Collaborate with technology partners. You don’t have to go it alone. There are engineering teams dedicated to providing automation solutions. Take advantage of their experience. I’ve seen companies try to keep their automation and engineering projects internal and then repeat the same mistakes others have made.
- Find a partner you can work with and leverage experience. Balance confidentiality with sharing technology. There are times when specific pieces of the puzzle are unique to one customer, but often the bigger picture automation works for the broader market.
Overall, many companies in the filtration industry are still doing the same manual processes. When working with an automation partner, broaden your scope to include improvements in other areas in the future.
Many times, one project leads to another. Planning for it ahead of time can save money later. Automation empowers your production efforts to be ready for growth and potential opportunity. It is the future.